Japan parts shortages highlight global reliance
- Published
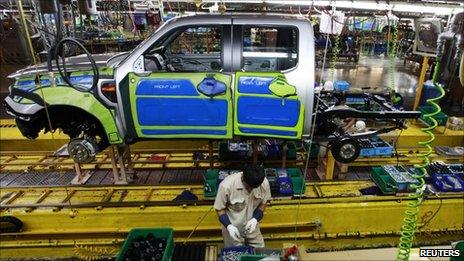
Carmakers need the right components delivered in the right order to complete each vehicle, which can contain some 20,000 parts
When the earthquake and tsunami hit Japan on 11 March, a metaphorical demolition ball was released.
The wrecking ball is still in motion, its pendulum movement about to create havoc as it crashes ever deeper into the global industrial landscape.
Dwindling supplies of components will inflict huge damage everywhere. Firms across the world fear shortages of parts that used to be made in the Japanese factories now shuttered because of power and water shortages, or because of road and port closures, following the quake and the floods.
And carmakers, whose products often contain some 20,000 individual parts, are expected to be among those worst hit.
"This isn't as straightforward as assembling the iPad 2," observes Brian Johnson, a motor industry analyst at Barclays Capital.
A matter of time
In Japan, dozens of carmakers, component suppliers and electronic firms have shut down both factories and showrooms - with Goldman Sachs estimating that the closures are costing the country's automotive industry some $1.4bn (£875m) per week.
Globally, prices have been rising in response to fewer cars going on sale, with car dealers reining in discounts. In turn, this has sent second-hand prices higher.
"Everyone is putting on the brakes a little bit and taking a look to see where they are affected," observes IHS Automotive analyst Paul Newton.
But outside Japan, the wrecking ball has done little actual damage so far.
Parts rationing has started, with some carmakers having cancelled shifts, slowed down production and delayed new model launches over the past couple of weeks. Others have warned of trivial shortages, such as certain paint colours.
Nobody doubts, however, that it is only a matter of time before it hits.
Mr Newton says it could take another month or so before we see the true impact, while doomsayers such as Koji Endo, managing director at Advanced Research Japan in Tokyo, goes as far as predicting it will have "the biggest impact ever in the history of the automobile industry".
Switching suppliers?
One might think that time would be a great luxury in circumstances such as these.
Given time, surely manufacturers in the US, Europe and the rest of the world could knock up replacement parts - whether microprocessors or steering wheels - somewhere else in the world?
But the answer is as simple as it is complex.
In practice, many car parts could be replicated with relative ease by rival parts suppliers or in carmakers' existing factories outside Japan.
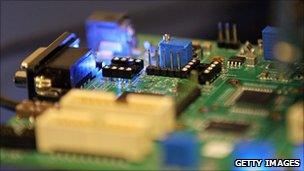
Semiconductor shortages have hit carmakers and other industries across the world
Sure, new tooling might be required, staff might need to be retrained, and there might be cost implications.
But mass-producing steering wheels or microprocessors, gear boxes or window wipers, is still relatively easy.
At least, that is, when compared with safety legislation and corporate law.
Legal complications
Whether companies outside Japan should switch suppliers could be seen simply as a moral question, relating to the rights and wrongs of solidarity in the world of business.
Carmakers such as Toyota or Honda might prove more loyal to their suppliers than those without cultural or national ties to Japan, though this is not a given.
But it is also a question of ownership. Under patent law, for instance, a carmaker might not own the rights to produce its own voltage regulators or lithium ion batteries - the patent might be owned by a supplier that is currently struggling with a shattered factory.
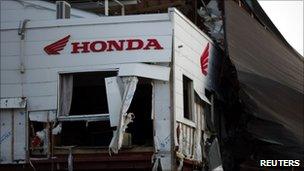
Japan's car industry needs to be rebuilt to revive global parts supplies
Indeed, even if a company owns the copyright of a part made by a supplier, it might find it hard to switch because of existing contractual obligations: The company might still be bound by agreements with the stricken supplier, even though their deliveries have been temporarily halted.
And off course, it is also a question of safety - or at least safety regulation. Any replacement parts would require type approval, which would invariably be a phenomenally costly and time-consuming affair.
For instance, according to one carmaker in the UK, merely using a different type of leather in the cockpit of one of its models would require a series of air bag crash-tests to be carried out at £30,000 ($48,000) apiece.
Short-lived crisis?
With the global car and technology industries' dependence on Japan established, it is clear that the next few weeks will prove painful for many as actual shortages will force firms to mothball their plants.
"You will see it happen almost daily," says Mr Newton, predicting that actual vehicle production will fall some five million short of a previously predicted production target of 72 million vehicles.
But the shortages are expected to last weeks rather than months, with some carmakers - such as Volkswagen and Peugeot Citroen - insisting they will not be affected.
Moreover, the length of the crisis may soon become highly transparent.
Currently, carmakers around the world are receiving supplies that were stashed on board ships ahead of the quake and tsunami.
These ships tend to be slow, so the last ones should be delivering parts perhaps as late as May.
By then, some industry observers expect new shipments to get under way too, with delivery dates a few weeks later.
Carmakers around the world hope they are right.