Why carmakers have the most to fear from protectionism
- Published
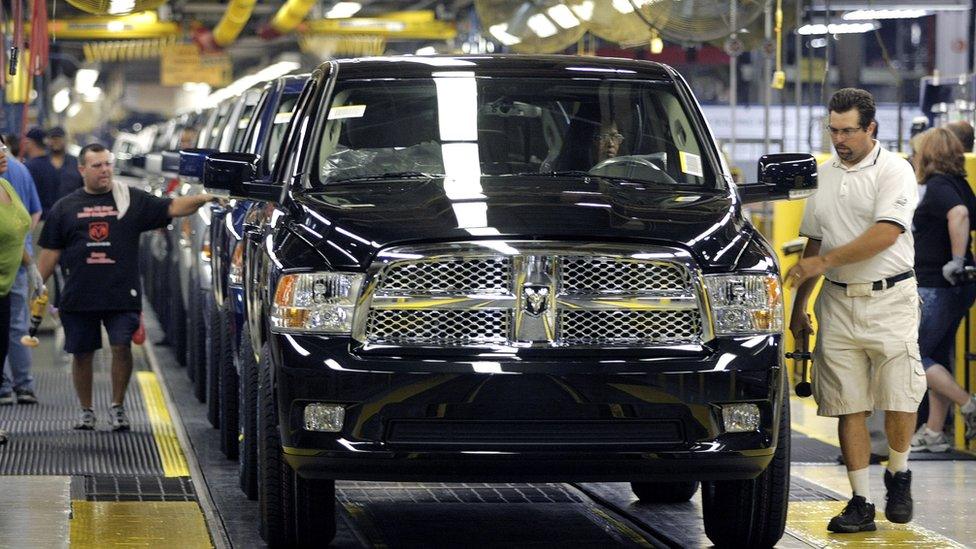
The Dodge Ram 1500 - made in the USA? Not entirely
Few places have "Made in America" written all over them like the Warren Truck Assembly Plant.
They have been making trucks at the factory, outside Detroit, since 1938, and you don't get much more American than the chunky, no-nonsense, big-tyred Dodge Ram 1500s that roll out from the 87-acre site every day.
So if I want to buy American, surely I can do no better than buy a Ram?
Well, no. Actually you'd be better off buying a Honda.
The Kogod School of Business at American University in Washington DC compiles an annual index, external of the cars Americans drive - and where they are made.
The Dodge Ram 1500 turns out, according to this index, to be only 59.5% made in America.
The Honda Accord, says Kogod, is 81% American.
Now this is partly because some of the Ram 1500s are made not in Detroit at all, but in Saltillo, Mexico.
And then there is the fiendishly complicated issue of components.
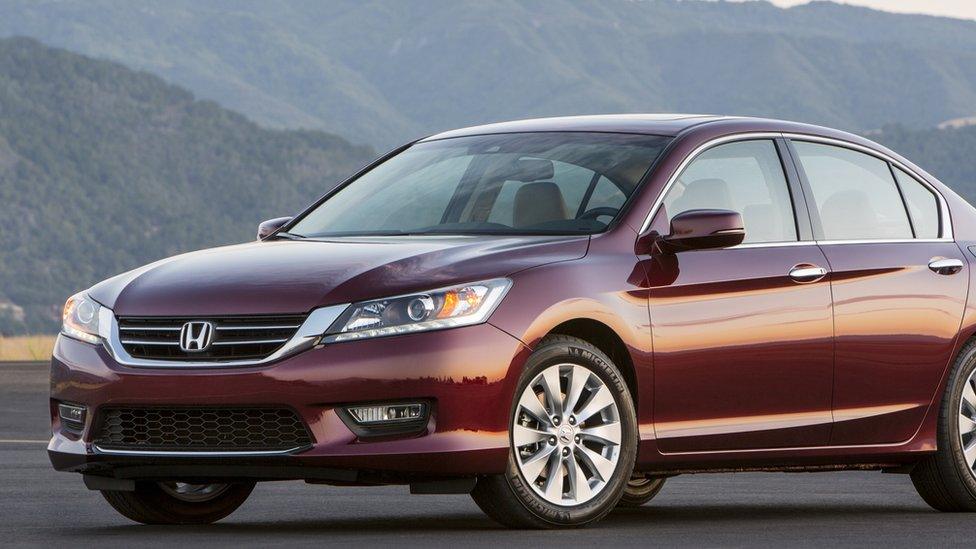
The Honda Accord is 81% American, according to the Kogod School of Business
Fiat Chrysler Automobiles (FCA), which makes the Ram, has a huge supplier network that buys in parts and manufacturing from around the world from Cordoba in Argentina to Serbia and South Korea.
It's not just FCA, globalisation is in the lifeblood of the car industry, and its supply lines have become possibly the most complex and finely tuned of any business on the planet.
Now this model is under threat.
In the US, President Trump has pledged to hike tariffs on US cars made abroad, or as he succinctly tweeted, external: "Make in U.S.A. or pay big border tax!" This, he believes, will save American jobs.
Mr Trump may well have caught hold of a global zeitgeist. Before the US election, the World Trade Organization (WTO) reported a spike in trade-restrictive measures imposed by members, averaging 22 per month, the highest since 2011.
"In the current environment, a rise in trade restrictions is the last thing the global economy needs," director-general Roberto Azevedo said.
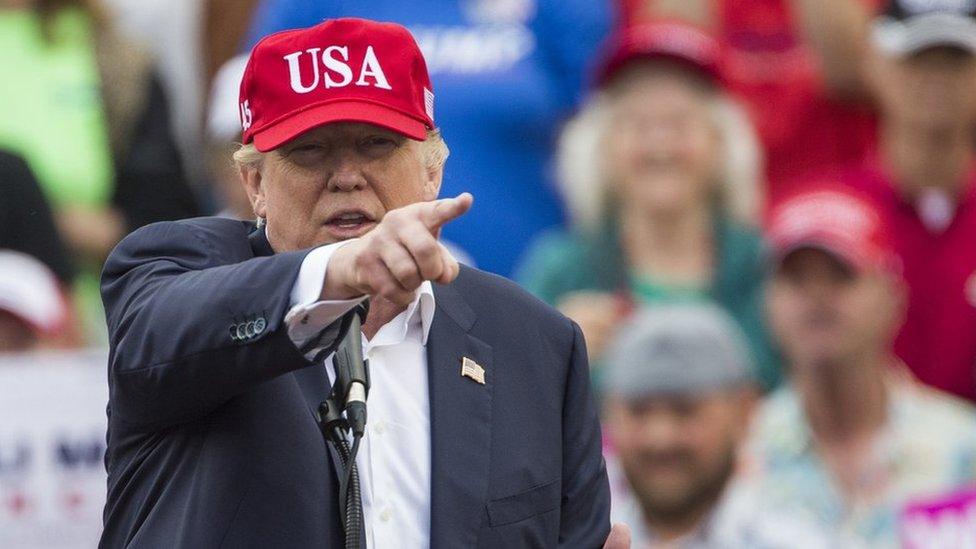
Trump: Protectionism by tweeting
But the carmakers appear to be buckling under, and scrambling to polish up their Made in America badges. Ford, for instance, scrapped a plan to build a plant in Mexico and got tweeted a pat on the back, external from the president.
Despite the hype, Ford's decision to build in Michigan is a minor tweak in its global strategy. But if border taxes on car imports work their way from angry tweets to real legislation, the global motor industry is in trouble.
One firm ignoring President Trump's criticism is German car giant BMW, who recently announced plans to retool its factory north of Pretoria in South Africa to produce the X3 sport-utility vehicle outside the US for the first time. BMW is also building another Mexican plant in San Luis Potosi.
Ian Robertson, head of sales and marketing at BMW, points out that its Spartanburg plant in South Carolina in the US is the biggest of all its factories, and says its decision to build the San Luis Potosi plant simply reflects how the industry works.
"This is part of the normal business development of a company like BMW which has nearly 30 production facilities in 14 countries. And the Mexican investment is one in a plant which will produce a capacity that will ultimately supply many markets."
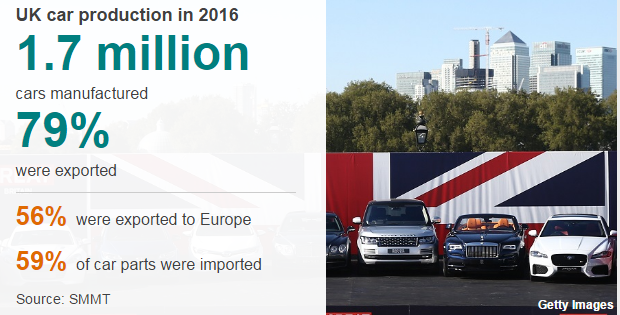
In the UK, the making and selling of cars is similarly global. Last year, which was not untypical, the majority of cars made in the UK were exported, while most of those sold (86%) were imported.
Few UK politicians are making Trump-like calls for protectionism, but if the Brexit process ends up with the country pulling out of the EU single market, as Prime Minister Theresa May has indicated, it could still lead to tariffs on imports and exports, and hobble the car industry's cross-border supply chains and sales.
"Year-on-year exports have driven the car industry, and with so much content sourced internationally, we are massively dependent on zero tariffs and a customs union," says Tamzen Isacsson, communications and international director at the Society of Motor Manufacturers and Traders (SMMT).
If tariffs based on WTO rules were applied to cross-border car and car part sales, the SMMT estimates the price of an average imported car would rise by £1,500, while overall costs would rise by at least £4.5bn ($5.6bn) a year.
But possible tariffs are not the only problem.
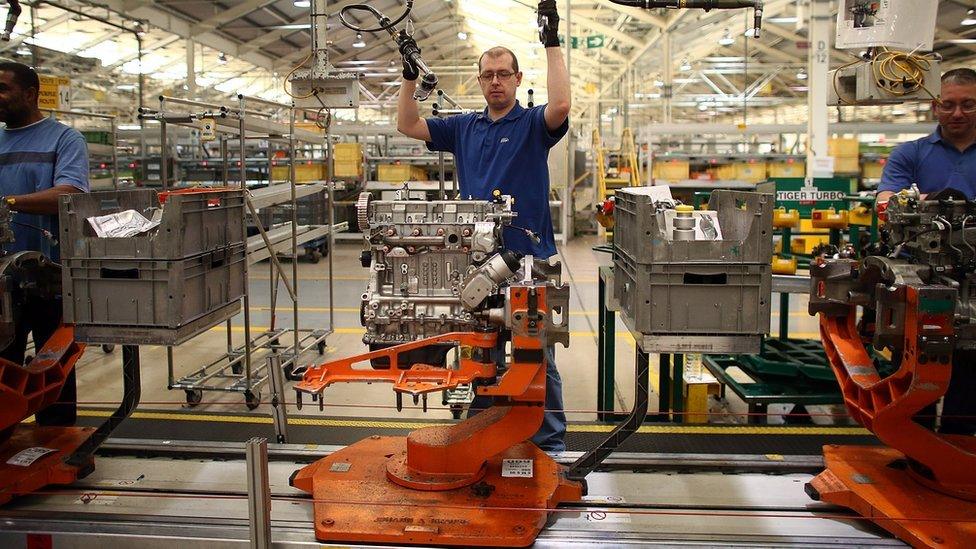
UK car production is globally integrated
Modern car manufacturing is built around just-in-time manufacturing (JIT), developed over the last 60 years under various names like "lean manufacturing" and "quality circles".
They all have the same core purpose - to minimise waste by keeping inventory at very low levels, alerting suppliers at exactly the point when new parts are needed.
The flipside of JIT is that a delay can wreak havoc on the whole operation.
When a fire closed the Channel Tunnel in 2015, UK car plants, starved for just a few hours of their supplies, were forced to hire private jets, external to intercept trucks en route to the UK to make sure components arrived on time.
"Many manufacturers carry stock to last them no more than four hours, so they are utterly dependent on rapid, fast-flowing content from the EU," says Ms Isacsson. "If you have delays with tariffs and cross-border checks the costs mount up and in an intensely competitive environment you suddenly find you cannot compete."
While the possibility of doing a free trade deal with the EU for the car industry would keep the wheels of trade turning, identifying which imports and exports were for the car industry and which weren't would be difficult.
"It would be easy to identify an engine, a turbo-charger, but we also buy in steel, we buy chemicals, we buy glass, we buy engine control units. How would you be sure that those particular products are going to go into the automotive sector, rather than another sector?," says SMMT chief executive Mike Hawes.
Ultimately, unwinding the labyrinthine supply chain of the car industry to work out what to tax and where could prove the biggest deterrent to new tariffs.
- Published3 January 2017
- Published6 January 2017
- Published5 January 2017