UK hand in glove with Ethiopia's booming leather sector
- Published
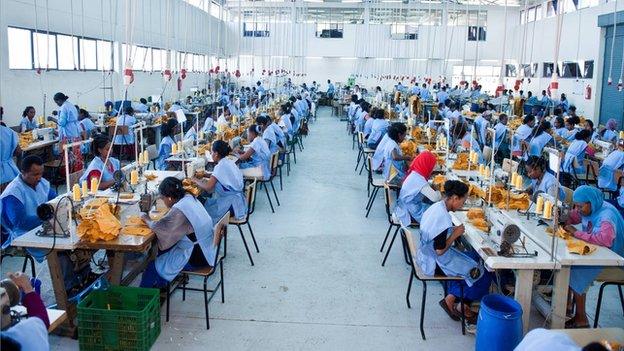
Pittards plans to substantially increase the size of its Ethiopian workforce
Amid the rhythmic clicking of rows and rows of sewing machines, hundreds of workers are busy creating a range of leather gloves, bags and jackets.
"I can tell when employees' skills have improved by the noises of the machines speeding up," says Tsedenia Mekbib, a general manager.
We are at a busy factory on the outskirts of the Ethiopian capital, Addis Ababa.
It is one of three such facilities in the city owned by UK leather goods company Pittards, which has a long history of operating in the country.
While an increasing number of Western firms of all sizes are now looking at doing business in Africa, Pittards has had a 90-year head start.
The company, which is based in Yeovil, Somerset, in the south-west of England, has been trading in Ethiopia since the 1920s. And it is all down to a celebrated type of sheep - the Ethiopian hair sheep.
This breed, which does not grow a thick coat of wool, also has much thinner skin than its European brethren, making it ideal for delicate leather apparel such as ladies' gloves.
New factory
Pittards now has ambitious plans to grow its Ethiopian operations, which help contribute towards the firm's £39m ($60m) annual revenues.
At present its Addis Ababa-based factories and tannery to the south of the city employ about 1,200 locals, a number expected to grow to about 5,000 within five years. A fourth factory has already been built, and is waiting to be occupied.
On the current production floors, an element of handwork is also included in the manufacturing process, which each month produces 100,000 work gloves and 5,000 dress gloves.
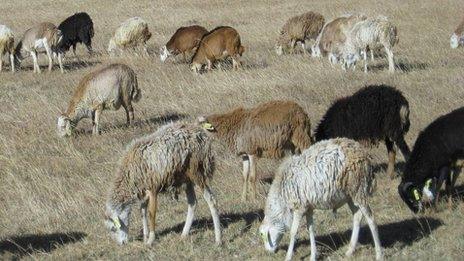
The Ethiopian hair sheep is much in demand in the leather industry
Pittards' Ethiopian factories also produce two million sq feet (186,000 sq m) of quality leather for export to be made into garments ranging from specialist golf gloves to couture handbags.
"Ethiopia will grow in importance to Pittards and the global leather industry [in general]," says the company's chief executive Reg Hankey.
Ethiopia's attractions for Pittards, and other Western firms, include the country's large pool of relatively low-cost labour. It also has duty-free status for most manufactured products for export to Europe, the US and other countries.
Animal husbandry
Despite Ethiopia having the largest flock of hair sheep in the world - more than 26 million - it is not the largest supplier of skins.
Its flock's reproductive rate of about 37% trails New Zealand's 180% and means Ethiopia has only some 9.5 million sheepskins available annually compared with New Zealand's total of about 30 million.
Better animal husbandry should increase Ethiopia's supply. Pittards is already involved in environmental programmes to improve the quality of local skins through improved husbandry and treatment against parasites.
Another benefit could be improved meat yields, a not insignificant detail while Ethiopia remains a developing country.
Regarding the wider issues of doing business in Ethiopia, Mr Hankey says the country faces the same challenges as other developing nations, encompassing difficulties related to bureaucracy, customs and banking. Yet, he adds, while more has to be done, the situation is greatly improved.
"Ethiopia has come a very long way over the last 23 years since I first visited, and the last decade in particular has witnessed massive positive changes," Mr Hankey says.
"Ethiopia has worked very hard to establish itself as a preferred country for economic development within Africa."
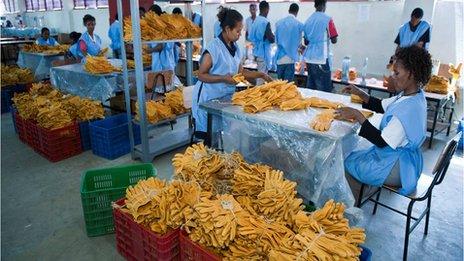
Pittards' Ethiopian operations are now a core part of its business
Ethiopia's government now wants to grow its leather industry's annual exports to $500m by the completion of its five-year growth and transformation plan at the end of 2015. Leather exports stood at $123m last year.
Within Pittards, the British management is happy to be playing a part in Ethiopia reaching its ambitious goal.
"We have put down roots," Mr Hankey says. "This changes relationships and thinking - we see things from the inside and the outside, giving us a unique position for further development."
'Changing lifestyles'
Busy at work in the Pittards factory is 20-year-old Embret Beshada.
Her job is to sew two glove-shaped panels together while incorporating material to create a thumb casing.
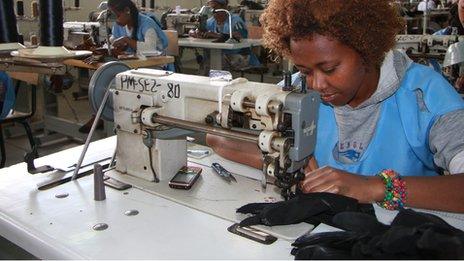
Embret Beshada likes the financial indepedence having a job gives her
She says she found the work easy when she started just over a year ago, despite having to learn many new skills, and was producing gloves within two months.
"Being able to support myself excites me the most," she says.
Sitting at sewing machines nearby are some of her friends. About 80% of the factory workforce is female, while at the tannery about 80% of the workforce is male.
"We are seeing people get more jobs, and people's lifestyles changing, which gives us hope for the future," Ms Beshada adds.