Retrofit for purpose: Old buildings get a green facelift
- Published

The retrofit of Waltham Forest College has helped reduce energy costs by £127,000 a year so far
One of the best ways of reducing energy consumption and saving money is retrofitting - in effect, adding new tech to old kit.
Technologies, such as thermally-efficient cladding, LED lighting, heat exchangers and smart metering, could save UK businesses £3bn to £5bn a year, according to the Carbon Trust, the energy saving advisory body.
Old buildings are leaky, wonky and inefficient with heating, cooling and lighting systems that often work in competition with each other rather than in harmony.
We can either knock them down and start from scratch - an expensive and often impractical option - or use what technology we have to give them a green facelift and bring them into the 21st Century.
Waltham Forest College, a further education college in North East London with buildings dating from the 1930s, has managed to reduce energy costs by 25% so far - or £127,000 a year - following an extensive retrofit programme involving new cladding for "1960s excrescences", double glazing, solid wall insulation and a heat exchange system for the swimming pool.
The project recently won Non-domestic Retrofit Project of the Year at the 2013 Retro Expo awards.
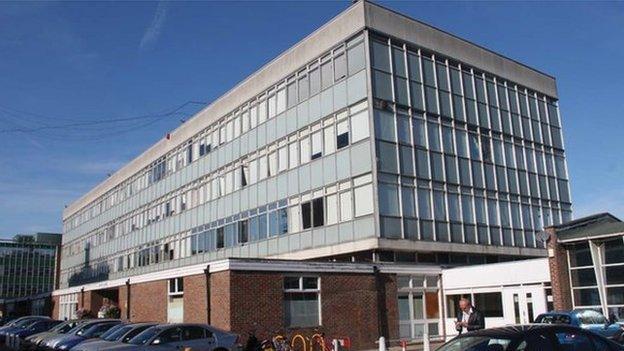
Waltham Forest College's Lowery Building: Before its facelift...
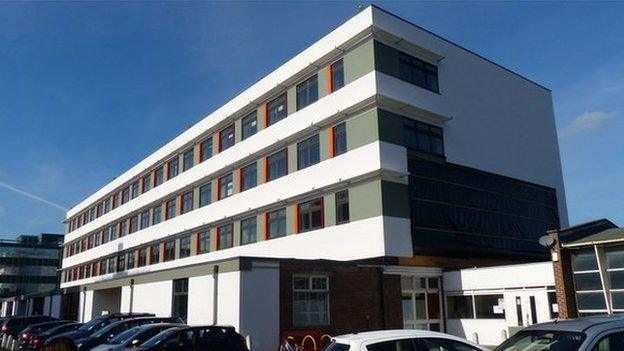
Waltham Forest College's Lowery Building: After its facelift
"We're aiming for zero carbon emissions by 2016," says Richard Hopkinson, the architect overseeing the project in collaboration with Platform 5 and Waltham Forest College's in-house team.
Changing the college culture towards sustainable energy use has been as important as the physical upgrade, he argues.
"Now that people see how their run-down building is being cared for again, they're taking far more care over how they use energy," says Mr Hopkinson.
The next phase of the £35m project will see a switch to a gas-fired combined heat and power system that will use waste heat to warm the swimming pool and then extract heat from it overnight, as well as a new centre for engineering excellence.
Precision engineering
Gumpp & Maier UK was another Retro Expo winner for its timber-based energy system (TES) facade - a sort of precision engineered, thermally-efficient cladding.
"Creating an air-tight layer is always the most difficult bit of retrofitting," says Martin Montgomery, the firm's UK managing director, "because old buildings are not uniform - they lean and the walls are never straight."
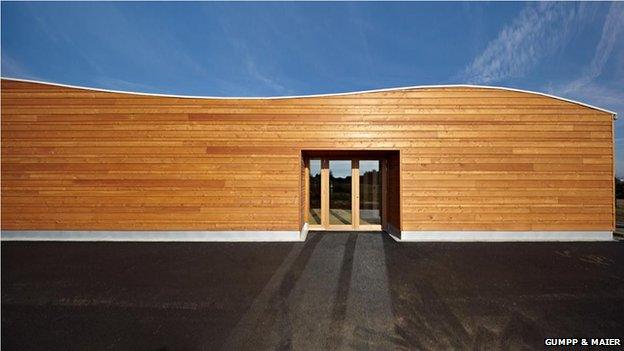
Kindergarten, Yutz, France: Pre-fabricated wooden cladding can be thermally efficient and beautiful
This entails building up a highly accurate 3D model of the building using traditional surveying technology, such as a theodolyte, with newer gizmos, such as mini-helicopter drones equipped with laser scanners.
The 3D model, which can take months to develop, is then transferred from computer-aided design software to computer-aided manufacturing software for off-site pre-fabrication.
The complicated jigsaw puzzle of parts is then assembled on-site without the occupants having to vacate the building, thus minimising disruption and saving time and money. Mr Montgomery says the company recently clad 400 sq m of a building in six days. A typical terraced house would take about four days, he says.
The cladding is essentially a sandwich of thermally efficient materials, including double or triple glazed windows, that creates an airtight shell around the existing building to retain heat. This can reduce energy consumption by as much as 10 times, he says.
Referring to the firm's current £2.8m social housing project at Parkview Hub, Thamesmead, south-east London, he says: "Residents currently spend about £40 per week on their gas bills. After the retrofit the bills should come down to about £4 per week."
But the technology isn't cheap - £30,000 to clad the typical terraced house, for example - which is why Gumpp & Maier is focusing on office blocks and factories that can afford to spend about £1m to £2m improving their energy efficiency.
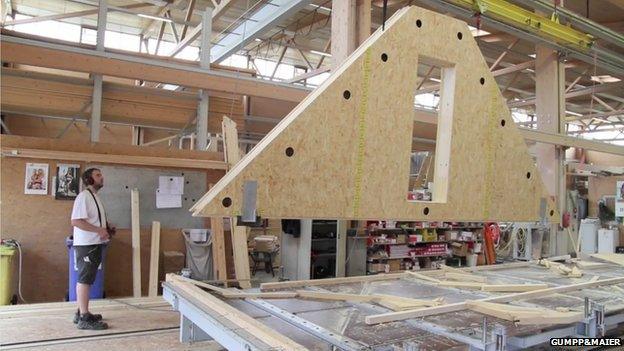
Gumpp & Maier's thermally-efficient panels are manufactured off-site
"Other cladding products, such as polystyrene that you simply stick on to existing walls, may be cheaper," Mr Montgomery admits, "but they're certainly not as effective."
The company claims its TES technology can bring buildings up to EnerPHit standards - the equivalent of "Passive House" certification for refurbished buildings. Technically speaking, this means the building's specific heat demand falls to 25kWh/m2 per year or less. In other words, the building is so well insulated traditional heating systems become virtually unnecessary.
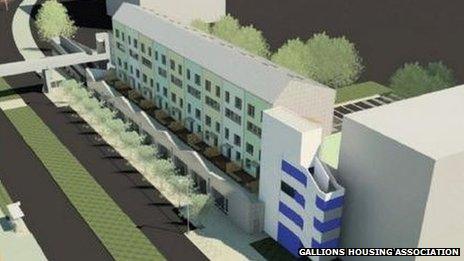
Parkview Hub housing development will be wrapped in Gumpp & Maier's insulated timber panels
"We thought [TES] was innovative, flexible, widely applicable and contributing to very high energy performance as well as economic retrofit at scale," the Retro Expo judges said.
Seeing the light
Myles McCarthy, the Carbon Trust's director of implementation, says rising energy costs are a key driver in the retrofit movement.
"Over the past 10 years, the cost of energy has roughly doubled and the government's forward projections suggest these prices will increase by a further 50% over the coming 10 years," he says.
One of the simplest and most cost-effective retrofits is to replace old lighting with the latest LED bulbs and controller technology, argues Mr McCarthy.
"A business, such as a warehouse or large hotel, can save up to 70% of its electricity costs by switching to LED lights with motion sensors," he says, "and receive a payback on the capital outlay within two years."
Longer-life bulbs reduce maintenance costs as well, he added, and replacing them causes minimal disruption to the business.
The bottom line is that greener businesses are more competitive businesses, he argues.
Retrofitting may sound backward, but it could give your business a sustainable future.