Bloodhound Diary: All roads lead to South Africa
- Published
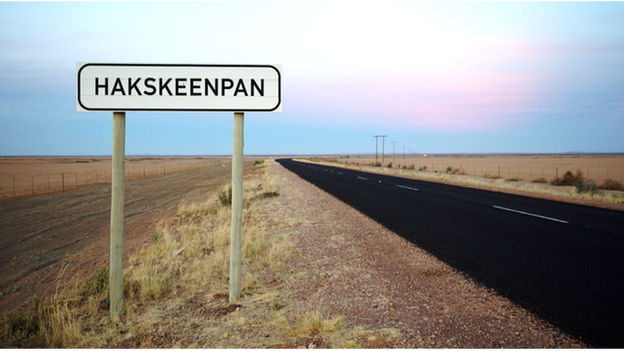
A British team is developing a car that will be capable of reaching 1,000mph (1,610km/h). Powered by a rocket bolted to a Eurofighter-Typhoon jet engine, the vehicle aims to show its potential by going progressively faster, year after year. By the end of 2019, Bloodhound, external wants to have demonstrated speeds above 500mph. The next step would be to break the existing world land speed record (763mph; 1,228km/h). The racing will take place on Hakskeen Pan in Northern Cape, South Africa.
Finally, the news we've all been waiting for… Bloodhound is going to the desert this year!
The accommodation is booked, deposits have been paid, and we're arranging charter flights and sea freight space as I write.
Bloodhound will touch down in South Africa in the middle of October for 3-4 weeks of "high speed testing" on the dry lakebed track at Hakskeenpan.
This high-speed testing is a key part of getting ready for an attempt at a new 800+ mph Land Speed Record next year.
We're going to take our slow-speed runway car, which we tested at 200mph back in 2017, and turn it into a high-speed racing car.
To do this, we're fitting the high-speed metal wheels, brake parachutes, pressure sensors, wheel fairings, and so on, ready for speeds well in excess of 500mph.
If things go really well for us out in South Africa, we might even finish up at a speed starting with a "6", but anything over 500 will allow us to test the aerodynamics, wheels, chutes, etc., so we won't be pushing too hard just yet. We'll save that for next year.
The first thing to test is the high-speed desert wheels.
Each wheel weighs 95 kg and is forged from solid aluminium, without any tyre on it.
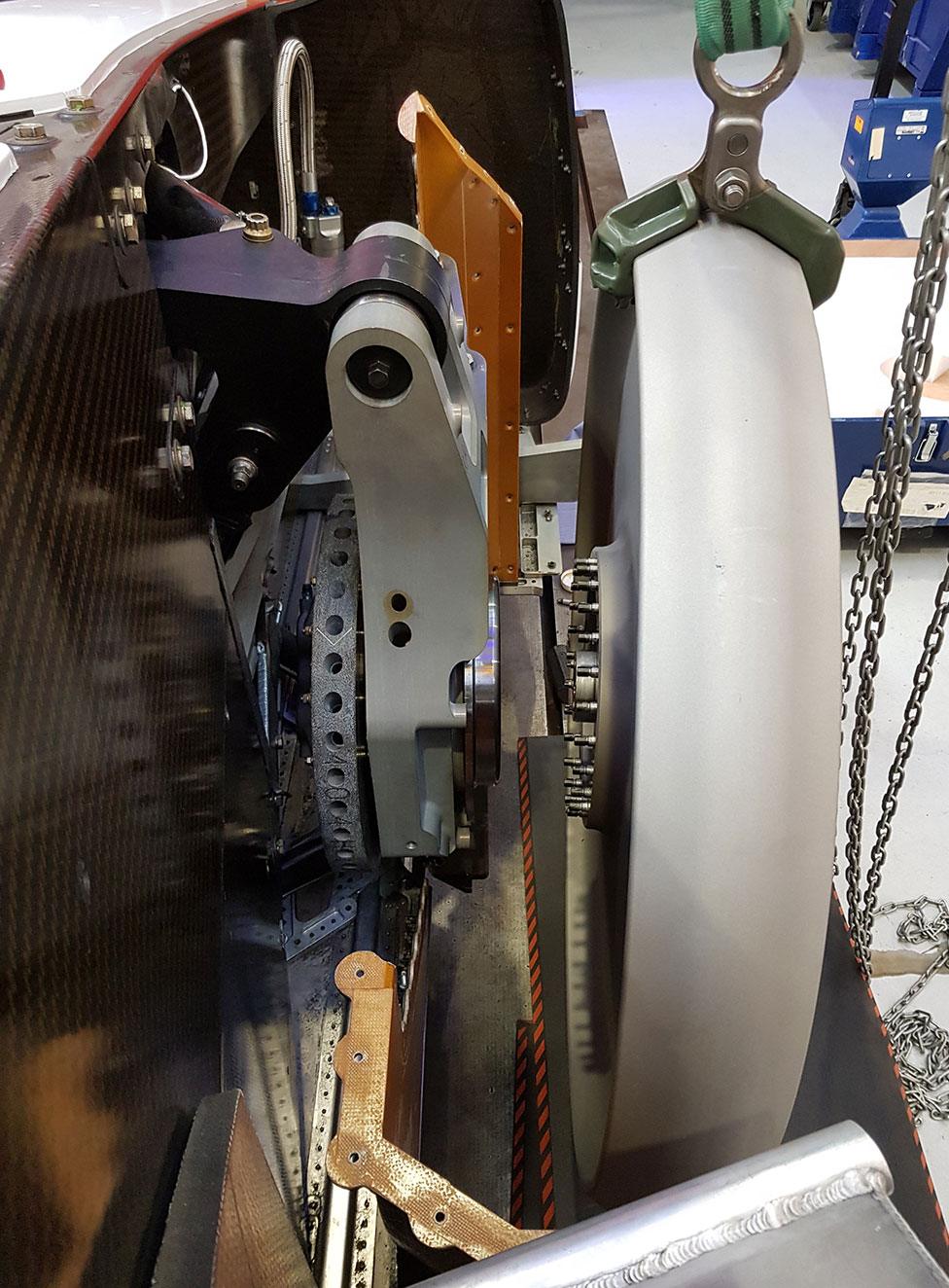
Ready for some ice-driving?

At 1,000mph, the wheels experience 50,000 times the force of gravity trying to tear the wheel rim apart, so it has to be solid metal; nothing else will cope with the extreme loads. So far, so well understood. Now we get to the bit that we don't know - how will these wheels behave on the desert surface?
Metal rims running on the hard mud surface of Hakskeenpan will have very little grip due to friction.
Normal road cars rely on tyre grip for their stability and safety, and tyre companies spend a huge amount on developing the right rubber compounds for maximum grip.
None of that helps us, as 50,000-g would destroy any rubber tyre, so we are working with the unusual (and poorly understood) dynamics of solid metal wheels.
We have given the metal wheels some lateral grip on the desert surface by making them a shallow "V" profile.
As the car runs along the track, the wheels cut ruts in the mud surface, providing the sideways grip that we need. Unfortunately, the faster we go, the shallower the ruts become - at slow speeds (200mph), they will be 10-15 mm deep, but at supersonic speeds the wheels will be making tracks less than 5mm deep, which will provide almost no sideways grip.
There is some good news at supersonic speeds, as the aerodynamic grip will be huge, so that car will get pretty much all of its directional stability from the supersonic airflow.
This should also give the car some very lively steering at high speeds, with the front wheels acting like rudders in the supersonic airflow, producing very rapid steering responses.
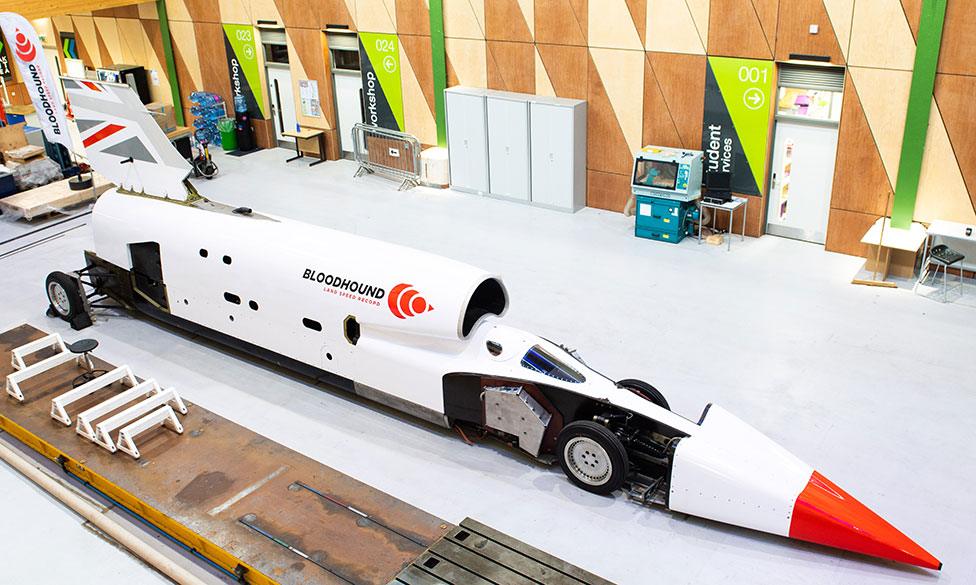
Now for the bad news. As the car accelerates, the mechanical wheel grip goes down quite quickly, but the aerodynamic forces (which depend on the square of the speed) build up much more slowly.
This means that at "medium" speeds (somewhere between 300mph and 500mph), there is very little surface grip from the wheels and there is very little aerodynamic response.
This is where controlling Bloodhound may well feel like driving on ice at 400mph.
I'm going to have to learn how to control the car as it accelerates from "normal" wheel grip below 200mph, through a period of almost-no-grip-at-all-oh-help-it's-all-over-the-place-like-driving-on-ice, to above 500mph where the steering is becoming super-fast.
Just to make things more complicated, we also need to assess the lateral stability as we increase the speed, so I need to learn how to control the car and try to measure its stability, all at the same time. Luckily, I love a challenge.
Once we've got on top of the steering, the rest of the testing might sound a bit tame, but there are still some other important things that we need to explore.
One of the key things is how to stop the car from high speeds.
We're using airbrakes and two separate brake parachutes, any one of which can stop the car by itself, to give us plenty of fail-safe.
If this seems a bit like overkill, just remember that going faster is optional, but once you get there slowing down is compulsory, so we have to get this bit right every single time.
The brake chutes are the same technology that has been used on previous cars, including the current record holder, Thrust SSC, so we know it works.
The chute canopy is about 2m across, on the end of a very heavy-duty nylon strop supplied by Marlow ropes, who normally make ropes like this for tying up small ships.
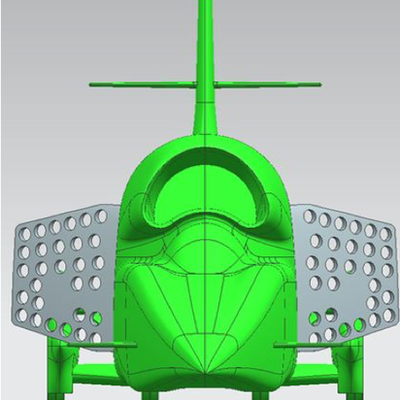
A gentle way to slow down
That might sound a bit low-tech, but it's exactly what we need to absorb the opening loads for the chutes.
At the maximum deployment speed of about 670mph, the chute will produce a drag force of around 9 tonnes, with an opening "shock" load of up to 12 or 13 tonnes.
It's a very rapid and violent process, which is why it's vital to test the whole system this year, before we go supersonic next year.
The airbrakes are a much more civilised way of slowing down. Large perforated panels open up on either side of the bodywork, towards the rear of the car, gradually increasing the drag in a way that doesn't try to tear the driver's eyeballs out. That's the good bit.
The downside is that the airbrakes will produce a huge amount of turbulence and vibration at the back end of the car, which we need to measure to make sure it's not going to break anything.
We are aiming to do at least one run with the airbrakes deployed, to see what the airflow is doing to the back end of the car.
This brings me to the next key area that we have to explore - the aerodynamics.
If you thought that aerodynamics is now all done in computers, then I'm going to have to disappoint you.
This is such a complex subject that the detailed measurements still have to be done by building things and testing them.
It's true for race cars (even slow ones, like Formula One), airliners, jet fighters, and it's certainly the case for supersonic Land Speed Record cars.
This year's testing will validate a lot of Swansea University's computer modelling and will also give us some very accurate drag figures.
To help with this process, we've got just shy of 200 pressure sensors fitted to the car, to confirm the exact pressures across the bodywork, with and without the airbrakes - fascinating stuff.
That's key to making sure we've got the right size of rocket fitted next year, when we take aim at 800mph and beyond.
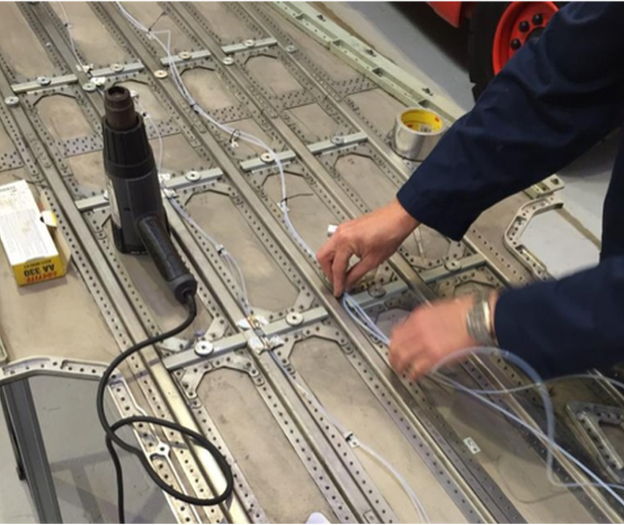
Plumbing in the pressure sensors - nearly 200 of them
The other really important thing we need to do this year is train ourselves, as a team, to operate the world's fastest car efficiently and safely.
We'll be on the Hakskeenpan track in the Northern Cape of South Africa, over 5,000 miles from home, running on a new surface using new wheels, new braking systems and new aerodynamics.
We've got a lot to learn before we can confidently say "800 mph here we come", so team training is going to be a key part of this year's testing.
Rest assured we'll be sharing it all with you as it happens.
The show starts in October. Not long to wait now.
- Published10 July 2019
- Published11 June 2019
- Published28 March 2019
- Published21 March 2019