Queen's Baton Relay: Designing the Queen's Baton
- Published
The Story of the Commonwealth Queen's Baton
Constructing an item which will reach a global audience of almost two billion people is not an easy task, but it was a challenge Will Mitchell was excited to accept.
When Glasgow-based firm 4c Design won the tender to create the Queen's Baton, the Design Director knew it was important to find the correct inspiration.
The team always had an idea in mind and a range of traditional and cutting edge production techniques were used to construct the baton.
Direct laser metal sintering was used infuse 4,500 layers of titanium together. This technique is normally dedicated to aerospace prototypes, sculpture and jewellery.
"This has never been done before with a baton design," said Will.
Layers of titanium powder, as thick as a human hair, took 30 hours to form into the baton.
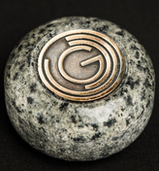
There is a gemstone gift for each country
He added: "The process has been around for a long time, we were pushing the technology. The people who made the metal work were pretty sure it would fail.
"This baton is one of the largest items the company has made. The complexity and thickness made the building process very unpredictable. As you built the part, it became very hot and cooling temperatures meant things can warp."
In stark contrast, a traditional boatbuilding technique called bird-mouthing was used to shape the baton's handle.
Elm wood for the handle was sourced from the Isle of Cumbrae, keeping the materials close to the desired Scottish connection. Granite gemstones, which will be given as a gift to each nation, are from Ailsa Craig in the Firth of Clyde.
At the top of the baton is a granite ‘gemstone’, which will be given to each nation and territory. The stones come from Ailsa Craig in the Firth of Clyde and have been crafted by Kays of Scotland and jewellers from Glasgow School of Art.
The gemstone can only be removed by opening a clever puzzle mechanism.
The lattice frame is inspired by Glasgow's industrial and architectural heritage. A process called direct metal laser sintering was used to create its organic shape by fusing together layers of pure titanium powder.
Inside the baton is a message from the Queen, written on parchment handmade in Glasgow from linen and plant fibre. Sealed with the royal seal, the message forms the 'visual core' of the baton, illuminated from within by LED lights.
The elm handle is crafted from wood from the grounds of Garrison House on the Isle of Cumbrae, and represents Scotland's natural resources. It was constructed using a boatbuilding technique known as "bird-mouthing", traditionally used to make ships' masts.
This is the first time the Queen's message has been a visible element of the baton. Will is proud of the companies achievement and hopes to leave a legacy for future baton designs.
This time around the design has gone back to basics and is modelled on an athletes' baton reminiscent of the original design in the 1958 Queen's Baton Relay.
Will said: "I was very keen to get a story together about the baton. The organising committee at Glasgow 2014 wanted references to Scottish and Glasgow culture."
'Culture', 'sport' and 'message' were the three key drivers for the inspiration of the baton.
"This has been our first mainstream project," added Will. "It is part of the Commonwealth Games and it has been absolutely amazing to make that association."
The baton will travel to Scotland on Thursday before heading to India for its first international stopover on 11 October.
- Published9 October 2013
- Published9 October 2013
- Published16 August 2013
- Published9 October 2013