Creating animal food from a greenhouse gas
- Published
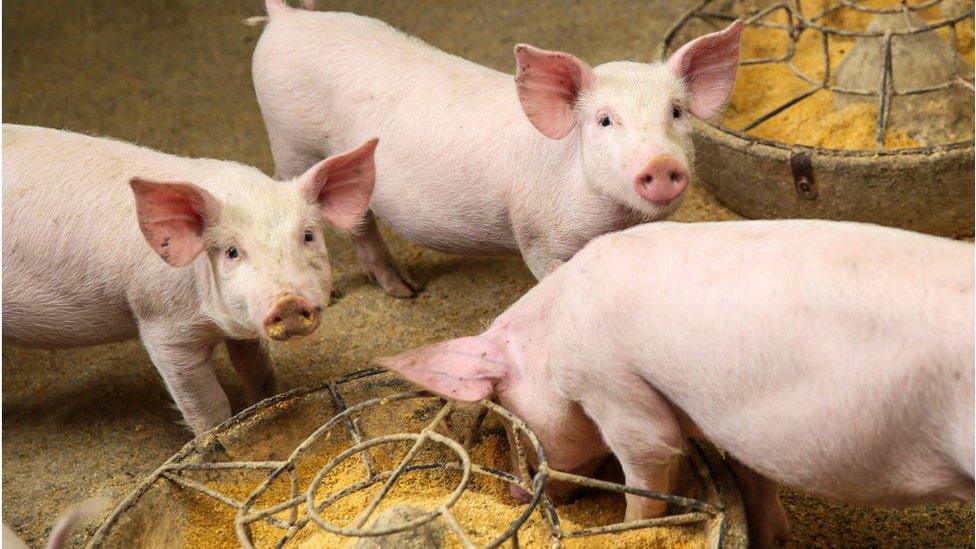
Global demand for meat is expected to rise in the coming decades
"I've tasted it, and it's great. If I had to put a flavour on it, I'd say it's slightly umami," says Peter Rowe, chief executive of biotech firm Deep Branch.
Mr Rowe clearly takes his work seriously, as he is not talking about food for humans. Instead, he has sampled an artificial protein that has been created to feed to animals.
Mr Rowe and his partners are trying to reduce the carbon footprint of animal feed which is often shipped around the world.
"If you take soy production, which is the primary protein source for feeding things like chickens, or if you take fishmeal production, which is the primary protein source for salmon, both of these tend to be done in South America," says Mr Rowe.
In the case of fishmeal, anchovies are caught off the Pacific coast of Peru and Chile, processed and shipped around the world. Similarly, soy plantations in Brazil or Argentina may involve clearing forest and require large quantities of fertiliser, heavy usage of agricultural machinery and, again, long-distance shipping.
"So a lot of the carbon intensity comes from the processes themselves, and a big part is the carbon intensity of shipping it over," says Mr Rowe.
One answer is to base animal feeds on single-cell proteins (SCPs), produced through a fermentation process involving yeast, bacteria or algae. Plants can be located anywhere that there's an available feedstock for the micro-organisms: methane, ethanol, sugar, biogas or even wood.
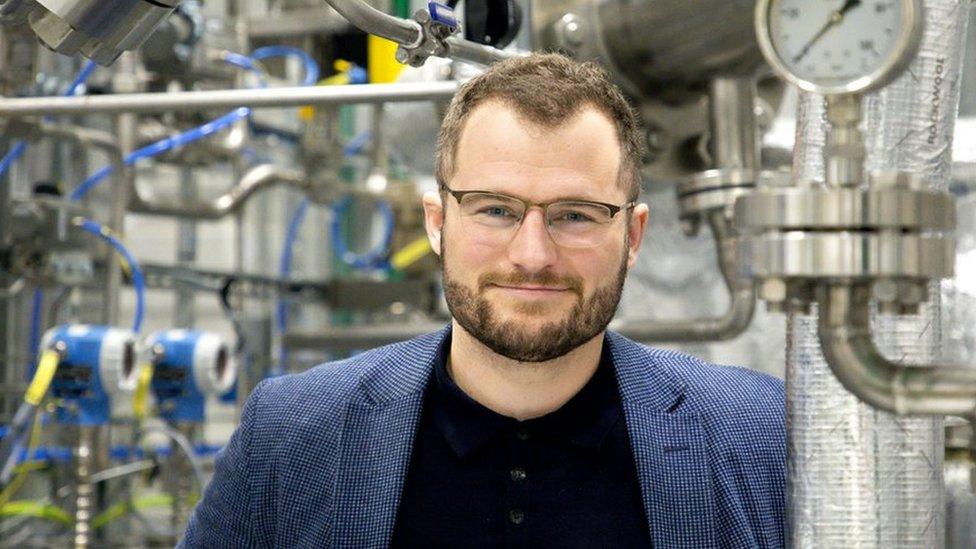
Peter Rowe is the chief executive of biotech firm Deep Branch
Through a project called React-First, which has received £3m in funding from Innovate UK, scientists are working to reduce the carbon footprint of animal feeds.
Along with Deep Branch, the project involves academics and companies including Drax, the UK's largest renewable energy producer, and supermarket Sainsbury's.
It's now producing a high-protein feed called Proton - more or less from thin air.
The process is based on a proprietary gas fermentation process, by which microbes are fed carbon dioxide, along with hydrogen - produced using an electrolyser - and water. They then produce the Proton protein as waste material.
The biggest challenge for any SCP manufacturer is achieving commercial scale, says Laura Krishfield, a research associate at analyst firm Lux Research.
"Single-cell proteins come with a huge investment cost," she says. "We've seen claims that commercial facilities are going to cost over the $100m (£72m) mark, so these facilities are not going to be cheap. And many of these facilities also come with other key challenges, such as access to the gas feedstock."
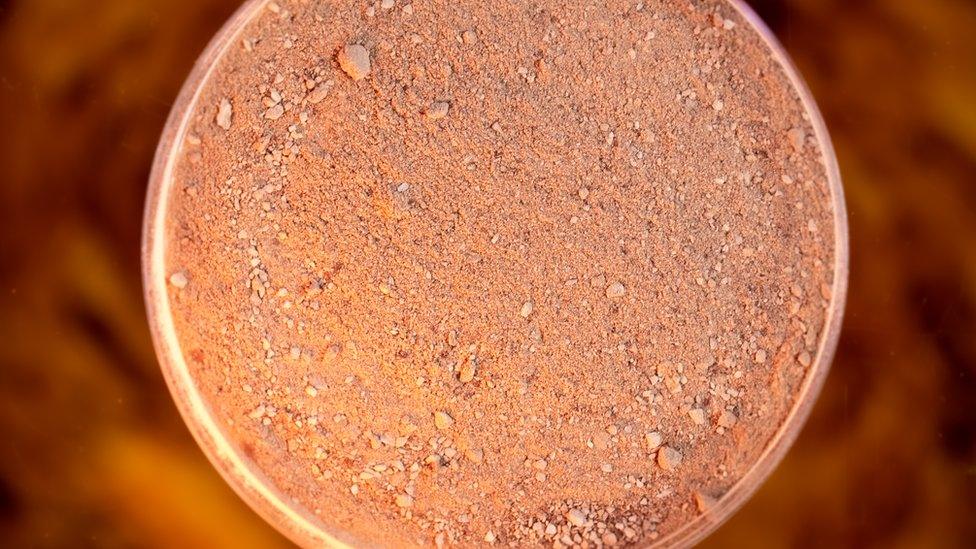
The Deep Branch protein can be created from waste CO2 and hydrogen
In the case of Deep Branch, industrial emissions provide the CO2 feedstock, both for the UK pilot and for a "scale-up centre" at the Brightlands Chemelot Campus in the Netherlands that has received funding from the European Union's Horizon 2020 EIC Accelerator programme.
"We see great value in partnering with people like Drax, and the reason for this is that they are working towards having a process whereby all the CO2 they create is stored and captured underneath the North Sea," says Mr Rowe.


"They're going to a lot of effort to put in the infrastructure, so essentially we have access to our CO2 in the same way as on a residential basis you have access to natural gas and electricity: it becomes a utility for us basically. And the same is true for hydrogen, which is the other main input we require."
By producing the feed close to where it's needed and using waste products as the fermentation feedstock, the carbon footprint of the protein is cut by 90%, compared with traditional feeds. And that, says Mr Rowe, cuts the carbon footprint of the salmon itself - including transport and packaging - by a quarter.
"So you can make a really big sustainability difference by simply swapping out one ingredient in the feed," he says.
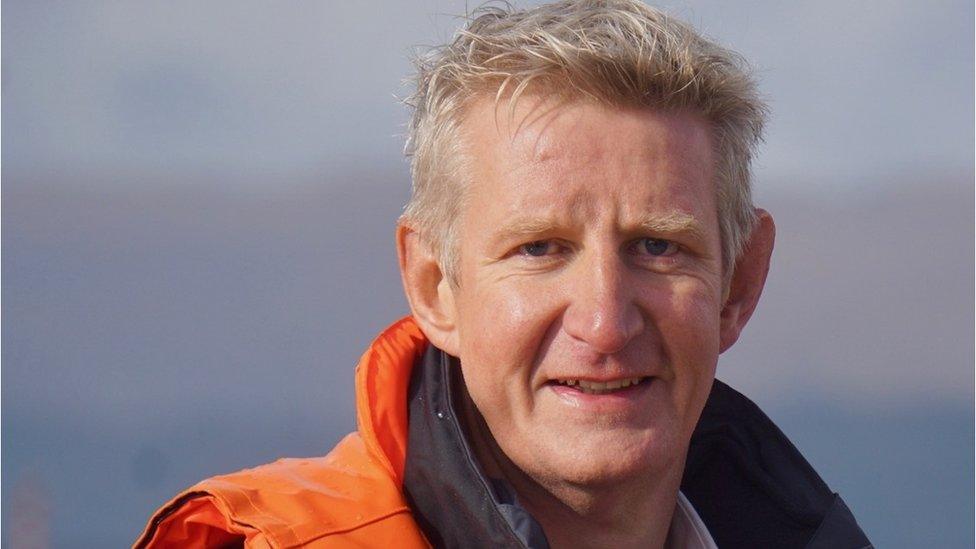
Rory Conn from Scottish Sea Farms says plant-based feeds for salmon are becoming more common
Rory Conn, sales and commercial manager for Scottish Sea Farms in Stirling, says that in recent years there has been a move towards more plant-based salmon feeds.
"But I think in general we've reached the point where we've gone as far as we can," he says.
"SCPs are interesting, and I think we see that as the future direction of travel - further enhancing the sustainability of salmon feeds."
Also boosting interest in SCPs is the question of national food security, says Joshua Haslun, a senior analyst with Lux Research.
"It's countries like Singapore where they're talking about vertical farming and aquaculture, and how you can begin to lower your risk around food security."
Right now, SCP production of all kinds is comparatively small scale, with Lux Research predicting that it will only become cost-effective at volumes of around 10,000 tonnes per year.
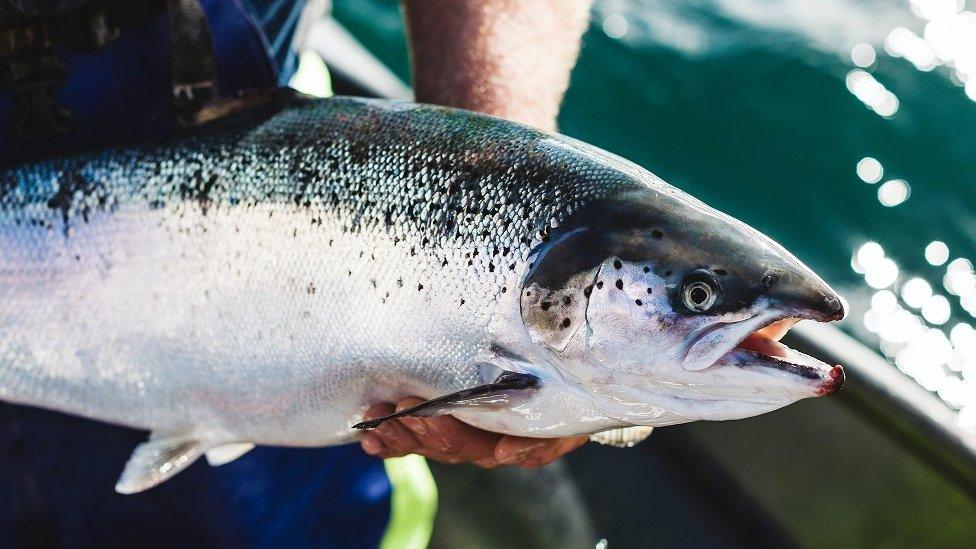
Food for fish... and then humans?
"This isn't a silver bullet for all the world's protein requirements, far from it," says Deep Branch's Peter Rowe. "But it is a very nice way to support additional protein sources that are out there."
So could SCPs become a source of protein for humans?
"The developers of single-cell proteins are seeing that as a long-term strategy for now. I do think there's going to be regulatory hurdles to jump through," says Lux Research's Laura Krishfield.
"And then you have to think about the formulation and is it going to taste good. There's also the whole issue of acceptance."
Mr Rowe, though, is more optimistic.
"It's relatively neutral in terms of flavour and colour, which means it'll be very versatile for use in a whole range of different products."