Human urine bricks invented by South African students
- Published
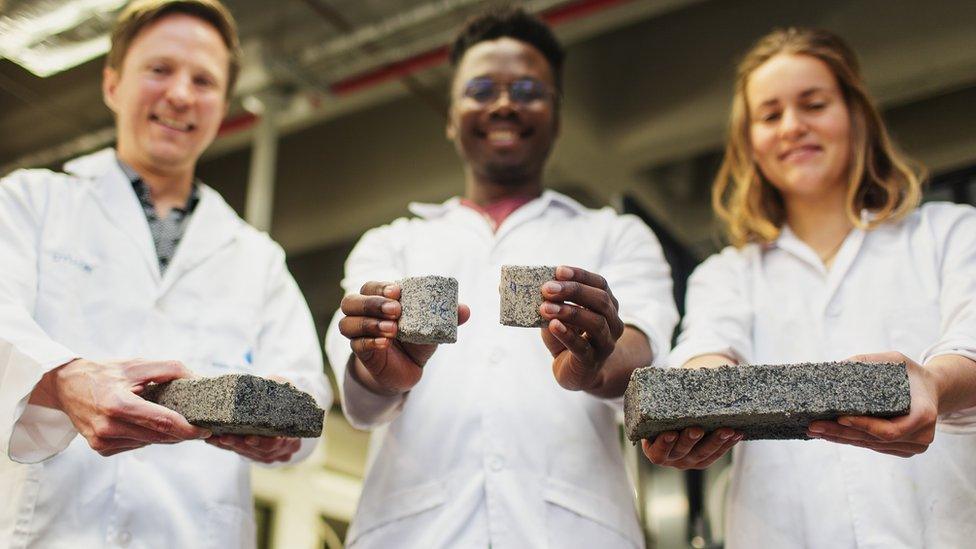
The bricks initially smell of ammonia but the odour disappears after about 48 hours
Human urine has been used to create environmentally friendly bricks by university students in South Africa.
They combined urine with sand and bacteria in a process that allows the bricks to solidify at room temperature.
"It's essentially the same way that coral is made in the ocean," Dyllon Randall, their supervisor at the University of Cape Town, told the BBC.
Normal bricks need to be baked in high-temperature kilns that produce large amounts of carbon dioxide.
'As hard as limestone'
The engineering students at the University of Cape Town (UCT) have been harvesting urine from men's toilets.
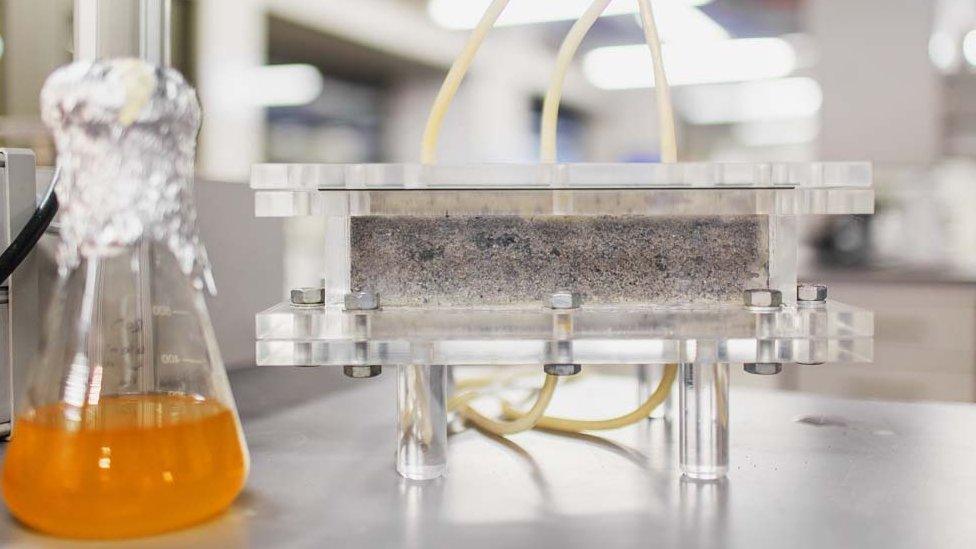
The bricks take between four and six days to grow depending on the strength needed
After first making a solid fertiliser, the leftover liquid is then used in a biological process "to grow" what the university calls "bio-bricks".
The process is called microbial carbonate precipitation.
The bacteria produces an enzyme that breaks down urea in the urine, forming calcium carbonate, which then binds the sand into rock hard, grey bricks.

How many loo breaks to make a brick?
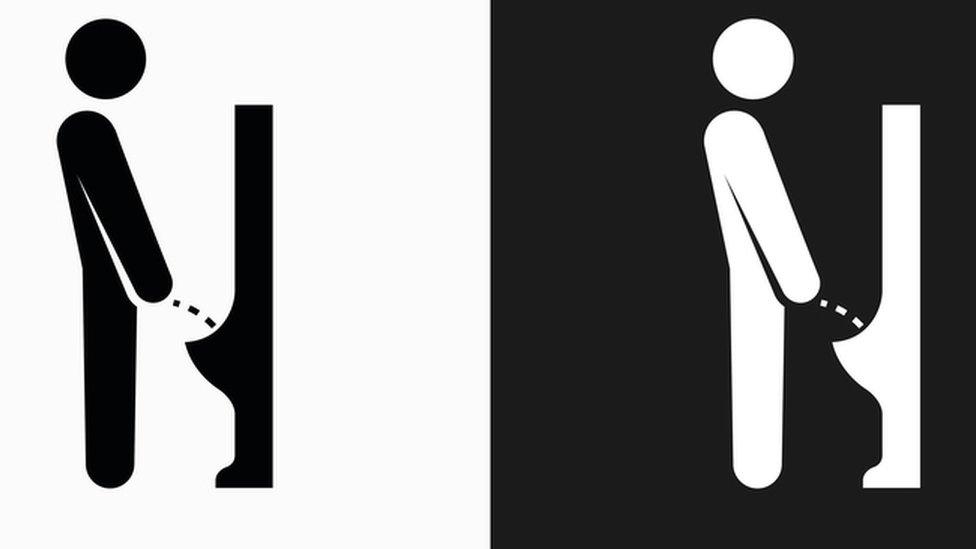
On average a person typically produces between 200ml and 300ml of urine per urination
A "bio-brick" needs between 25 litres and 30 litres to grow - this may sound a lot, but most of this urine is also used to produce about 1kg of fertiliser
So to make one urine brick, you'd need to go to the loo about 100 times.
(These are all rough calculations from the bio-brick and fertiliser urine project.)

The strength and shape of the bio-bricks can be altered as required.
"When we first started this process last year, we achieved the same compressibility strength as a 40% limestone brick," Dr Randall told the BBC Newsday programme.
"Just a few months later we've doubled that strength now just by changing the material we put into the mould and allowing the bacteria to cement the particles for longer - with zero heat, at room temperature."
Regular bricks are kiln-fired at temperatures around 1,400C (2,552F), according to the University of Cape Town.
But Dr Randall admits their process is much smellier.
"Say you had a pet and it peed in the corner, and you have that strong smell - that's ammonia being released. This process produces ammonia as a by-product," he said, adding that this ammonia is then converted into nitrogen-rich fertiliser.

You may also like:

But after about 48 hours, the bricks completely lose the ammonia smell - and they do not have any health risks either, he said.
"The process we use in stage one kills all harmful pathogens and bacteria because we operate at an extremely high pH that has been shown to kill pretty much everything."
According to UCT, the concept of using urea to grow bricks was tested in the US some years ago using synthetic urea, which requires a lot of energy to produce.
The bricks produced by Dr Randall and his students, Suzanne Lambert and Vukheta Mukhari, use real human urine for the first time, which offers opportunities for recycling waste.
They take between four and six days to grow - if you want a stronger brick you leave it for longer.
- Published9 November 2011
- Published31 July 2018
- Published24 July 2018
- Published18 September 2018