The tough little bottles crucial to fighting Covid
- Published
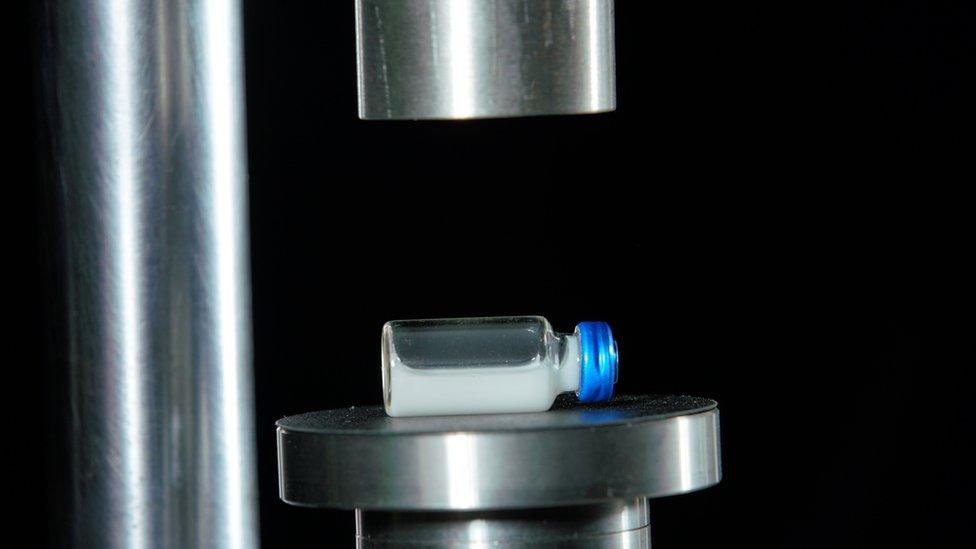
Vaccine vials have to be able to withstand significant stress
The pharmaceutical company worker stood at the top of a stairwell, holding a tiny glass vial in their hand. They held the vial out, peering at the ground three storeys below and dropped the vial. On purpose.
"It bounced incredibly," says Rob Schaut, scientific director of Corning Pharmaceutical Technologies. He co-invented the glass used to make the vial and was told about the stairwell incident by a customer who had wanted to test how strong the glass was.
Staff at the unnamed firm had attempted to break the vials during stress tests in their lab but couldn't, so they took to the stairs.
"This was the most severe test that they could find," adds Dr Schaut.
Corning is the maker of Gorilla Glass, a specially strengthened glass used to make super tough smartphone screens. But the company has a long history and, among other things, also invented early versions of the optical fibre cable used for internet communications.
It is one of just a handful of firms that makes glass vials for the pharmaceutical industry, where containers for drugs or vaccines must meet extremely high safety standards, including being shatterproof and resistant to extraordinary temperatures.
Other companies in the industry include Germany's Schott, founded by Friedrich Otto Schott, who invented borosilicate glass in 1897. This toughened material is still used for pharmaceutical containers today and Schott says that three-quarters of the world's Covid-19 vaccine projects use its products.
But Corning has captured the industry's attention lately with the strength of its Valor glass product, which was introduced in 2017.
"It's basically the Gorilla Glass for pharmaceuticals," says Steven Fox, an analyst at equity research firm Fox Advisors.

Corning's Valor glass is melted and hot-formed into tubes
Corning says vials made with Valor glass, being so robust, can be filled much more quickly at manufacturing sites, increasing the speed of production by up to 50%, according to the company. That is a potentially crucial feature in a year when the world requires billions of vaccine doses in as short a time as possible.
The speedier filling is possible partly because of the vials' ability to handle greater mechanical stress. But it is also due to the fact that, thanks to a special coating, the vials create less friction when hundreds of them rub against one another on a production line. Rather, they glide together swiftly in neat groups and are less likely to fall over and require manual intervention.
Glass is made from the silica found in sand, which gets melted down and mixed with traces of other materials. In the case of Valor aluminium, calcium and magnesium are added to increase the strength of the material.
During production, Valor glass is melted and hot-formed into tubes that are cooled and reheated before being shaped into vials. Dr Schaut explains that the next step involves a chemical strengthening technique similar to the one used for Gorilla Glass.
By submerging the vials in a molten salt bath, sodium ions in the glass are replaced with larger potassium ions. This has the effect of "stuffing" the glass surface to make it tougher, says Dr Schaut. "When we do that, it places the glass surface under compression making it very, very strong."


The vials aren't just designed to take a ham-fisted beating, they're hardy on a microscopic level, too. Among the headaches Corning's researchers sought to solve with Valor glass was a phenomenon called delamination - in which microscopic bits of glass flake off the interior of glass vials and mix with the vaccine or drug they contain, potentially reacting with and damaging the pharmaceutical product.
Boron and sodium can evaporate from glass during the vial manufacturing process, which destabilises the glass surface, making it susceptible to delamination later when the vial is filled. By eliminating boron and removing sodium from the glass surface, Corning prevents this evaporation from occurring, which keeps the glass intact.
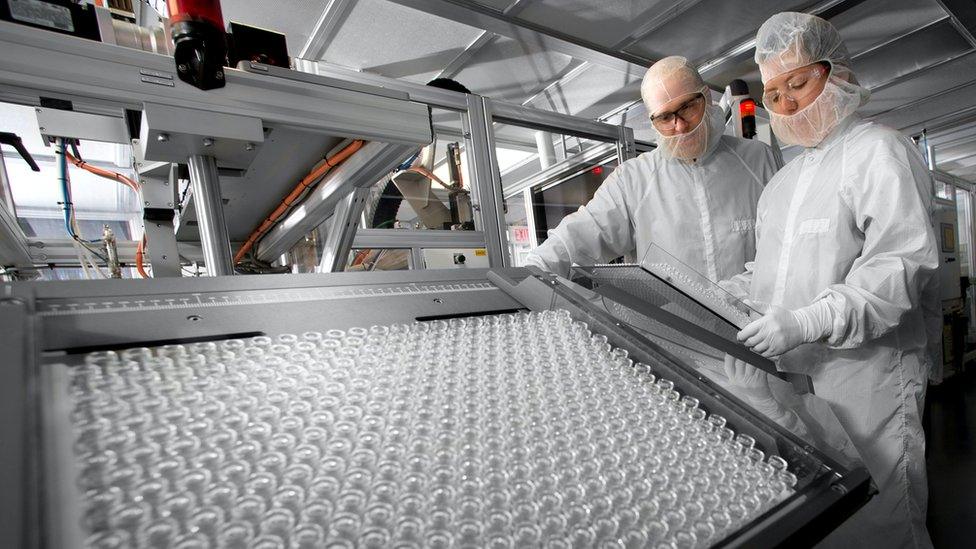
An extra layer is added to vials to reduce friction between them
The final step is to add a polymer coating to the glass vial. This is what reduces friction between the vials as they clink together on production lines. That lack of friction also lowers particulate, microscopic glass dust kicked up when the vials jostle. It too can contaminate pharmaceutical products.
Covid-19 vaccines that use mRNA, such as those made by Pfizer/BioNTech and Moderna, require storage at around -80C. Valor glass can withstand temperatures from between -180C and 400C.
Resistance to extreme heat is useful because pharmaceutical firms wash vials and heat them to around 350C to sterilise them before filling them with products.
The robustness of glass vials is important but in a race to vaccinate the world, quantity may be just as important as quality. Schott has said it aims to have churned out two billion vials by the end of 2021. US-based manufacturer SiO2, which makes vials out of plastic and then coats them with a thin layer of glass, hopes to have made up to one billion by April this year.
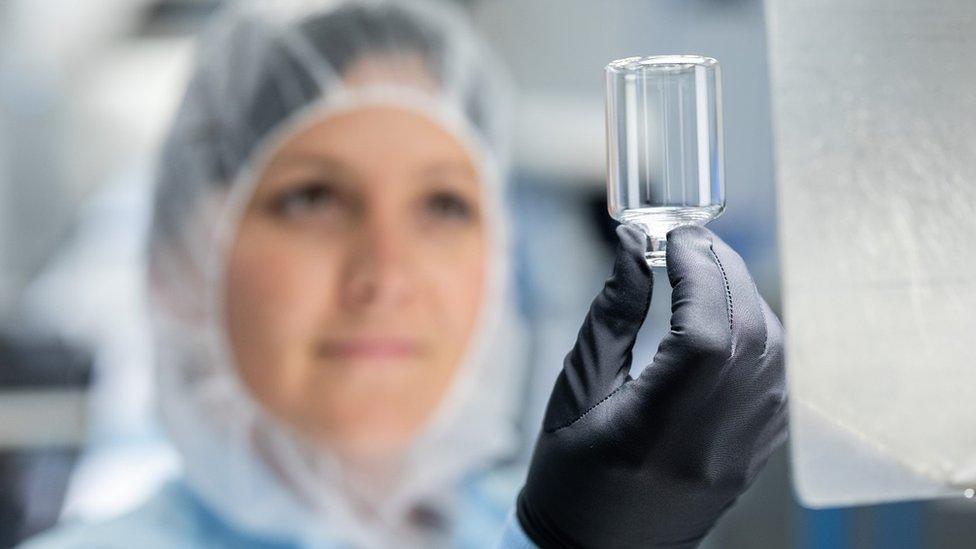
Schott says it will have churned out two billion vials by the end of 2021
Corning has not revealed its production target for Valor glass vials in 2021 but the company has accelerated the construction of a new manufacturing plant in North Carolina, which will open later this year.
Whether enough vials will be available in time is now a matter of supplies, manufacturing capacity and distribution. But Dr Schaut is confident the glass he co-invented will make a difference.
"Never did I imagine that there would be a pandemic that would need our invention," he says.
"I hope this gets the world through this pandemic and gets vaccines in the arms of people who need it."