The hunt for a new way to tackle clothing waste
- Published
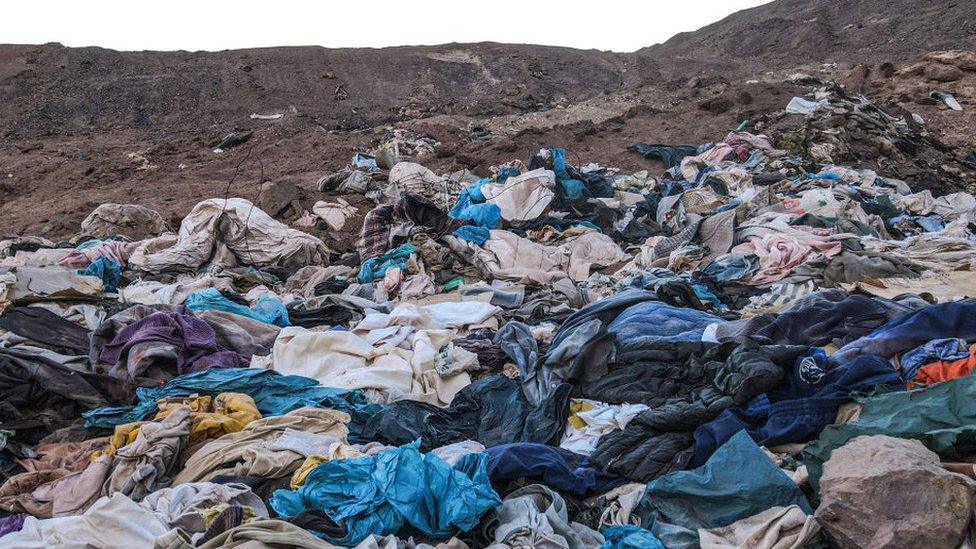
A large amount of waste clothing had been dumped in northern Chile
Earlier this year, a satellite photo of a mountain of discarded clothes in Chile's Atacama Desert went viral.
Clearly visible from space, it once again raised questions about the amount of waste the fashion industry is creating, and what we can do about it.
While natural fibres such as cotton and wool will decompose, most manmade fibres, such as polyester and nylon, are not currently biodegradable. They will instead remain in landfills, or where they have been dumped, for decades or even hundreds of years.
However, a US-based scientific organisation is continuing work to find a natural way of getting waste polyester and nylon to quickly decompose.
"One of the approaches that we are looking at is how you break down these complicated materials, and in a way that actually gets rid of the toxic effects of dyes and coating," says Beth Rattner, the executive director of the Montana-based Biomimicry Institute. "Using biological materials, whether that be enzymes or bacteria, to create new materials."
She adds that the aim is to "take the existing mountains of clothing waste and turn them into something that's biocompatible".
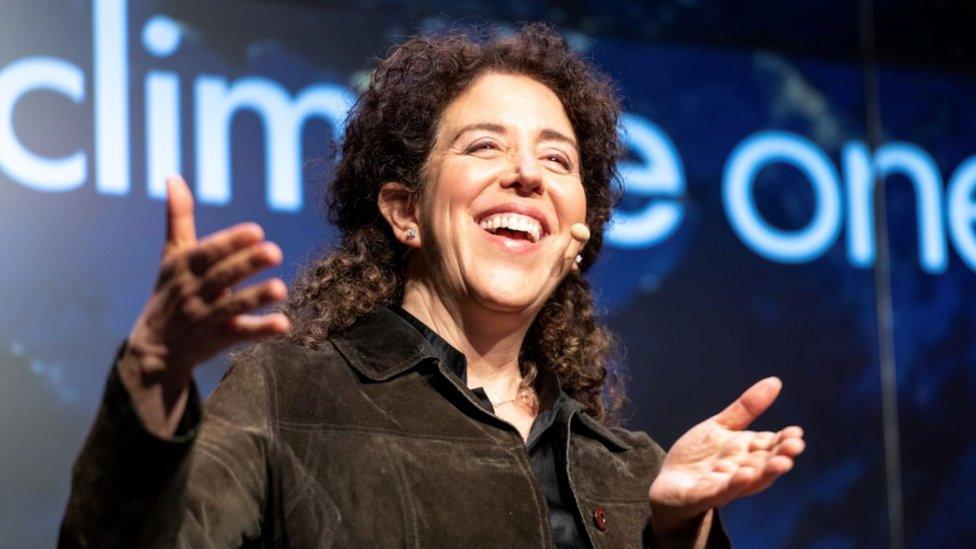
Beth Rattner and her team are working on ways to naturally break down manmade fibres
The Biomimicry Institute's project - dubbed Design for Decomposition - will choose tech partners later this year, and report back in 2024.
Ms Rattner says that the new processes it is exploring can not only help break down existing fabrics in more planet-friendly ways, but could also in future form the basis of new innovative materials.
"Instead of dyes you could use the structure of the fibre itself, the same for water repellency, rather than coating it, or to make wrinkle-free fabrics."
While the term "fast fashion" was originally coined to refer to the short length of time clothes took from going from design stage to shop, it has come to mean endless consumption of cheap clothes.
According to the UK's Ellen MacArthur Foundation, which campaigns for more recycling, every second there are enough garments thrown away to fill a rubbish truck, with less than 1% recycled into new clothes.
It means, says Jules Lennon, leader of its fashion programme, that "today's fashion system is broken".
"More clothes are being made than ever before, yet we are using them less," she adds. "The fashion industry is responsible for more annual greenhouse gas emissions than all international flights and maritime shipping combined.
"It is also a significant contributor to biodiversity loss due to soil degradation and waterway pollution caused by raw material production methods and intensive washing and dyeing processes."
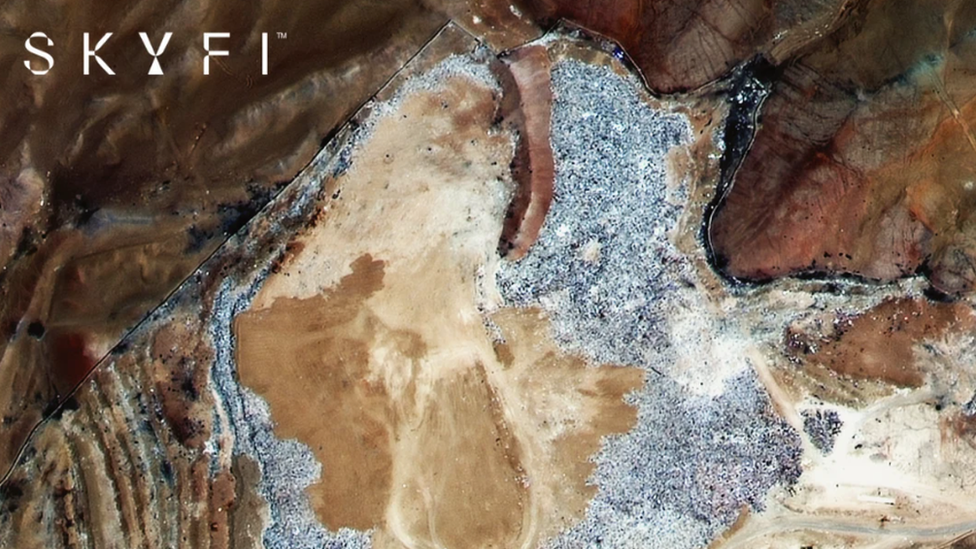
The clothing mountain in Chile's Atacama Desert was visible from space
Jean Hegedus, head of sustainability at Lycra, the maker of the stretchy man-made spandex fabric of the same brand name, is well aware of the problems.
"It's estimated that about eight to 10% of all carbon emissions come from the textile and apparel industry, so we know that we have to change," she tells the BBC.
Change for US-based Lycra means finding a natural replacement for the spandex that makes up the majority of its material. Spandex, like nylon, is derived from petroleum.
"We found that if just one component, which makes up 70% of the total fibre, could be swapped from a petroleum-based fibre to a renewable one, it would reduce the product's carbon footprint by 44%," says Ms Hegedus.
Lycra's journey to find this new raw material began in the US state of Iowa. There a company called Qore is working with farmers to source the corn being used to create a new material called Qira, which will become a key component of Lycra.
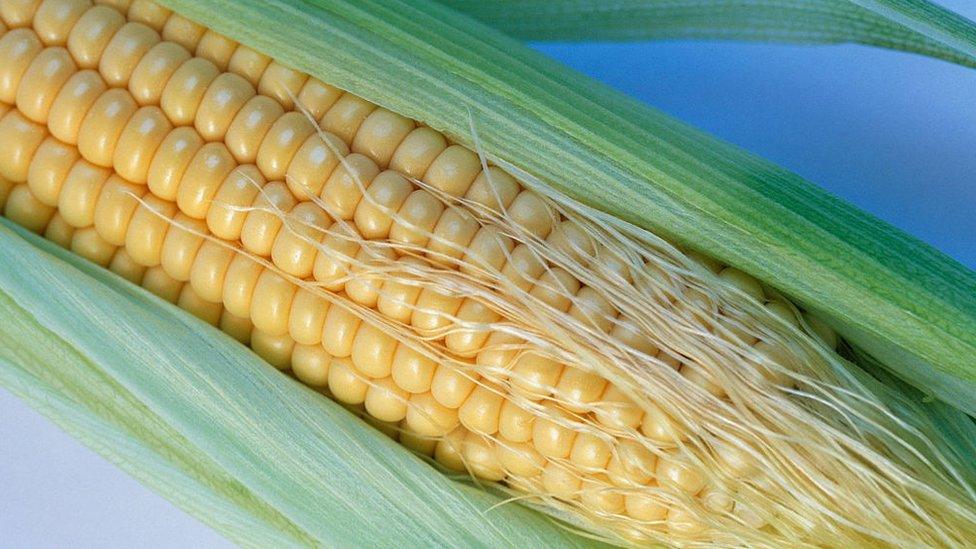
Lycra is aiming to switch to using sweetcorn as a key ingredient in making its fabric
"The core product is really interesting," says Ms Hegedus. "It's made from what we call 'industrial dent corn'. So it's not like sweetcorn that's used for human consumption. It's specifically grown for things like materials, or to go into paper, or for animal feed."
Lycra is now building a large wind-powered factory in Iowa to make its material using Qira instead of polyester. This is due to start production next year, and Lycra wants 70% of its fibre content, external to come from the new corn-based fibre.


New Tech Economy is a series exploring how technological innovation is set to shape the new emerging economic landscape.

Ms Hegedus says the switch will make its material 10% more expensive to manufacture, a cost that it will share with its clothing firm customers. She adds that most "are very positive" about the change.
Lycra says that the use of Qira has no negative impact on the functionality or comfort of its products. However, the first version of the corn-based Lycra will not be recyclable, but the firm says it is "working on" that problem.
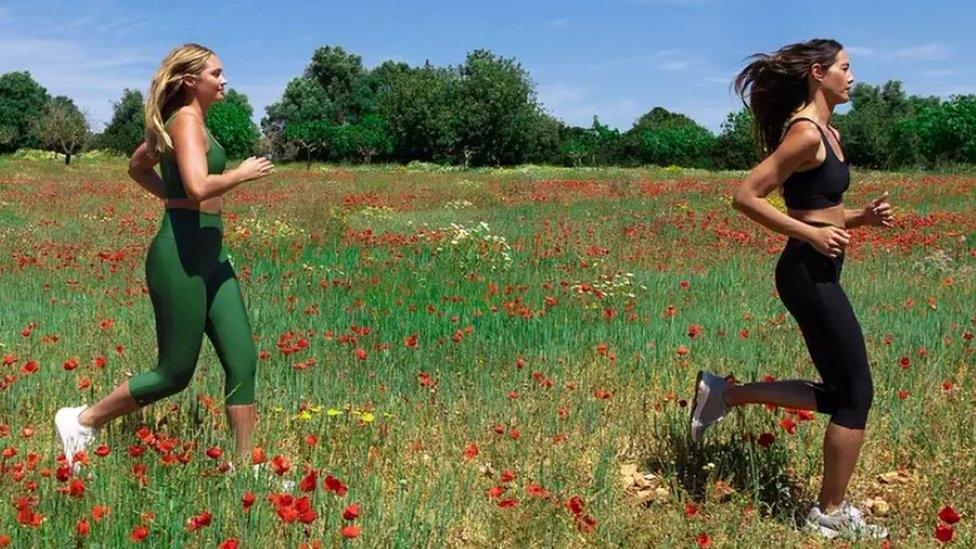
Lycra is the best-known producer of spandex, or expanding, fabric
The manufacture of clothing using natural materials not previously associated with textile production is a growing sector.
Take US firm MycoWorks, which produces leather-like material from mushroom mycelium (the roots of the fungi). Its first large-scale manufacturing facility is due to open in South Carolina at the end of the year, and aims to produce several million square feet of its material, known as Reishi, annually.
Meanwhile, companies such as UK-based Faber Futures are exploring the use of a soil-dwelling bacteria called streptomyces coelicolor. It has the potential to revolutionise the textile dyeing process, because it produces a rainbow of pigments as part of its normal life cycle, from vibrant blues and reds to subtle yellows.
In Finland, a company called Spinnova turns wood pulp into clothing fabric. It breaks down the pulp into micro-scale fibres which it turns into a cotton-like thread.
With customers including H&M and Adidas, earlier this year it opened a factory in Jyvaskyla, western Finland, with the aim of manufacturing one million tons of fibre annually by 2033. The factory is carbon-neutral - the only by-product is heat which is pumped back into the local heating system.
Spinnova's fibres can be recycled and re-spun, but the firm's interim CEO Ben Selby acknowledges, that for this type of "circular textile loop" to work, brands and customers will need to change.
"The whole industry needs to start to better at collecting back old garments that can then be recycled," he says.
Numerous fashion retailers now offer "takeback" schemes - you can return old clothes that they will recycle. However, one report this year,, external which tracked 21 returned items from 10 fashion brands, found that three-quarters were either destroyed, left in warehouses, or exported thousands of miles to Africa to form new unwanted clothes mountains.