London 2012: Will the Olympic torch survive a British summer?
- Published
Olympic torch tested on top of Mount Snowdon
After stringent tests, the Olympic torch has emerged with its flame alight and been pronounced "weather proof" by Olympic organisers Locog.
But what exactly was the torch subjected to, given it has to survive our often soggy summers, not to mention <link> <caption>being whizzed on a zip-wire</caption> <url href="http://www.bbc.co.uk/news/uk-england-tyne-15528021" platform="highweb"/> </link> , <link> <caption>slogging up Snowdon</caption> <url href="http://www.bbc.co.uk/news/uk-wales-15563973" platform="highweb"/> </link> and braving white-water rapids?
Basildon-based Tecosim Technical Simulation were tasked with exploring how the torch would react to extreme weather, and they worked alongside Bullfinch, whose engineers developed the burner system.
Our burning questions about the torch were answered by Tecosim's MD Stuart Hawker and its lead engineers Gary Lansdowne and Ian Raper, plus Bullfinch's lead engineer Nigel Williams and Locog's Clare Pelly, who was project manager for torch production.
How did the testing process start?
<bold>Clare Pelly</bold>: We started in 2010 by looking at what the torch needed to be, and how it needed to behave.
It had to be strong, robust and safe on the roads - health and safety were key.
What conditions did the torch need to be able to withstand?
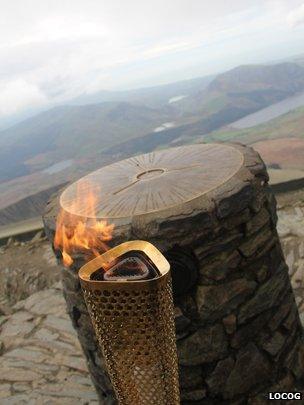
The torch has been exposed to extremes of altitude, wet and wind
<bold>Stuart Hawker</bold>: Locog stated that the torch had to work within temperatures of -5C to 40C, as well as in 95% humidity, rain and snow, in wind speeds of 35mph, gusting up to 50mph and an altitude of 400 feet above sea level.
The orientation of the torch was also key - it had to stay alight when tilted at 90 degrees and 45 degrees either way.
We also had to do a drop test, dropping it vertically onto the burner and also onto the base, after computer simulation determined these were the worst-case scenarios. There was some discussion about what height it might be dropped from onto a hard surface, perhaps from horseback or an elevated stage - we settled on three metres.
We needed to be sure the burner would remain inside the body of the torch, that it would be safe. Obviously after such a drop the torch would have to be replaced, but the main thing was that no-one would be hurt by the burner.
We also did a durability test which wasn't a prerequisite from Locog, but we wanted to ensure the torch could be robust enough so it wouldn't be easily damaged while being taken on and off the bus, in case it hit anything.
What was the most extreme testing you carried out?
<bold>Stuart Hawker</bold>: We did the majority of the testing over three days in BMW's wind tunnel in Munich. We replicated extremes of a multitude of weather conditions.
It was better to do things logically in terms of starting at -5C. Gas finds it difficult to convert from liquid to vapour at that temperature. We did a snow simulation and put the torch through orientations you'd expect during normal use.
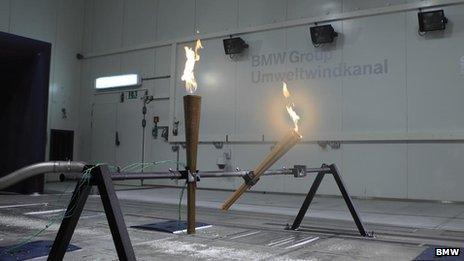
Testing the torch in BMW's Munich wind tunnel
We then took the temperature up to 5C, adding rain, various orientations, conditions and wind speeds. Next was 20C, which is more typical of a nice summer's day in July and August.
We did go up to 40C which doesn't give the gas system much of a problem. It works best at high temperatures, but then you're looking more into the heat management side of things where you don't want it to get too hot. Cool down is the slowest at this temperature.
I should add that we did do some testing before Munich, simply by using an industrial fan. Hiring a wind tunnel is very expensive and it's heavily utilised so it's really hard to book time there. So the torch was tested with the fan in a cold chamber, where a lot of development work was done. Bullfinch had also done a lot of testing of the burner pre-Munich.
Which bit of the testing proved the most tricky?
<bold>Gary Lansdowne</bold>: The most difficult testing was at -5C at high wind speed. The torch is lightweight with many holes and the structure doesn't provide much protection for the burner, so wind chill on the burner canister was key. It has no protection from driving snow or rain. The burner was totally exposed as it has to breathe. But it still worked in those conditions. We did have some highs and lows during the testing, but mainly highs.
How many torches did you test?
<bold>Gary Lansdowne</bold>: We had three torches - two were ours, prototypes of the ones designed for the 2012 relay - and one was a "benchmark torch". It was from the 2006 Turin Winter Olympics as this torch was considered to be the best previous one with the least number of flame-outs.
We put both types of torch through all the tests, to compare the relative performance of the two. Our torch proved to be extremely robust.
How did you determine the size and duration of the flame?
<bold>Nigel Williams</bold>: The flame had to be big enough to be seen by the audience in the stadium and robust enough so it couldn't be blown out. Its size was purely determined by the size of the torch.
It's 400mm high, from the bottom of the burner to the top of the flame.
It needs to burn for a minimum of 10 minutes, but with the gas cylinder and burner we've got now, it will last 13 to 14 minutes.
<bold>Clare Pelly</bold>: The average distance each torchbearer will travel with the torch is 300m and each leg of the relay is expected to take between three and six minutes. We've allocated one cylinder per torchbearer.
How about safety for torchbearers as regards the flame?
<bold>Clare Pelly</bold>: We were concerned with the safety aspect of the torch throughout the whole testing process. Torchbearers will not handle the burner.
We are issuing a torch safety document for the Metropolitan Police, who as part of the torch operations team will turn off the gas on each torch when it has been used. The torch then has to cool for 10 minutes before being handled. Safety is paramount - our youngest torchbearers are aged 12.
How does the burner work?
<bold>Nigel Williams</bold>: It was based around a burner we designed in 2010 when we were asked to produce <link> <caption>burners for beacons for Hadrian's Wall celebrations</caption> <url href="http://www.guardian.co.uk/culture/interactive/2010/mar/12/hadrians-wall-lights-500-torches html" platform="highweb"/> </link> , which involved 500 beacons being lit along the 84-mile national trail that follows the line of the wall.
The Olympic torch system was a miniaturised version of that one although we adapted it slightly after environmental tests.
It works like a miniature hot air balloon really, which overcomes all the problems caused by cold temperatures. It uses a vapour off-take system, which uses a cylinder full of liquid gas. The top of the liquid is heated by a coil in the top of the burner which is heated by the flame, turning the boiling liquid into a gas. The canister is filled with two-thirds propane and one-third butane.
Did the torch have to be modified during the tests?
<bold>Gary Lansdowne</bold>: Yes. We had to introduce a small perforated cup shield to surround the burner. It gives better wind protection, a better gas reservoir and it's easier to light. Bullfinch worked on it. Each Olympic torch design is so specific, so you end up having to design a burner to fit the torch - it's definitely not one design fits all.
<bold>Ian Raper</bold>: When you examine the other Olympic torches, you can see why they've gone down certain routes with the burner. Our torch is unique, so we have a burner system that works exclusively for it.
<bold>Stuart Hawker</bold>: The styling of the holes of the torch [it has 8,000 laser-cut holes representing the 8,000 torches and torchbearers] gave us numerous challenges. It's beautiful but everything's on show. The torch needed to hold together with the burner under high drop loads and we had to hide the fixings and not spoil the design - everything's hidden away.
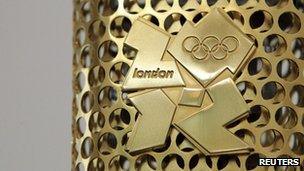
The torch's 8,000 holes were a challenge for the burner
We also had to play with hole pattern so the fixings holding the burner could be attached to the skin of the body without tearing the panels.
We had to go back to the designers [Edward Barber and Jay Osgerby] to ask about moving the holes slightly. We were able to do a lot of computer analysis so we didn't need to physically have lots of models.
We fed it all back to the design company for their input and they had a very pragmatic approach. They didn't want to compromise their beautiful style but it also has to function and has to be safe. We proved why things needed to change.
So they took a view that mild styling changes wouldn't be apparent but were needed. It took several weeks of work to iterate the pattern and size of holes, but after that we got our prototype.
British summers are not known for being particularly dry - what if it rains?
<bold>Nigel Williams</bold>: The torch can survive rain as long as it's not bucketfuls of water - rain simply evaporates off. Obviously if the torch was dropped into water off the side of a boat it would go out but we'll have spares.
What happens if the torch goes out?
<bold>Clare Pelly</bold>: We always have the mother flame in a back-up lantern. We're able to use the lantern to relight a new torch in extreme situations and we'll always have additional torches within 30 seconds' reach.
Where else has the torch been tested, and what happens if sand is blown in the burner?
<bold>Gary Lansdowne</bold>: One thing that did shine out loudly during the wind tunnel tests was that they represent the worst-case scenario. In the real world, you don't get constant wind speed - a wind tunnel is worse than reality. So we were keen to do as much reality testing as possible.
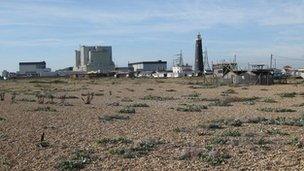
Windy Dungeness beach was also a testing spot for the torch
We took the torches to beaches near the EDF nuclear power site in Dungeness, Kent, which has 20-39 mph winds.
EDF are supplying the fuel for the torches. It's a pebbly beach and you can't measure the exact amount of dust and grit in the air, but there were lots of areas that were dusty and dry.
We also took the torch up Snowdon in Wales with 50mph winds and there were no issues at all. I don't believe the torch will go out in high winds.
What about lightning?
<bold>Clare Pelly</bold>: If there was an electric storm we'd probably stop the relay. The safety of the torchbearer will always come first.
Is it true that you looked at making the torch energy efficient by powering it with elephant grass, but that it wasn't possible to do in time for 2012?
<bold>Gary Lansdowne</bold>: Yes. An energy efficiency solution using [biofuel] elephant grass was looked at for the torches. But the problem was the timescale required to develop the fuel. The torches are so high-profile and there are such high numbers of them that there just wasn't time. But it was useful to do the work on it, and the research will have other uses.
Is there any testing still to do?
<bold>Clare Pelly</bold>: We need to test it being carried by someone on a zip wire - initial tests have gone very well. We're just making sure for safety reasons.