Greener planes of the future... or just pretty plans?
- Published
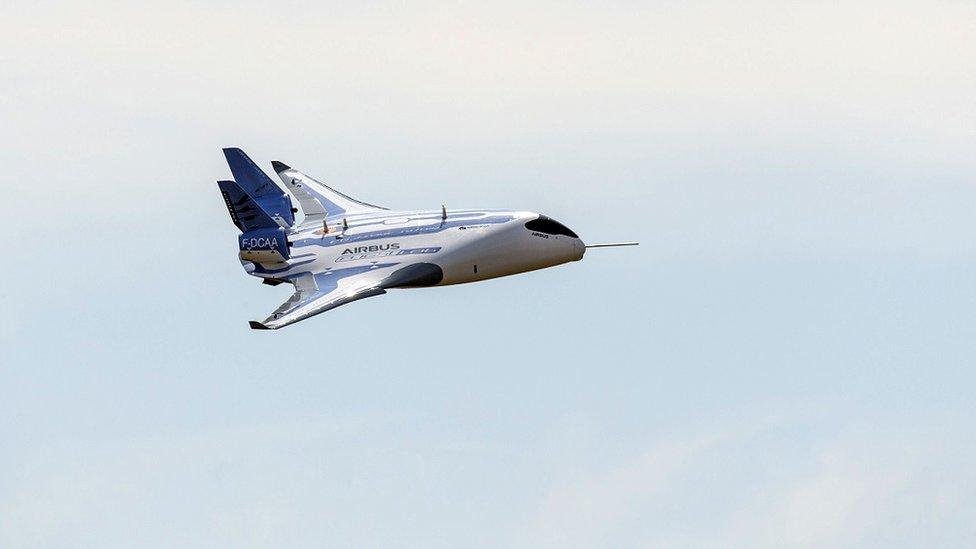
The Airbus Maveric is a remote-controlled blended-wing test aircraft
At an undisclosed location Airbus has spent months testing a radical looking plane. At 10ft (3m) wide, it is only small, but it could be the start of something very big in the aerospace industry.
It looks like a flying wedge - known in the trade as a blended-wing design.
Airbus calls the remote-controlled aircraft Maveric and is keen to emphasise that, at the moment, it is only exploring how the configuration works. But it says the design has "great potential".
One day it could be scaled up to the size of a regular passenger jet.
In traditional aircraft the fuselage is basically dead weight and needs big wings to keep it in the sky.
Under a blended-wing design, the whole airframe provides lift, so it can be lighter and smaller than current designs, but can potentially carry the same payload.
Maveric is one of several initiatives from Airbus, and there are many by other aerospace firms, to meet an industry target to halve emissions from air travel by 2050, compared to 2005 levels.
"There is a really big challenge there. And there is a big expectation from society which we think it is our duty to find answers to," says Sandra Bour-Schaeffer, the chief executive of Airbus UpNext, which evaluates new technologies for the European aerospace giant.
"We believe that we have to go into a really… breakthrough technology," she says.
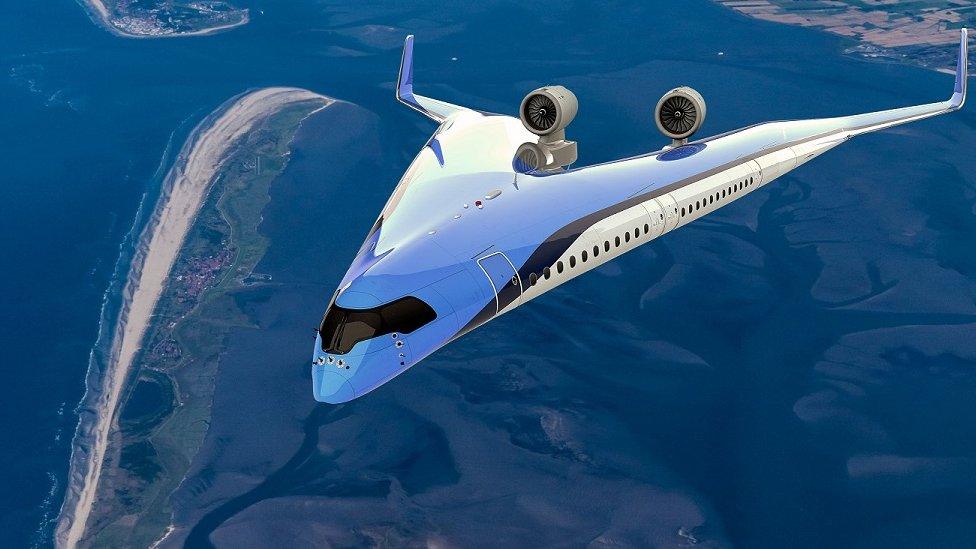
The Flying-V design would see passengers carried in the aircraft's wings
An equally radical idea is being explored at Delft University of Technology in the Netherlands.
Researchers there are working on a design known as the "Flying-V". It is a new concept for a long-haul aircraft, which they claim would be up to 20% more efficient than a state-of-the-art modern plane such as the Airbus A350.
Like Maveric, it abandons the idea of a conventional fuselage. But in this case the shape is more like an arrowhead, with two wings stretching out behind the cockpit in a V. Passengers and cargo would be carried within the wings themselves.
The designers think it would be cheaper to build than the blended wing because the two arms of the V could be "plugged" into the rest of the fuselage. So the aircraft could be built in parts, rather than all at once.
"We think we can keep the manufacturing costs relatively low, compared to concepts that would have more unique components," says Roelof Vos, the project lead for the Flying-V and an assistant professor at Delft University of Technology.
The design was originally the brainchild of a graduate student, and formed part of his thesis. It is being developed with support from the Dutch airline KLM and Airbus - and in July a scale model took to the skies for the first time, from an airbase in Germany.
The flight of the test aircraft - a battery-powered drone with a 9ft wingspan - was deemed a success.
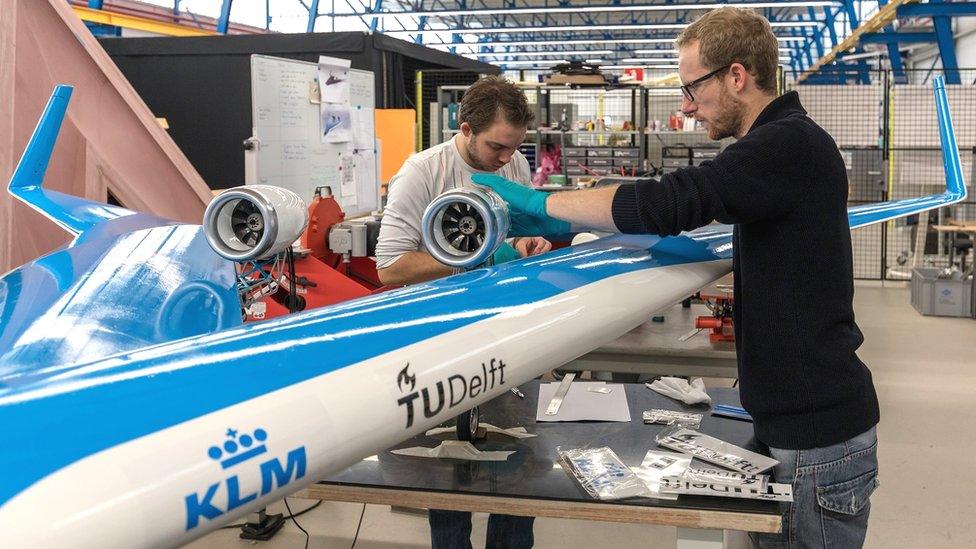
A flying scale model of the Flying-V being prepared for tests
Researchers said the machine performed well, although it did suffer from a kind of aerodynamic wobbling, known as "Dutch roll". This made it difficult to keep the wings level, and resulted in what they described as "a somewhat rough landing" that damaged the front landing gear.
Data from those tests is currently being analysed and incorporated into a flight test simulator.
Airlines have seen their sales slump due to the pandemic, but despite that KLM says it will continue to support research into the Flying-V.
The attractions of more efficient aircraft are obvious, for an industry where cost control is vital to profitability, and which is under intense pressure to reduce its environmental impact.
But with the basic layout of commercial aircraft having gone unchanged for decades, there are other practical issues to consider - some of which avionics expert Steve Wright of the University of the West of England describes as "showstoppers".


Among them are how passengers board or leave the aircraft. In the case of the blended wing, for example, the wide central section could make the boarding process take longer, while passengers in the middle would be a long way from the exits in an emergency.
There's also the question of passenger comfort. Those sitting close to the side of the aircraft - and effectively close to the edge of the "wing" - would experience much greater movement when the aircraft is banking, while take-off and landing would have to be at steeper angles than normal.
Building a new type of aircraft would also present a challenge to the aerospace industry. Airbus, for example, makes sections and components of existing aircraft all over Europe, before bringing them for final assembly in Hamburg and Toulouse. It is a tried and tested supply chain, using the specific expertise present in each region.
"That well-oiled manufacturing machine... it would certainly be strained and would have to be redesigned," says Mr Wright.
Airbus insists that issues such as these are already under consideration and would be considered as part of the design process - but there's little doubt a design such as the blended wing or Flying-V would represent a major gamble for a manufacturer.
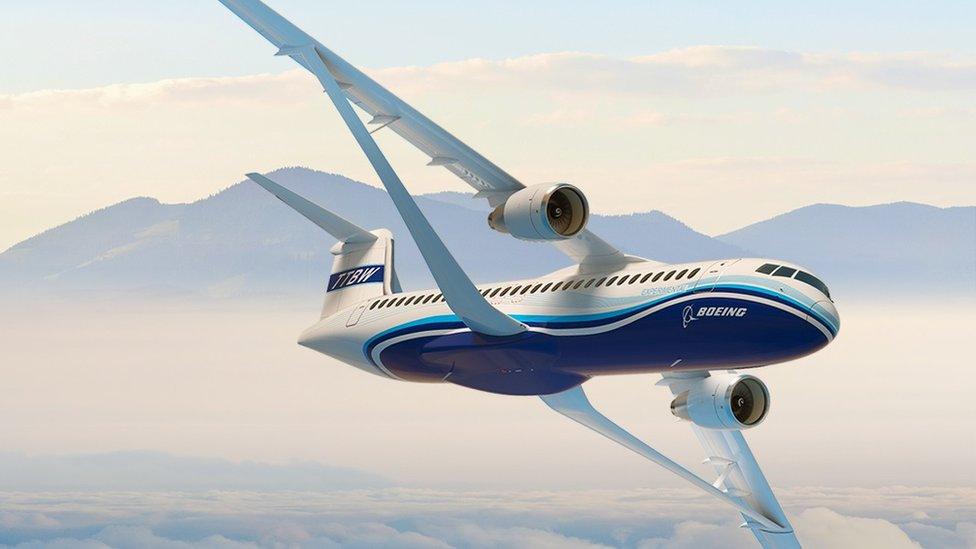
Boeing's Transonic Truss-Braced Wing design
Its rival Boeing has spent years studying a concept that is less obviously radical, but still a clear departure from what we have now: the Transonic Truss-Braced Wing.
Aircraft equipped with the wing would look relatively conventional, with a central fuselage. But the wing itself would be much longer and thinner, and would be braced by a support, or truss, angled up from beneath the fuselage. The wing would fold to make accessing conventional airport gates easier.
Boeing says the new design would need 9% less fuel than a conventional design.
But current research is not only focused on aerodynamics. There's also the question of how future aircraft are powered. For short-range flights, with a limited number of passengers, battery power might be viable. Projects such as the Eviation Alice - shown off at the 2019 Paris Airshow - are based on proving that concept.
For longer distances, batteries are currently impractical, because they are simply too heavy and do not contain enough energy to compensate for that weight. The industry has explored other options, such as hybridisation - in which part of the thrust needed to fly is provided by electric power.
One major research project was Airbus's E-Fan X, a partnership between Airbus, Rolls-Royce and Siemens. It involved fitting a single 2MW (2,700hp) electric motor, powered by an on-board generator, to a four-engined BAe 146 test plane.
But the experiment was cancelled last year - before the system could be tested in flight - as the effects of the Covid outbreak led Airbus to review its priorities.
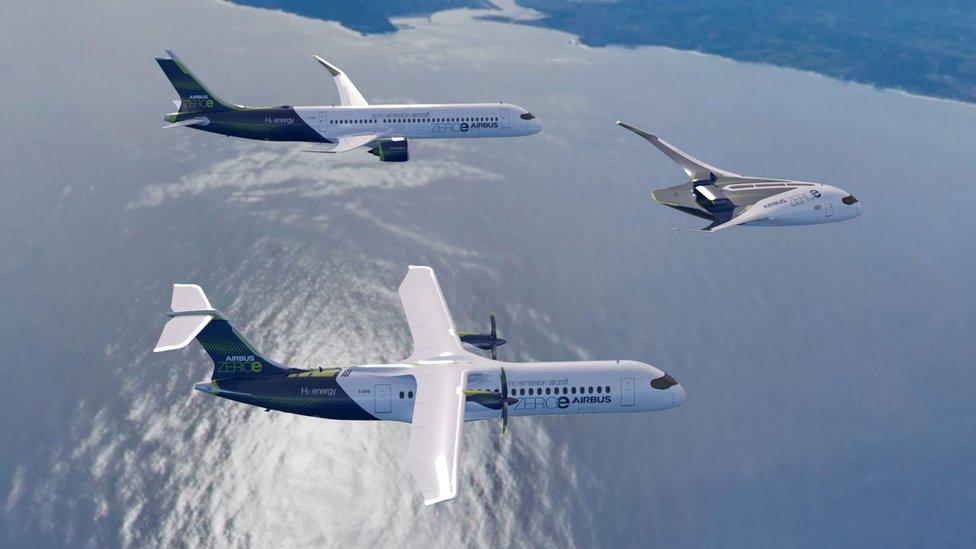
Airbus is exploring the use of hydrogen for fuel in its ZEROe project
Those priorities now include research into hydrogen propulsion.
Airbus has pledged to build the world's first zero-emission aircraft by 2035. Its plans rely on creating hybrid systems, using hydrogen-burning gas turbine engines as well as hydrogen fuel cells to generate electric power.
In September, Airbus unveiled three concept hydrogen-powered designs.
Hydrogen fuel could even be combined with a radical design - one of the concepts included the blended wing.
But there is a significant problem here. Most of our hydrogen supplies today are derived from methane - a fossil fuel - which is mixed with steam at high pressures. It is an energy-intensive process that creates significant quantities of carbon dioxide.
In order to be truly zero emission, aircraft would need to be powered by hydrogen produced in a much more environmentally friendly way - and large quantities would be needed. But according to Glenn Llewellyn, Airbus vice president for zero-emission aircraft, society itself will eventually provide the solution.
"Over the next decade, in order for society at large to meet the Paris Agreement, to meet our climate targets, we need to shift to renewable hydrogen," he explains.