Bloodhound diary: Making tracks in 2013
- Published
A British team is developing a car that will capable of reaching 1,000mph (1,610km/h). Powered by a rocket bolted to a Eurofighter-Typhoon jet engine, the Bloodhound SSC (SuperSonic Car), external vehicle will mount an assault on the land speed record.
Wing Commander Andy Green, world land-speed record holder, is writing a diary for the BBC News website about his experiences working on the Bloodhound project and the team's efforts to inspire national interest in science and engineering.
Not long back from Los Angeles, where I went to launch a movie. OK, so the film was only three minutes long, but still, I can claim a Hollywood film launch!
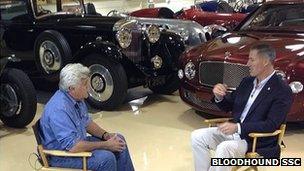
Jay Leno talks Bloodhound
The Future of Speed was made in a Bentley Mulsanne at 190mph on Bonneville Salt Flats (and at 190mph, three minutes is a long time).
The really fun bit though was doing an interview with Jay Leno in his world-famous garage. If I ever win the Lottery (which is unlikely - I don't buy any tickets) then I'd have a garage like that, perhaps with less cars and more aeroplanes, but the same general idea.
While I was in LA, our senior engineer Brian Coombs and veteran aerodynamicist Ron Ayers were hard at work on the Bloodhound track.
The rainy season will start anytime soon on Hakskeen Pan, in the Northern Cape of South Africa, so this was their last chance for a few months.
They were there to test the desert/wheel interaction, and they learned a lot more than we had expected (have a look at Ron's article for more detail, external). Unfortunately, it's not all good news, but if breaking the World Land Speed Record was easy, everyone would be doing it.
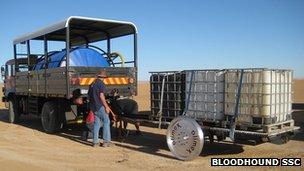
"Mad Max"
The team mounted two wheels to a purpose-built trailer, which was the result of a truly amazing effort from three engineers in South Africa - our huge thanks go Fabian, Hentie and Colin for working through the night, followed by a 25-hour non-stop drive to get it there in time.
They then filled "Max Max" (a good name for a collection of spare parts running on a desert!) with water to a total of 3.8 tonnes - half the mass of the fully fuelled 1,000mph car.
Towing the trailer along the desert would then tell us how deep the wheels dig into the desert, the width of the V-shaped grooves would show how consistent the surface is, and the changes over the new repairs would show how well the desert was recovering.
First, the good news. We've been debating how wide the wheels need to be, estimating somewhere between 90mm and 120mm at the rim, to support the full weight of the car.
The tracks left on the desert were mostly around 70mm wide, which means that 90mm should be more than enough.
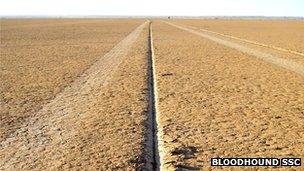
Good News – Thin tracks
Narrow wheels equals light-weight rims equals reduced loads at peak speeds.
To give you some idea, peak speed for the wheels is 10,300rpm at 1000mph, which gives a peak load of 50,000 times the force of gravity at the wheel rim.
To try and picture this acceleration force, if we put a 1kg bag of sugar on the wheel rim, it would exert a force of 50 tonnes (more than the weight of a fully loaded articulated lorry) at full speed. So reducing the total load on the wheel is a very good thing - and narrower, lighter wheels will do just that.
Next, the not-quite-so-good news. The surface hardness is a little uneven, with the recent repairs rather softer than the rest of the surface. I was surprised to find that the causeway repair, where the old man-made road was graded down to its original level, is actually harder than the surrounding lake bed surface.
That means that the car may have a tendency to jump upwards slightly as it hits the causeway - at around 600mph. However, the "jump" should only be around 10mm, as the wheels will be "planing" on the surface at that speed, and 10mm is well within the suspension travel of +/-50mm. So far, so good.
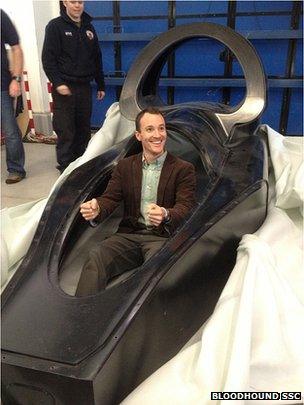
Can I have a go please?
Now the thing that could worry us the most. As the V-shaped keels are pressed into the surface with nearly two tonnes of load each, the small stones embedded just below the surface are forced against the aluminium surface and dig in. This was the same effect that we saw 15 years ago with Thrust SSC running on the stony surface of a Jordanian Desert. However, the damage on Hakskeen seems to be worse, particularly when we ran the trailer over the (harder) causeway surface.
We've got several options to consider. The damage should not be as bad on the final forgings, which will be a harder alloy than these test wheels. We can reduce the load on the point of the wheel by reducing the angle of the "V", spreading the load over more of the tread. We can make our early runs south of the causeway (which still gives us almost 10 miles of track), to check the damage once the car is running at speed, when the wheel rut will be shallower and the stone impacts less deep.
Finally, if this is a major problem after we've done our first season of testing this year, we can look at making the wheels from steel if we need to - we know that they can be made thin enough, and steel should be more than hard enough.
All this could look quite worrying - but this is exactly what an "Engineering Adventure" is all about. If we hadn't made a trailer and tested the wheels, we wouldn't know about any of this until we arrived with a ready-to-run car later this year. As it is, the more problems we know about, the more solutions we can take with us. It makes the engineering task more challenging, but if breaking the World Land Speed Record was easy…
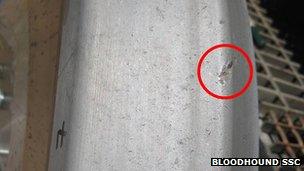
Bad News – Stone damage
The build of the car is progressing nicely. The rear lower-chassis has now been delivered to the Bloodhound Technical Centre in Bristol, while the rear sub-frame (the strong bit at the back that supports the rocket and rear suspension) is being manufactured. The team at Nuclear AMRC are doing impressive bits of machining to deliver some beautiful bits for the back end of the car.
The upper rear-chassis, which carries the jet engine and supports the fin (have you put your name on the fin yet?, external Over 13,000 people already have!) is now about to be manufactured.
The Hyde engineers have been working closely with the Bloodhound team on the design of the fin, which includes the stress analysis. This looks at the loads on the structure, as well as the natural frequencies (the rate at which each part will "vibrate" under load) - and the challenge is to make sure that the different frequencies on the car don't interfere with each other!
For example, the frequency of the fin is around 45 Hertz - that's 45 oscillations per second when it's being buffeted by supersonic airflow. Another major input is the airflow around the airbrakes, so we need to make sure that the airbrake frequency is nowhere near 45 Hz.

And the Rocket goes through here...
Bloodhound stress engineer Roland has been looking at two options for making the airbrakes, aluminium (frequency - 45 Hz!) and carbon fibre (frequency - 80 Hz), so the need to avoid 45 Hz makes the choice fairly simple. Add in the difference in mass between aluminium (88kg) and carbon fibre (18kg) and there's no contest - we're having carbon fibre panels for the airbrakes.
URT is busy laying up the carbon fibre monocoque - which forms the structure around my 1,000mph office - and has already delivered some fibreglass test pieces ("splashes") so that we can start fitting out the cockpit. It's starting to feel very real now - but that didn't stop our computational fluid dynamics expert Ben from jumping into the upper cockpit splash as it arrived, just to try it out.
Following our very successful rocket firing in October, external, we've conducted an independent review to confirm the results and the choice of rocket for us. We're grateful that some of the UK's leading rocket scientists found the time to mark our homework - and the rocket scored well!
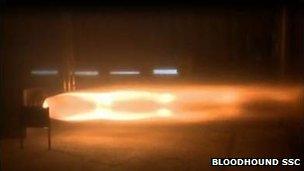
Rocket Power – and plenty of it, apparently
The review panel confirmed that the Falcon hybrid rocket concept would be capable (with some development, of course) of getting us to 1,000mph.
However, the panel did not agree with our measured thrust figure of 6.5 tonnes: they felt that, from their assessment of the rocket parameters, the thrust should be even higher than that - hope they're right! The next set of rocket firing tests will be in the New Year, so we'll know soon enough.
Just in case we haven't got enough going on right now, the Bloodhound Technical Centre is about to move. With the build of the car ramping up, plus a lot of support equipment and vehicles arriving soon, we need more room! We're staying in the Bristol area, and will probably move at the end of February. The bigger Centre should also give us more room for visitors, so if you want to come and see the world's first 1,000 mph car, join our 1K Supporters' Club, external and come to one of our open days - we'd love to see you there.
Have a truly supersonic New Year. We plan to!
- Published30 November 2012
- Published3 October 2012
- Published2 October 2012
- Published23 September 2012
- Published12 September 2012
- Published24 August 2012
- Published7 February 2011
- Published21 November 2010
- Published13 November 2010