Tomorrow's Buildings: Construction industry goes robotic
- Published
Mexico City is trialling new technologies to tackle air pollution
The building site of the future is going to look very different to the one we are all used to today.
Instead of men in high-visibility jackets and hard hats, there are going to be drones buzzing overhead, robotic bulldozers and 3D printers churning out new structures.
That at least is the hope of those making technological solutions.
But first they have to convince the traditionally risk-averse construction industry that such change is necessary.
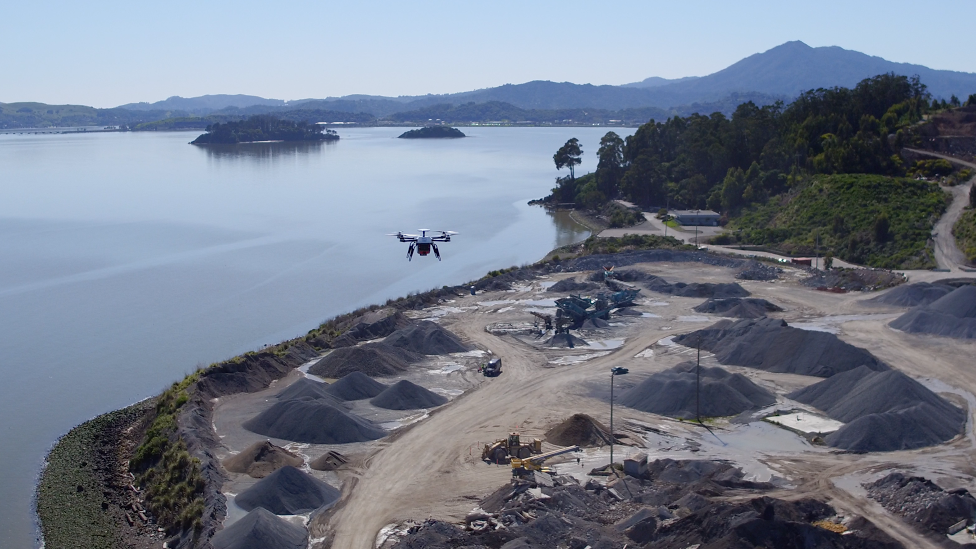
Drones offer a bird's-eye view of a building site
US start-up Skycatch is using drones on some high-profile building projects - although it cannot name them because of commercial sensitivity.
The drones give a bird's-eye view of a site and provide progress reports, speed up the logistics of construction by monitoring deliveries and offer real-time updates on any changes that may need to be made to the plans.
Japanese construction machinery giant Komatsu has gone one step further - using the Skycatch drones to provide the eyes for automated bulldozers. The drones send 3D models of a building site to a computer which then feeds the information to unmanned machinery to plot their course.
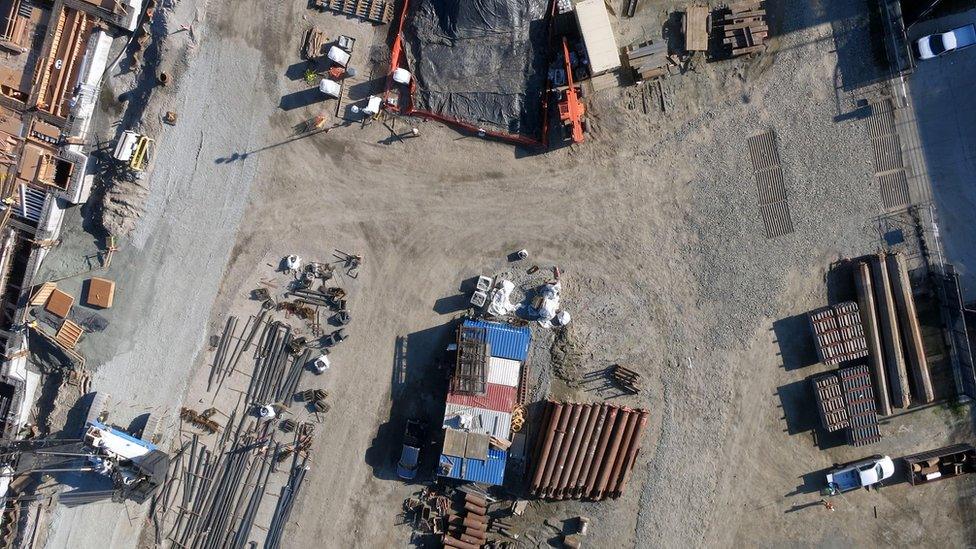
Drones could provide the 'eyes' for automated vehicles on a building site
Skycatch's chief executive Christian Sanz thinks such combinations of technology could kickstart a robotic building site.
"The more visible data that you have on a site, the more you'll see machines and robots moving things around rather than humans."
One of the potential solutions to the housing crisis could be 3D printing, which is already making an impact on the construction industry - cutting both the time and cost of building houses.
The UN estimates that by 2030 approximately three billion people will require housing and has mooted 3D printing as one possible solution.
A team in the School of Civil and Building Engineering at Loughborough University has been working on the technology since 2007, first developing a 3D concrete printer within a frame and more recently adapting it to work with a robotic arm.
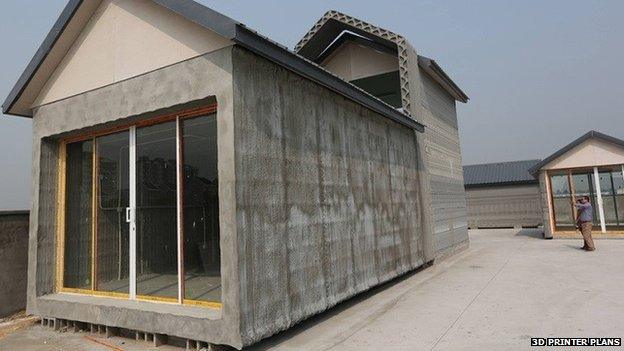
Chinese company WinSun claimed to have 3D printed 10 full-size single-storey houses in one day
Using a robotic arm means that the team can print up to 10 times faster and create a huge variety of forms, including curved, hollow and geometrically complex shapes.
The group's YouTube video of the system in action has garnered over half a million views, something lead researcher Prof Simon Austin finds astonishing.
"I am still trying to get my head around the fact that a video about concrete - a material normally seen as boring - has had so many views," he said.
It indicates, he hopes, a shift in thinking - not only from the public but also from the construction industry, which is traditionally "risk-averse".
"I think that companies who become early adopters of 3D printing will learn a huge amount about automation and robotics and how they can be exploited on a site," he said.
The team decided to work with concrete as their main material because as Prof Austin says: "There are very good reasons why the built world is made mainly out of steel and concrete - including durability, mechanical performance and aesthetic properties."

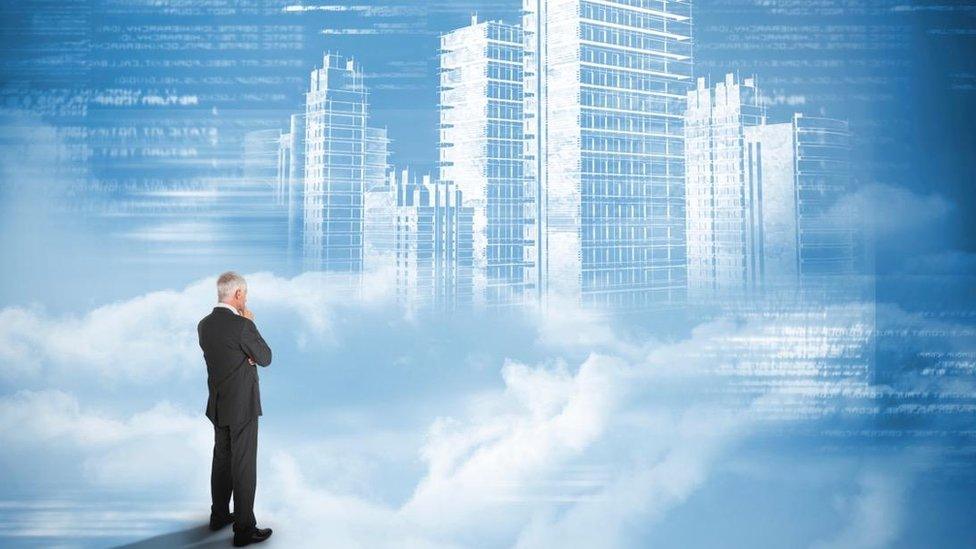
Will we need to work in offices in the future?
Tomorrow's Buildings

Two years ago the research moved into a new phase and the team is now building an industry prototype, working with partners - construction firm Skanska, architects Foster and Partners, materials supplier Tarmac and Scandinavian robotics firm ABB.
The prototype is being tested at the Manufacturing Technology Centre in Coventry, which to date has only worked with hi-tech industries - this represents its first collaboration with the construction industry.
Skanska's director of innovation Rob Francis has high hopes for the technology.
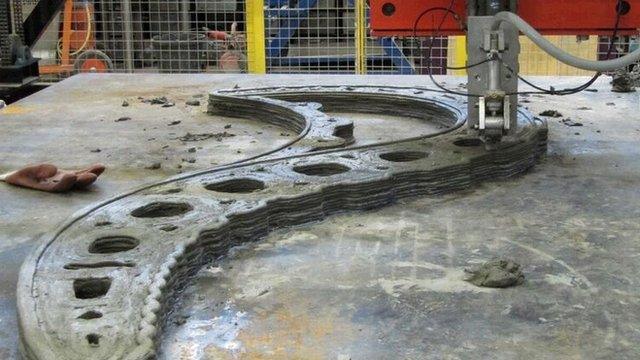
The 3D printing system designed at Loughborough means that a variety of shapes and designs can be created
He said: "3D concrete printing, when combined with a type of mobile prefabrication centre, has the potential to reduce the time needed to create complex elements of buildings from weeks to hours. We expect to achieve a level of quality and efficiency which has never been seen before in construction."
Prof Austin sees the future of 3D printing in construction as a way of printing key components of buildings rather than whole structures created in China.
"I'm not convinced 3D-printed concrete would appeal to the high-end of the housing market and in the developing world labour is cheap and they have developed ways of building homes with local materials that have worked for hundreds of years.
"So the idea of bringing a gantry and printing machine to a site to print whole houses is a bit far-fetched," he said. "On the other hand, printing building components where a variety of geometry is sought is an attractive approach that will soon be realised."
Nature-inspired designs
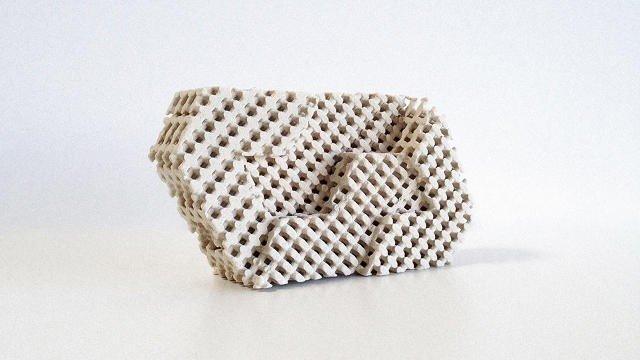
3D-printed bricks filled with water could help regulate temperatures
It isn't just concrete that is getting a hi-tech makeover.
Design studio Emerging Objects has come up with 3D-printed porous bricks called Cool Bricks that can be filled with water to bring down temperatures.
Each 3D-printed cool brick, has a three-dimensional ceramic lattice-like structure that can hold water in its pores, like a sponge. When air flows through the porous brick it absorbs evaporated water vapour, becoming cooler in the process.
According to the designers, if all the walls of a home were built with porous, water-logged cool bricks, the air flow through them could bring down the home's internal temperature.
Increasingly designers and architects are looking to nature for inspiration and at the Institute for Computational Design, David Correa is convinced that buildings will only be truly smart when they are built with smart materials - many of which can be found in the natural world.
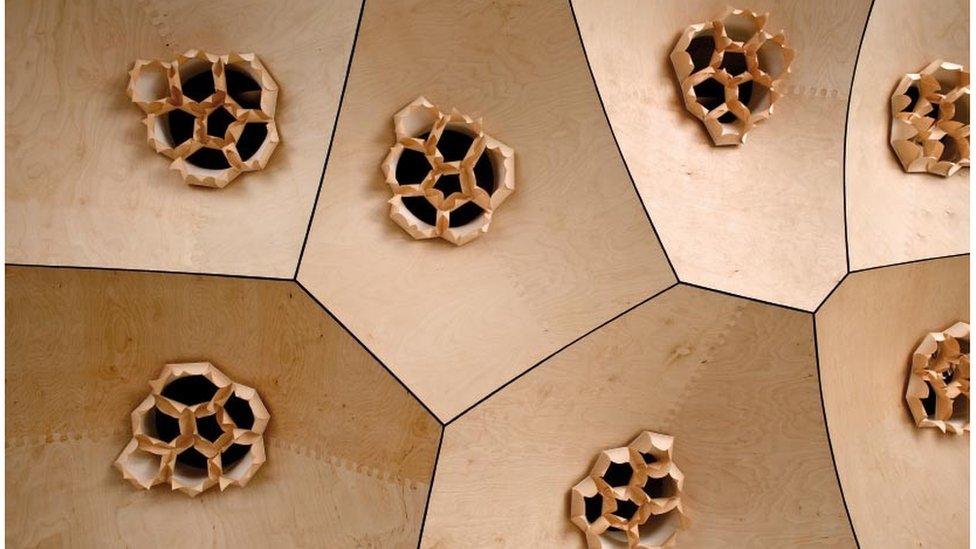
Roofs with pine cone-like openings could end the need to open a window
"Things that have lots of mechanics, or software that gets outdated or sensors that go wrong mean that maintenance of smart buildings is an ongoing battle," he told the BBC.
"Pine cones on the other hand have been working for millions of years so imagine a roof surface that can open when it is sunny and close when it rains."
The team designed just such a structure and is now working on creating new materials that can respond to a variety of environmental conditions.
Building with air
For Allison Dring, head of start-up Elegant Embellishments, it is important that the materials we build with give something back to the environment.
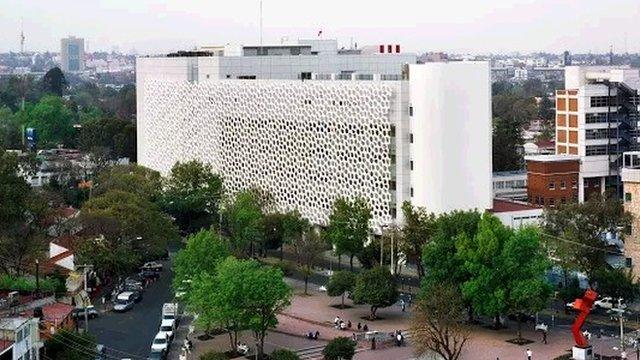
The facade is being used on a hospital in Mexico City where pollution is a huge issue
She has designed a smog-eating facade that is coated with a special paint made from titanium dioxide, a pollution-fighting technology that is activated by daylight. It absorbs the fumes generated from traffic and converts them first into nitric acid and then into calcium nitrate, which is harmless.
One of its facades has been put on the side of a hospital in Mexico City.
"It has reduced pollution of about 1,000 cars per day," said Ms Dring.
The firm is in talks with other building owners but, said Ms Dring, it can often be a hard sell to persuade them of the need for such a facade.
"Building owners have to think about investing beyond their building to the wider urban context," she said.
Elegant Embellishments is now working on a new material, made from agricultural bio-waste, that it claims will be carbon negative.
"If you burn the material without oxygen it becomes a pure form of carbon. You are building from air and just by building you can reduce CO2," she added.
- Published4 May 2016
- Published27 April 2016
- Published25 April 2014
- Published20 April 2016
- Published13 April 2016
- Published6 April 2016
- Published6 April 2016