From garden chairs to boxes: Five items in short supply
- Published
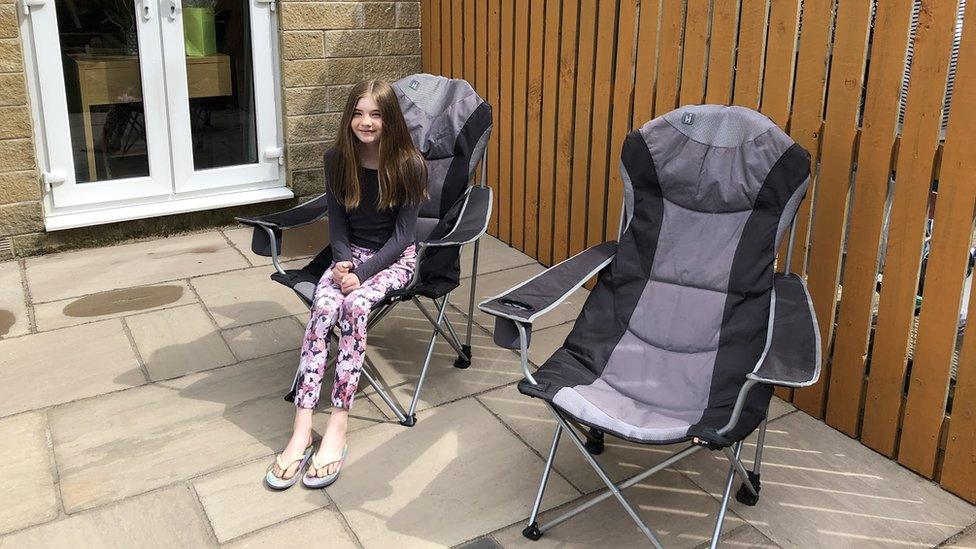
Sophia and her family are making do with camping chairs while they wait for their new garden furniture
Shortages of garden furniture, building supplies, cardboard and other packaging are causing a headache for business and consumers as summer looms.
A combination of problems - including port delays due to Covid measures, a surge in online orders during lockdowns, the burden of Brexit paperwork and disruption to the Suez canal - has increased competition for shipping container space and delayed delivery times.
1. Garden Furniture: 'We're having to use camping chairs'
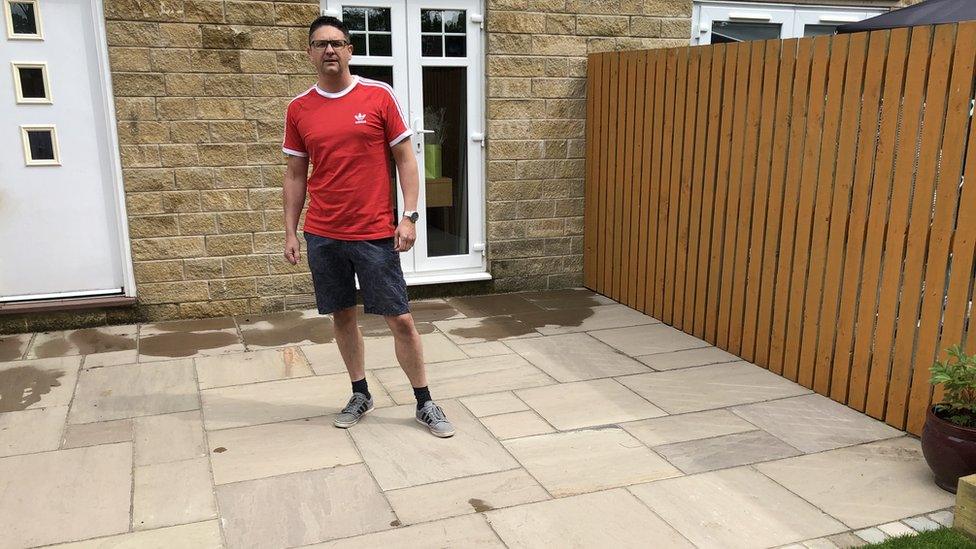
Richard is waiting for his new garden furniture
Richard from Ilkley in West Yorkshire and his family are making do with camping chairs after his garden furniture order was delayed.
He is still waiting for a corner sofa, glass top table and three stools from furniture company Mattressman.
He paid £839 upfront in March and was told the furniture would arrive by 6 May.
"After contacting the company again to try to establish what was going on, we discovered that the furniture had arrived but was sitting in a shipping container, so we couldn't get a delivery date."
Richard, who has now been told his order will not arrive until August, said he was "very disappointed and upset".
Mattressman's spokesperson told the BBC: "It's an industry-wide shipping issue across the board and we're working closely with lots of suppliers to provide as much clarity as we possibly can."
The founder logistics app logistics app Annalise Davis said of the commodities she monitors, up to 94% are experiencing "extreme" port delays from mainland China.
More positive Covid cases have been identified in places such as Shenzhen, leading to tighter coronavirus measures at ports, according to a Maersk advisory, external.
2. Building supplies: 'I'm experiencing delays at all angles'
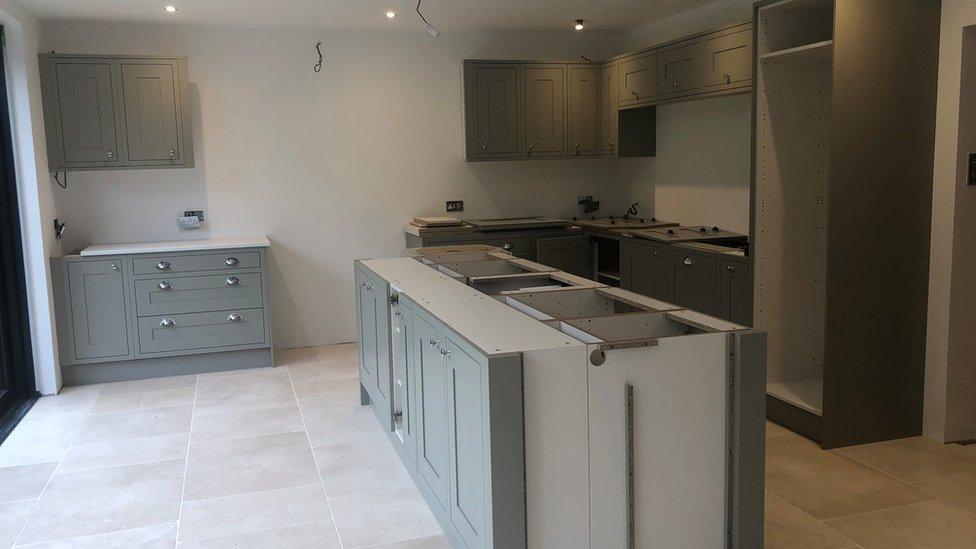
Chris Nutley's half finished kitchen
Chris Nutley, a building contractor based in Sussex, has been waiting for more than five months for an order to complete a new kitchen in his home.
"I'm experiencing delays at all angles at the moment, professionally and personally," he said.
Building materials are running short in the UK, putting construction companies under extra pressure.
Mr Nutley's firm is facing long waits for oak and timber imports due to a lockdown backlog and logistical problems from Brexit.
"There is currently more chance of buying an overpriced bag of cement on Facebook marketplace than at the usual merchant," Chris said.
Alex Veitch, general manager of policy at Logistics UK, said he was not surprised to hear there were some supply chain problems but said it was primarily due to businesses having to deal with extra administration.
"The paperwork required for these products is here to stay due to Brexit."
"Looking at evidence of the border flow, goods are moving well, but it's typically smaller businesses who have less experience with the paperwork, or have more complicated product ingredients, that are suffering more," he said.
But Mr Veitch said hold-ups caused by the Suez Canal jam and container delays between Europe and China were short-term problems which should be resolved in a few weeks.
3. Outdoor gear: 'We're paying $14,000 for shipping, up from $2,500'
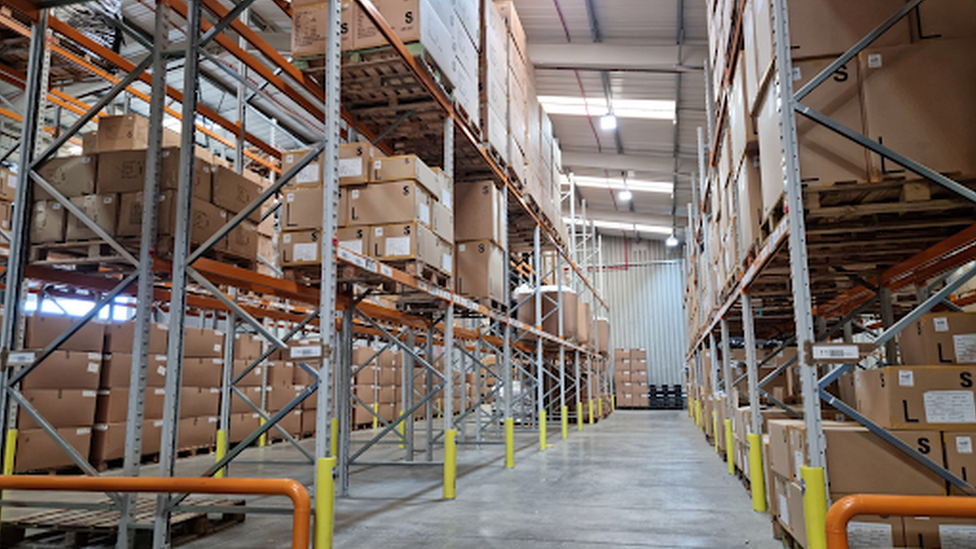
A Lowe Alpine warehouse with a low stock level
Camping and outdoor clothing have also experienced delays. Rab and Lowe Alpine chief executive Matt Gower said the company was being hit "quite badly".
"Shipments that used to take four weeks, now take eight and many aren't even sailing to the UK anymore."
"Last June we paid $2,500 (£1,800) per 40ft container, now we're paying $14,000."
Mr Gower said products would have to go up in price in the spring because of this added freight cost.
4. Cardboard boxes: 'We've switched to plain brown stock boxes'
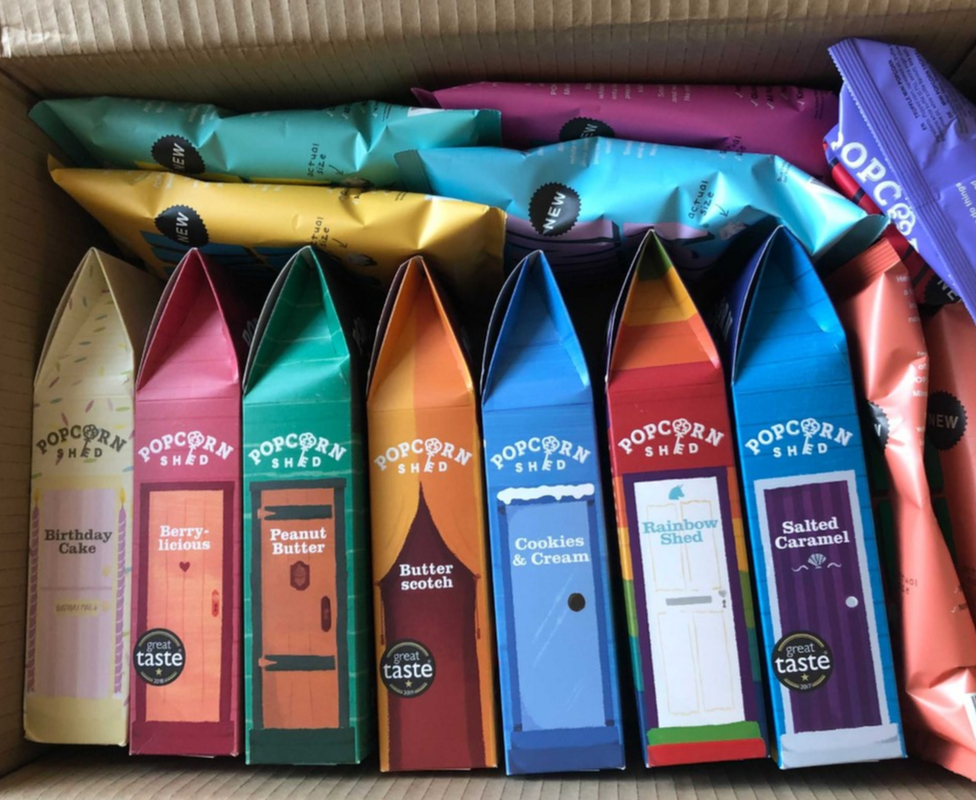
Popcorn Shed is using plain brown rather than branded boxes
Wholesale popcorn business Popcorn Shed has had supply problems since January.
"We're not able to get brand-printed corrugated boxes from any of our UK suppliers", director Sam Feller said.
Before Covid and Brexit, branded boxes would arrive three or four weeks after the initial order, but now "delivery dates bear no resemblance to when the order turns up" Mr Feller said.
Often the delays have come with a price hike because cardboard box manufacturers say they cannot get the usual material.
"Brexit delays and Covid issues have culminated in a perfect storm," said Mr Feller.
"We've switched to plain brown stock boxes and are larger too which means more pollution and wastage as a result."
5. Packaging: 'We've had to use larger size trays'
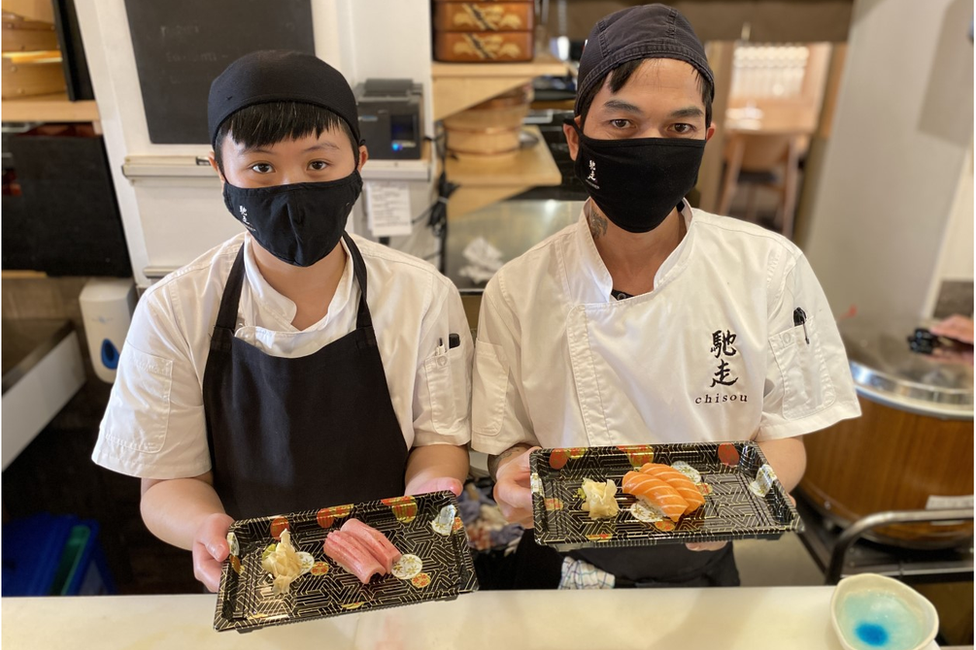
Sushi restaurant Chisou is using larger trays
Sushi restaurant Chisou has also had to cope with packaging shortages.
Its five sites in central London moved primarily to take-away during the lockdowns but the price of a tray and lid has risen from 15-20p to £1.
"We often use between 300 and 400 of these units a day per restaurant so can't afford that increase," said David Leroy, founder and managing director of Chisou.
After using the same takeaway packaging suppliers for more than 20 years, Mr Leroy said he had spent hours looking for alternatives but four out of five of them were out of stock.
"We've had to use larger size trays as those are all we can find, but this can cause issues when its being delivered as the food can move around and we don't want to start getting complaints," he says.
Prior to the lockdowns, Chisou had been trying to move to pulp and cardboard trays as this was more sustainable but have had to stay with the plastic trays.
"We wanted to choose a packaging option that's better for the planet but you've got to keep going as a business," Mr Leroy adds.
- Published7 June 2021
- Published26 May 2021
- Published31 January 2021
- Published22 January 2021