The Gasless Green House
- Published
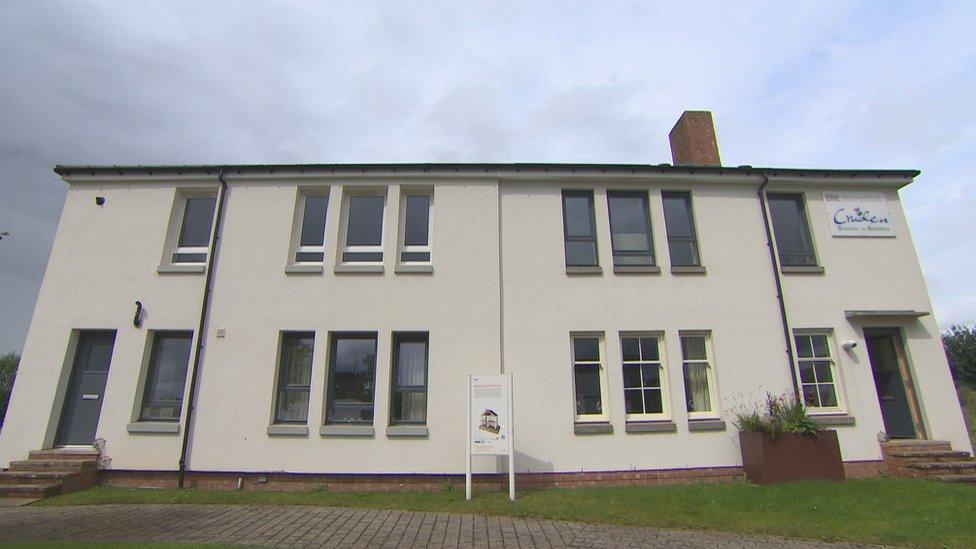
A block of four flats - similar to those built across Scotland in the 1930s - has been built at the former Ravenscraig steel works
Building low carbon homes is proving tougher than expected, when the Scottish government set out ambitious targets in 2007.
House builders continue to face little pressure from customers, and there is at least some push back at the ratcheting effect of building standards.
A far bigger challenge is in retro-fitting older homes, with the gulf between maximum and minimal approaches roughly three-fold.
There's a small part of the former Ravenscraig steel works, where the past has been recreated - not a blast furnace, but a block of four flats, of the type built across central Scotland in the 1930s to replace slums. It now numbers around 250,000 housing units.
They were built for the times, and they've been adapted for the expectation of central heating and double glazing. The coal storage has gone.
The design was re-built, to a 1930s spec, on the BRE building research site in Lanarkshire, requiring South Lanarkshire Council planning approval to break the current construction rules.
It was then upgraded to take account of typical improvements since the inter-war years.
And each of the four flats has subsequently had an upgrade, to differing specifications, to see how different approaches perform in terms of energy efficiency.
The more minimal makeover involves external insulation cladding and new windows. The most extensive one includes solar panels on the roof and an air source pump.
The walls were stripped back to the brick, and new internal insulation panels were installed. This level of household surgery requires that occupants move out. It can get messy.
The end result reduces the floor space, but is the most effective way of improving energy efficiency when you retrofit a home. And those who have had it done to their homes like the broader internal window sill.
It's not clear how much each would cost, if an attempt were to upgrade the flats by the thousand. An entire industry could be built around this, building in efficiencies and providing opportunities for exporting expertise.
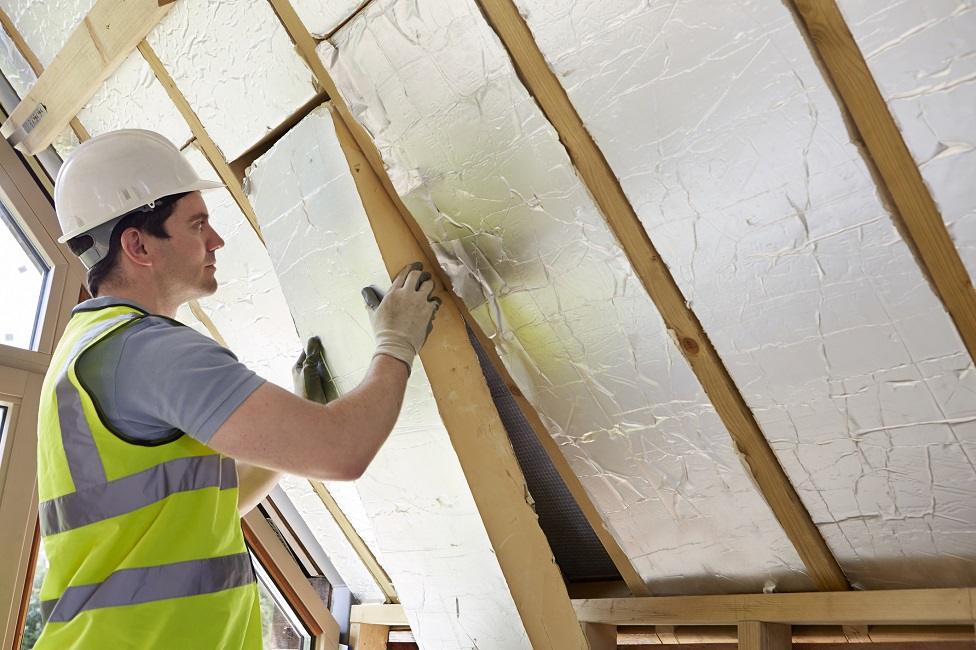
David Kelly, the housing specialist who is a director of BRE - the building research establishment that the UK Government hived off - reckons that between the least and the most extensive makeover, there's a cost difference of roughly three-fold.
I've been learning a lot about housing recently, in trying to find out what might be required if Scotland is to hit government targets for getting greenhouse gas emissions to net zero, within 30 years. That's the UK target. The Scottish government is being more ambitious, to get there by 2045.
If that seems a long time, bear in mind that homes being built now will only be half way through their design lifespans by then.
This was explained by Tom Barbour, of Thermal Image UK, wielding a heat-seeking camera with which to expose shoddy building finish. He reckoned that could add a tonne of carbon dioxide to the new-build Carfin home we were visiting, on top of three to four tonnes in its design. Without being sorted, that adds up throughout its lifespan. Without reducing those emissions now, they're locked in for the 60 year design lifespan of a building.
There's a lot of capacity for improved efficiency on new-build. When the house building industry and government both proudly cite the 70% improvement in energy efficiency for new homes built now, when compared with new build in 1990 - the baseline year for climate change measures - it sounds impressive.
But it can also have you wondering: how bad were they back then? Why weren't they better? Heating bills were a factor back then too, weren't they? And how much better could building standards be within 30 years, leaving today's new-builds in their shade?
'Gradual ratchet effect'
What, then, would it take for the house builders to build their homes according to the long term cost to the owner, rather than the short-term profit that the volume house builders pursue in the interests of their shareholders.
There isn't much of an incentive for them to build for minimum long term cost, or for the highest level of efficiency.
When pushed on building standards, the concern of the house builders is to meet government wishes to increase housing completions. There's a trade off there: the higher the spec, and the higher the cost of building energy efficient buildings, the lower the completions.
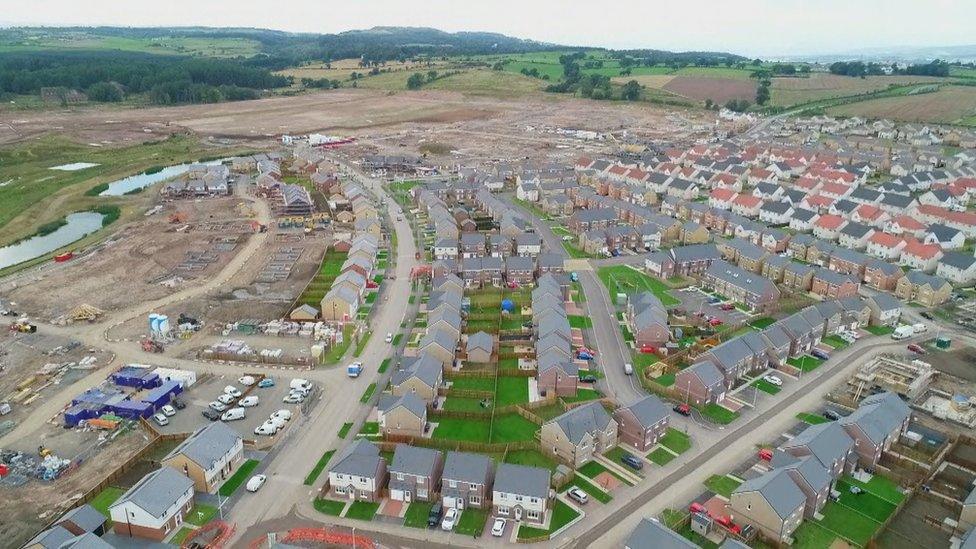
With that downturn thinking, and with a clear-out of many construction firms in the past 10 years, there's been a slowing up of the gradual ratchet effect on building standards during the past decade.
The last upgrade was delayed until 2015. Although there's a climate emergency declared, we won't know until 2021 whether future housing developments are to be off the gas grid (as they are, from 2025, in England).
There are European directives also on the extent of electric vehicle charging points with new developments. In or out of the EU, we won't know how that will be applied in Scotland for another two years.
Location is king
The new build market is strongly controlled by those volume house builders. Customers get to choose kitchens and bathrooms, but otherwise get and buy what they're offered.
It's a rare house builder who finds themselves struggling to sell stock, even in these uncertain economic times.
The lack of customer engagement in the issue was acknowledged by Lynne Sullivan, who convened the panel advising the Scottish government on building standards in 2007, and reconvening in 2013, concluding:
"Surveyors, and ultimately lenders, do not factor in the additional value of low-energy buildings in relation to running cost savings, reducing the potential for a developer to recoup their additional capital investment.
"We offered suggestions as to why this may be:
People expect a new building to be energy efficient. It is a 'given' so it is difficult to promote.
Location is still 'king' both for new homes and commercial buildings.
Education is lacking on carbon emissions. There is a need to make this more of a 'currency' in the eyes of the public, and give clarity to the twin objectives of energy efficiency and low carbon in buildings.
Some newer technologies available to industry are often not viewed with confidence by prospective owners, warranty providers, insurers or lenders.
Lack of fiscal incentives and awareness, by building owners and occupiers, of benefits in return."
Commercial buildings can gain in value if they have a high energy rating. Using commonly understood efficiency ratings, the car industry is being driven by fuel efficiency. But rarely residential homes.
So David Kelly is one of those to point to consumer information as a key component in improving the housing stock.
Every house sale has to include an energy rating already, but how many sales are decided by the information within it? And what would it take for that to become a decisive factor, potentially upending the housing market by giving real power to the buyer?
Armed with information and an understanding of energy ratings, they could trade off up-front price with the long-term cost of running and heating a house. And that only works if the secondary market - that is, buying a second hand home - has similarly informed customers.
Breathing stone
Homes for Scotland, the industry grouping, is eager to get a more diversified industry, to bring on small and medium-scale enterprises (SMEs).
Understandably, it would also like us to focus more attention on the existing housing stock.
As the owner of an 1860s terrace house - a familiar age for much of Scotland - I can see the problem. Its stonework is constructed to breathe, which means the loss of heat. When I recently sought to move on from an inefficient gas-fuelled heating boiler, there was no question of me getting anything else but a more efficient gas-burner. The electric system that ought to become the affordable norm within 10 to 20 years is not yet in our reach.
But to retrofit such a house for low energy use is far from easy, as I learned from John Riley, in Biggar. He's the owner of a splendid villa, built from stone in 1900.
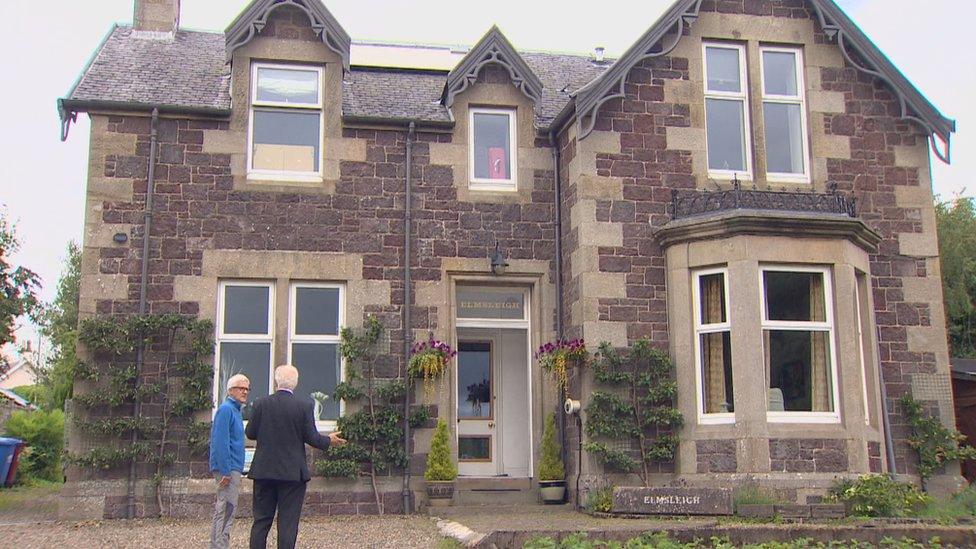
Mr Riley clad his house from the inside
He is something of a dogged pioneer in the venture of understanding what it takes to tackle the backlog of inefficient older homes.
The answer is not simply to copy Scandinavian standards, where heavy snow and biting cold is the wintry norm, and where they face fewer challenges than Scots from wind and rain.
Unable to clad his home from the outside, Mr Riley clad it from the inside. There was no brick cavity to be filled. He had to strip back all the plaster on external walls, to replace them with a thick shell of insulated panels. As he put it to me, it was as if he had built a modern house inside the old one.
The cost? Along with a heat exchanger in the attic (using warm stale air to take the chill off the fresh air intake) and solar panels, the bill was roughly £25,000.
But that only bought the materials. It didn't buy his time, or the cost of cleaning up the soot and filth from 120 years of Biggar life and coal-burning. Nor did it include the cost of decanting the Riley household out of the building for a year of stressful DIY.
So to take this to net zero - reducing the need for conventional heating with heat exchanging technology, solar panels, and air or ground-source heat pumps - is expensive. There is a limited range of hardware so far available to the committed householder.
The sealing of buildings brings problems of internal air quality, which have yet to be reliably resolved.
But a bit like education, so it is with climate change: if you think that sounds expensive, just try the alternative.
- Published19 August 2019