Bloodhound Diary: Speedy politicians
- Published
A British team is developing a car that will be capable of reaching 1,000mph (1,610km/h). Powered by a rocket bolted to a Eurofighter-Typhoon jet engine, the vehicle will mount an assault on the land speed record. The vehicle will be run on Hakskeen Pan in Northern Cape, South Africa, in 2015 and 2016.
Wing Commander Andy Green, world land-speed record holder, is writing a diary for the BBC News website about his experiences working on the Bloodhound project and the team's efforts to inspire national interest in science and engineering.
We've decided to start a "Top Gear" style leader board for the VIPs that have set a time on our Bloodhound Driving Experience, external.
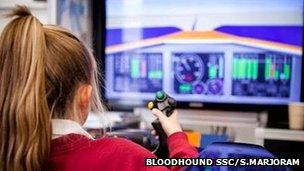
Get the experience: Bloodhound test drivers start young
The current list includes Baroness Scotland at 997mph, David Willetts (Minister for Universities and Science) at 1,003.3mph and William Hague (Foreign Secretary), who was - until recently - just in the lead with a speed of 1,003.6mph.
The Driving Experience has proved very useful to me as a cockpit development tool, but its real value has been in showing thousands of children (and politicians!) a little of what goes on in the cockpit during a Land Speed record run.
The FIA rules for a Land Speed Record Car are that "the motive power and steering system… are constantly and entirely controlled by a driver on board the vehicle".
For Bloodhound, that means I've got to control the EJ200 jet engine (dry and reheat power ranges), the rocket motor (two stages, light-up and high power) and the Formula 1 engine that powers the rocket pump.
While I'm doing all of that, I need to keep the car straight, as fast cars (in my world that means supersonic!) tend to drift across the track at high speed - have a look at "How hard can it be to drive in a straight line?, external"
This month's test driver was the Chancellor, George Osborne.
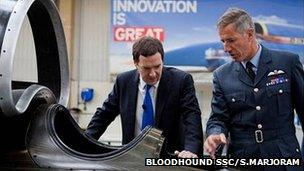
Showing the Chancellor the 1,000mph office
After a quick brief, he jumped into the Driving Experience and set our new fastest time - 1,007mph.
If you want to try to beat his time, then come along to one of our Bloodhound public events, external, or join our 1K Supporters Club, external, and give it a go.
The visit also gave us a chance to say thank you for the government's support to our Education Programme.
With around 5,500 schools now signed up (that's about two million students), keeping up with the demand for education materials in schools is a big task.
During the visit, we also showed the Chancellor how over 200 British companies are helping to develop and build the cutting-edge technology that will allow us to reach over 1,000mph - and do it safely.
Bloodhound SSC is being assembled from around 3,500 unique components.
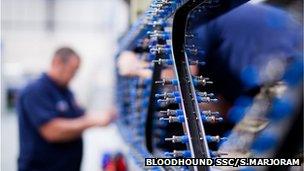
4,000 rivets done, 15,000 to go
The finished car is a blend of race car, jet fighter and spaceship technology, and every one of those 3,500 unique parts needs to be made perfectly, first time.
The quality of the work is simply world-class - if anyone tries to tell you that British industry is not a world leader any more, then send them to see us, external and we'll show them how wrong they are!
The car is looking more complete every time I see it.
The rear chassis assembly continues to grow from the floor up, with the chassis rails now being built up, before we start on the upper-structure.
This is a simply massive task, involving the bonding (that's gluing for engineers) and riveting of the aluminium, steel and titanium body panels.
The lower-chassis took 4,000 rivets to complete, with another 15,000 to go before we've finished the upper-structure.
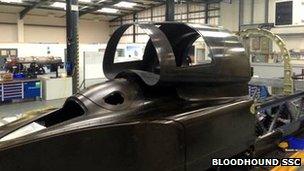
Bigger every week
Have a look at the video of the assembly, external - it's fascinating. We get everyone to help out, even the Chancellor, who added a couple of rivets during his visit.
URT is still doing a terrific job of delivering our composite parts.
After the mammoth task of making the carbon fibre monocoque (my 1,000mph office and one of the strongest, safest cells - perhaps the strongest ever? - in the history of motor racing), they are now churning out the intake sections.
As far as I can tell, making composite components is a cross between knitting and cooking.
The structural strength of the carbon fibre is critically dependent on how the individual carbon fibres are woven together, and then how the woven layers are laid up on top of each other.
The individual carbon fibres are only 5-10 microns (millionths of a metre) thick, about one 10th the thickness of a human hair, so we need a lot of them knitted together to build a 1,000 mph Car.
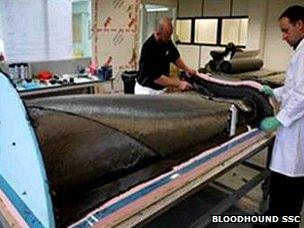
Resin infusion - the 30-minute meal
Once the fibres are knitted in the right direction to make the composite part strong enough, they need gluing together.
This is where the cooking skill comes in, with resin added either to the carbon fibre cloth before assembly (known as "pre-preg") or afterwards by a process called "resin infusion".
The whole thing is then cooked in an autoclave (a big engineering oven) until done.
The monocoque was made using carbon fibre moulds and "pre-preg" carbon sheets, as the recent Cisco BHTV episode, external explained very well. The disadvantage with this method is that half the work goes into making the moulds, so it takes twice as long.
For the intake components, we're using the simpler method of resin infusion, the carbon fibre equivalent of the 30-minute meal.
The dry carbon fibre cloth is laid up directly on to the former (no mould required) and then encased in a big plastic bag.
After all the air is sucked out, hot liquid resin (i.e. the glue) is added, which flows through the carbon fibre.
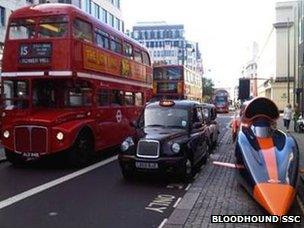
We’ll lift the lot
Once it's all soaked in, the whole thing is cooked in the autoclave.
Just like cooking, the results are all about how you put the ingredients together, and at URT we've got some world-class chefs on the case.
Our rear-suspension strut is now back from the test rig.
After several load cycles, it was tested to its working limit, by simulating a bump on the track (not that there are any, as far as we know).
The bump load was 153kN, or just over 15 tonnes, which it took with no trouble at all.
That's the same weight as a London double-decker bus, with 50 passengers on board, being lifted up by a single Bloodhound suspension rod.
That's impressive engineering.
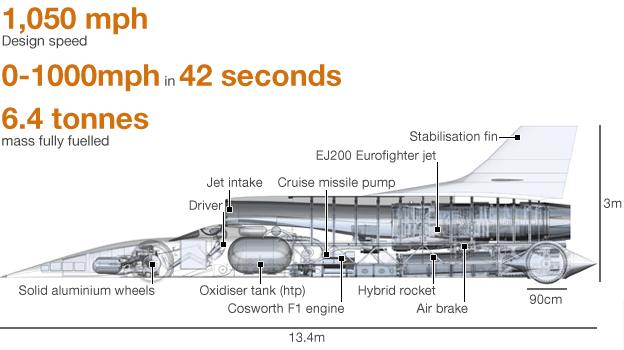
Image: Bloodhound SSC
- Published3 September 2013
- Published8 August 2013
- Published4 July 2013
- Published13 May 2013
- Published3 October 2012
- Published7 February 2011
- Published5 March 2011
- Published13 November 2010