Bloodhound Diary: Holes and rivets
- Published
A British team is developing a car that will be capable of reaching 1,000mph (1,610km/h). Powered by a rocket bolted to a Eurofighter-Typhoon jet engine, the vehicle will mount an assault on the world land speed record. Bloodhound will be run on Hakskeen Pan in Northern Cape, South Africa, in 2015 and 2016.
Wing Commander Andy Green, the current world land-speed record holder, is writing a diary for BBC News about his experiences working on the Bloodhound project and the team's efforts to inspire national interest in science and engineering.
The New Year started with some great news. Ron Ayers, the aerodynamic genius, external behind Thrust SSC (current World Land Speed Record, 763mph), the JCB Dieselmax (fastest diesel car ever, 350mph) and Bloodhound SSC (soon to be the world's first 1,000mph car) was made an MBE.
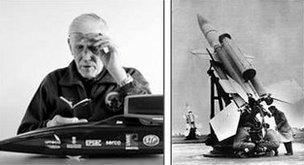
Bloodhound genius Ron Ayers was made an MBE
Ron is the reason for the "Bloodhound" name. He worked on the Bloodhound surface-to-air missile many years ago, producing huge improvements in its performance.
When we started to design a new Land Speed Record car, aiming for the amazing speed of 1,000mph, we used "Bloodhound" as a code name while we developed the idea in secret.
Come the 2008 public launch of the project, the name had pretty much taken root, so the car officially became the Bloodhound SuperSonic Car. We're very lucky to have a team of brilliant and successful engineers working on Bloodhound, and it's great to see one of them formally recognised.
Bloodhound starts 2014 with a new rocket partner. We've been working with Falcon for over five years now, to complete the initial research for our hybrid rocket technology.
The highlight of this work was the test firing of our full-size hybrid rocket at the end of 2012, external, watched live online by around quarter of a million people.
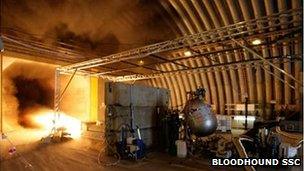
It really is rocket science
However, there is a lot of work required to turn this prototype into a full-tested production version, and it's a complicated process - quite literally, it is rocket science.
Step forward Norwegian company Nammo, external, which (luckily for us) is already working on a production version of a similar hybrid rocket, for a next-generation satellite launcher. A supplier to the European Space Agency, Nammo has agreed to manufacture the hybrid rockets that will boost Bloodhound SSC up to 1,000mph.
Bloodhound's hybrid rockets use a solid rubber compound as the fuel.
It's not explosive and will only burn under very specific conditions. Since I have to strap myself to several hundred kilogrammes of this stuff, this is quite reassuring.
The hybrid rocket combustion occurs when the rocket tube is force-fed with very hot oxygen. This is produced from concentrated hydrogen peroxide, also known as "high test peroxide" or HTP for short.
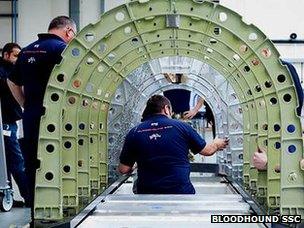
Only 11,999 more rivets to go
The HTP is forced though multiple layers of silver oxide mesh in a catalyst pack, at around 70 Bar (1000 pounds per sq in) and at a huge flow rate, around 40 litres per second. For comparison, that flow rate would fill your bath at home in three seconds.
The HTP (chemically, H2O2) is broken down by the catalyst action of the silver into water (H2O) and oxygen (O2). This process releases a lot of energy, so the mixture comes out at around 600C.
At this temperature the rubber ignites and burns furiously, heating up to over 2,500C, about twice the temperature inside an active volcano.
This increases the pressure inside the rocket tube, forcing the burnt gases out through the nozzle at high supersonic speeds. The reaction produces the rocket thrust, which for Bloodhound needs to be about 12 tonnes. It's going to be quite a ride.
The upper-rear chassis is now being drilled off for riveting, with 12,000 rivets in total. Most of the frames in the upper-chassis are aluminium, but Frame 1 (at the very back) is being manufactured by URT from high-temperature carbon composites.
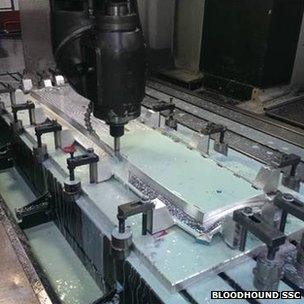
Turning a Fiat 500 into a bicycle
This will be able to cope with temperatures as high as 330C for short durations, and up to 250C all day long. Using carbon at the back of the car is a little counter-intuitive, as this is the hot bit, and composites don't like high temperatures. However, Frame 1 doesn't carry much load, and is a complex shape, so it's much easier to make in carbon. We'll also add a protective thermal coating and monitor the temperatures every time we run, just in case.
The upper-chassis has to cope with some huge loads. In addition to nine tonnes of thrust from the EJ200 jet engine, it has to support Bloodhound's huge fin at 1,000mph. Bloodhound will be travelling faster at ground level than any aircraft has ever been, so this is going to be the hardest-working fin in history (have you put your name on the fin yet?, external). The fin bolts on to a "shear plate", a truly extreme engineering component, even by Bloodhound standards.
The plate is over two meters long by 400mm wide, but in some places is only 2mm thick. It's the key part that interfaces the fin to the top of the upper-chassis.
Just to make the manufacturing task slightly harder, the shear plate has to be curved to follow the line along the rear of the chassis. Because the part is a complicated shape with lots of features on it, our friends at Manufax must start with 750kg of material to produce a final part weighing just 8.7 kg. In other words, they will turn a lump of metal weighing nearly as much as a Fiat 500 into a component weighing something akin to a racing bicycle.
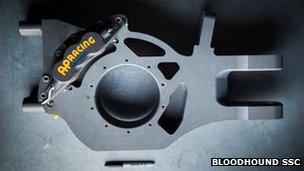
Strong but skinny front suspension
That's extreme one-off engineering. The metal that's machined away - known as swarf - is captured, recycled and used in other applications and products.
Perhaps surprisingly, the shear plate is going to be quite a delicate part until it's joined to the upper-chassis structure, when it becomes part of a very strong complete assembly.
The front uprights, which attach the front wheels to the suspension, have now been delivered by AP Racing. Manufactured from solid aluminium, they have been anodised to protect them from the desert dust (which will get everywhere and is mildly corrosive). Each upright weighs a staggering 21.5kg and, between the two of them, are designed to take peak suspension loads of up to 30 tonnes.
For comparison, an upright from a "normal" race car would weigh around 1kg and would fit in the hole in the centre of the Bloodhound upright.
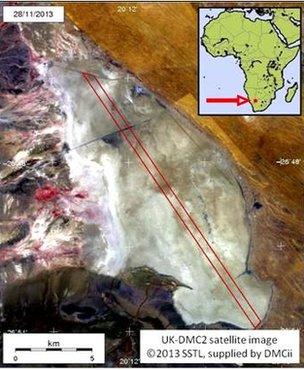
DMC – Watching it rain 5,000 miles away
Bloodhound will use conventional wheel brakes for UK runway testing and at low speeds (less than 200mph) in the desert. Each front brake caliper is half-built into the front uprights.
This arrangement is unique to Bloodhound, allowing the engineers to package the front wheels and suspension into the smallest possible space. It keeps Bloodhound's front track (the distance between the front wheels) narrow, making the front of the car narrower and more aerodynamic.
It's the rainy season in South Africa's Northern Cape right now. Thanks to DMC International Imaging and Surrey Satellites, we can keep a close track of how the surface floods and dries.
The dark areas on the satellite photo show the damp/wet areas. We can even see the remains of the old causeway, as a dark line across the track near the northern end. This is a good sign as it means that the surface repairs are now being "glued" together by the rains.
The Northern Cape has been working on the world's fastest race track for three years now and it's almost complete. I can't wait to get out there in the next few months to see the end result.
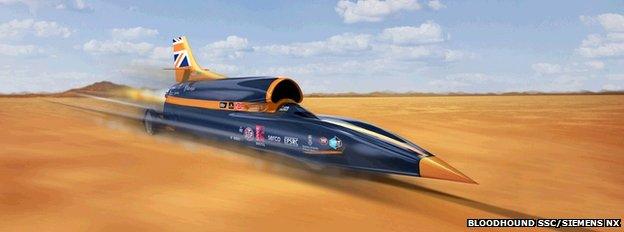
The Bloodhound car will run on a specially prepared dried-out lake bed in South Africa
- Published25 December 2013
- Published19 December 2013
- Published4 July 2013
- Published13 May 2013
- Published3 October 2012
- Published7 February 2011
- Published5 March 2011
- Published13 November 2010