Why there's a revolution on the way in glass making
- Published
- comments
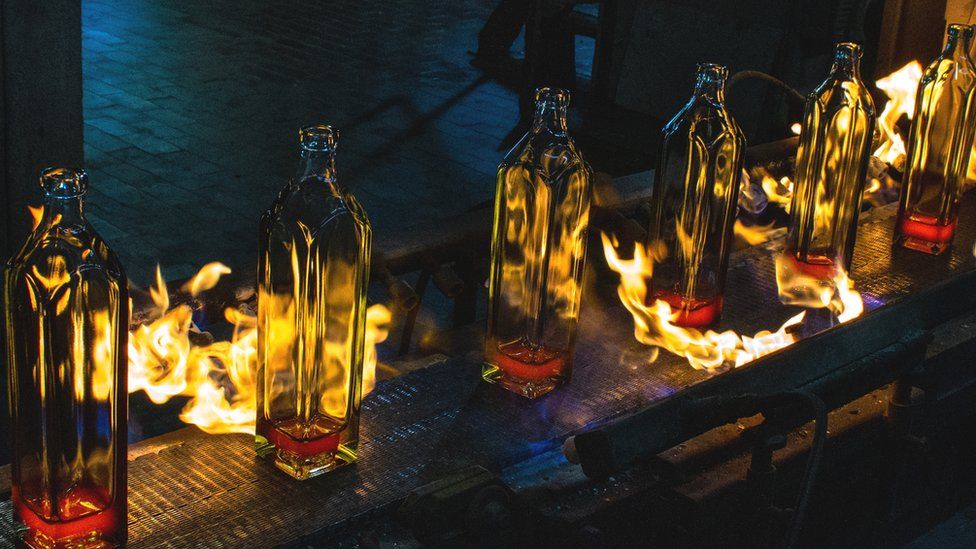
Making glass bottles is an energy intensive business
I'm handed an elegant pear-shaped bottle with an intricate leaf pattern reaching up around the neck.
Despite being empty, it's heavy.
I ask how much the bottle costs. "About £270," I'm told. I hand the bottle back - very carefully.
The bottle, designed for a rare whisky, is one of the creations of Stoelzle Flaconnage, based in Knottingley, West Yorkshire. Glassware has been made on this site since 1871.
In 1994 the factory was taken over by Austria's Stoelzle Glass Group, which has focused the plant on making bottles for the spirits industry.
It can handle the design, bottle making and decoration all on one site.
Demand is strong, helped by the boom in gin making and demand for whisky in Asia. When I visit, the plant is busy, lumps of molten glass are dropping into dozens of moulds, the glass still glowing orange from the heat of the furnace.
To stand out in a crowded market, customers want distinctive bottles, with patterned and sometimes coloured glass, elaborate labels and artwork.
"What our clients are looking for is to have their product presented in an outstanding - sometimes iconic - way," says Thomas Riss, chief executive of Stoelzle Flaconnage.
To make glass the raw materials have to be heated up to 1,500C
While business is brisk, Stoelzle Flaconnage - and other glassmakers - are having to make some big decisions about the way they make glass containers.
The European Union is cracking down on packaging waste. It wants packaging to be lighter so less material is needed and less fuel is needed for transportation.
It has been working on the Packaging & Packaging Waste Regulation (PPWR), which is in the final stages of approval.
Under the rules, member states would have to cut back on packaging weight and would have to introduce measures to meet targets.
There is concern in the glass container industry that it will be unfairly targeted as glass is relatively heavy, compared with plastic or aluminium.
"Light doesn't mean sustainable," points out Vanessa Chesnot, from FEVE, the industry body which represents European glass container makers.
"Glass is 100% and infinitely recyclable... so, you can recycle a whisky bottle into another bottle, forever basically."
While it's true that glass recycling is an established process, making glass, even using recycled materials, is energy intensive.
Most glass making involves burning natural gas to heat the raw materials in a furnace to 1,500C. Burning gas and heating the raw materials both produce CO2.
Thomas Riss plans to open an electric furnace in 2026 at the Stoelzle plant in Knottingley
The furnace I saw in action at Stoelzle Flaconnage uses about 191,000 kWh of energy per day - that's enough to supply the average UK household with energy for 12 years, the company says.
It is considered a relatively small furnace; bigger plants would have furnaces twice the size.
What's more, glass furnaces are never turned off, as it takes 12 days for a furnace to reach its operating temperature. Essentially a furnace will run all day, every day for its operational life - typically between ten and 12 years.
So the glass industry is looking at switching from gas-fired furnaces to electricity.
If the electricity comes from a sustainable source then the carbon footprint is slashed, which could go a long way to helping glass firms meet their goal to become net zero by 2050.
Until recent years, running a furnace on electricity was considered too expensive. But electricity prices have become more competitive, so glass makers are looking at making the switch.
Stoelzle Flaconnage, plans to have an electric furnace running in Knottingley by 2026.
"When I talked with my engineers, five years back, none of them would have ever come up with the idea of electric furnaces, because the mathematics didn't make sense. But this has changed now," says Mr Riss.
However, electric furnaces might not be an option for companies that mass produce containers, like beer bottles. Even if electric furnaces can be made big enough, the extra expense of electricity will be off-putting for them.
"For the time being it [electric furnace tech] is mainly being developed for niche markets or small furnaces producing high added value products," says FEVE's director of environment, health and safety, Fabrice Rivet.
An extra challenge for electric glass furnaces is plugging them in. Connections to the electricity grid often have to be upgraded, to cope with the extra electricity supply.
But the glass industry is attempting to clear some of those hurdles.
Ardagh Glass Packaging is making glass with Europe's first hybrid furnace
In Obernkirchen, in northern Germany the world's most advanced hybrid glass furnace is undergoing trials, at Ardagh Glass Packaging (AGP).
Partly funded by the German government and the EU, and made by Germany company Sorg, it is a large furnace with a capacity of 350 tonnes - enough to make about a million beer bottles a day.
When fully operational it will run on 80% sustainable electricity and 20% gas, which AGP says will save 45,000 tonnes of CO2 per year.
Engineers at AGP are giving the furnace the ultimate test - making amber-coloured glass, which involves tricky chemistry and is more difficult to control than making clear glass.
"There has been no successful demonstration of full-scale amber glass production in full electric melting. And if you wanted to combine the maximum of carbon footprint reduction with high cullet (recycled glass) and amber glass, then the hybrid is the logical choice," says Joris Goossens, research and development project manager at AGP.
AGP says that once the hybrid furnace has proved itself, then the next step could be replacing the natural gas with hydrogen.
Even if the industry does make the switch to electric or hybrid furnaces, it still has other problems to solve.
The raw materials needed to make glass, including sand, soda ash and limestone, emit CO2 while they are being heated. They account for about 20% of the carbon emissions of the glass making process.
The industry hopes that using more recycled glass in the production process will cut those emissions, but getting enough unwanted glass is a challenge.
One academic who has studied the packaging industry says the answer might be just to use less glass.
In a paper published in 2020, Alice Brock, a PhD researcher at Southampton University, compared the environmental impact, external of glass, plastic and aluminium containers and found that glass had the most detrimental impact on the environment.
"Even recycled glass has an incredibly high energy demand," she points out.
"The waste hierarchy is reduce, reuse, recycle. We should have less packaging, or we should be reusing packaging, or we should recycle if we have to," she says.