Mend, do and make: Can Scotland reverse its industrial decline?
- Published
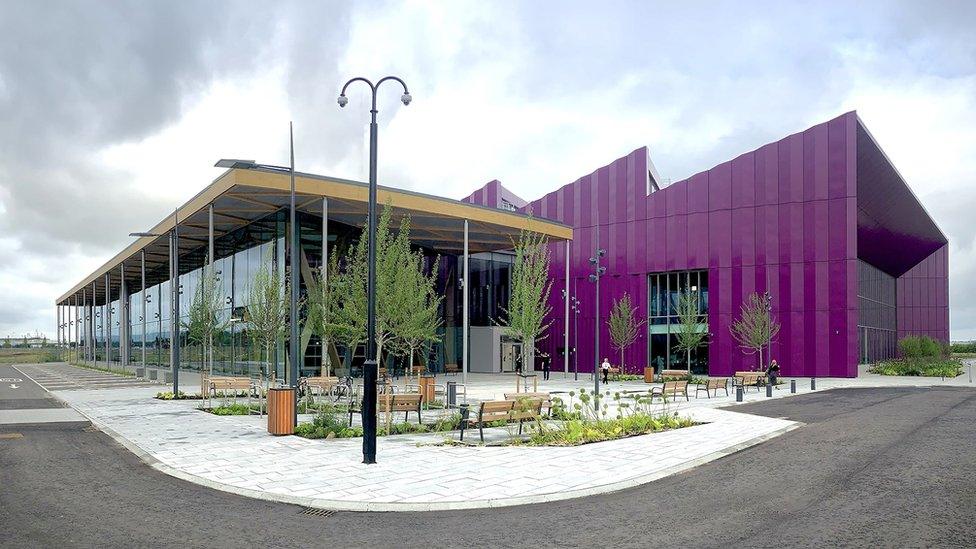
The National Manufacturing Institute Scotland in Renfrewshire
A large new focus for modern manufacturing has been opened in Renfrewshire, costing £90m and intended to reverse the decline of Scottish industrial employment.
Robotics and other automation can be a further threat to jobs, but the national institute has been set up to grow a segment of the economy that now represents only an eighth of the private sector.
Geopolitics, the pandemic and clean, green industries are reshaping manufacturing globally, so there is an opportunity there to be grasped.
Jayne Nicholl understands stress, measuring it in intricate ultra-sonic detail, and recommends other young women consider a career in it.
In her mid-twenties, she's got nine years' experience, starting with an apprenticeship, then part-time degrees at bachelor and masters level, qualifying her to advise others in how to handle, mitigate and minimise stress.
This is not emotional intelligence or counselling. Jayne is a materials engineer, and part of a 400-strong team at the forefront of a programme to claw back some of Scotland's lost prowess in manufacturing.
This is the National Manufacturing Institute Scotland. Clustered around Glasgow Airport, it has had an advanced forming and forging centre for over a decade, working with Strathclyde University to help engineers understand the stresses and strains that come from processing old and new materials.
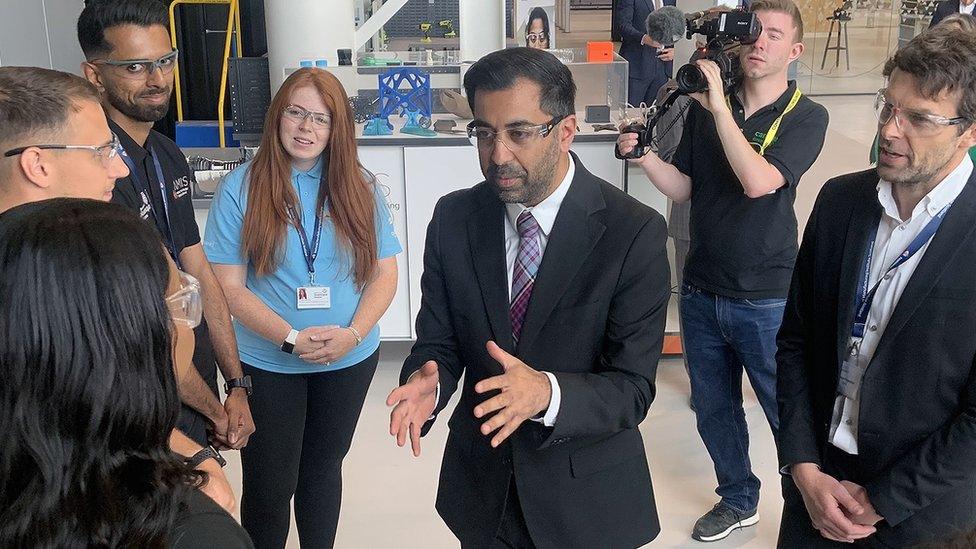
Engineer Jayne Nicholl with First Minister Humza Yousaf as he officially opened the centre
A large new building has become its headquarters, opened this week by the First Minister, it's designed to be a bold icon of Scottish hopes for a manufacturing revival.
In a striking purple, its sawtooth roof is a reminder of factory design past, though covered in solar panels, while a long glass wall opens out to Renfrewshire sunshine, and a few metres away, another new research centre for the making of medicines.
On the shop floor of the new centre, robots and cobots (collaborative robots, with sensors helping them to respond to things happening around them) demonstrate 3D printing, engraving of silicon wafers, testing aero-engine blades, and constructing each electronic layer packed into a miniature satellite.
Robotics
It can seem a long way from conventional views of manufacturing as metal-bashing and welding. That's partly because the Scottish economy is a long way from its manufacturing heyday.
Only one job in 15 is now in this sector. Sixty years ago, there were around 750,000 Scots employed in making things here.
Heavy industry took a heavy pounding from foreign competition and a harsh regime of economic change. In came foreign investors, making computers in Greenock and cash machines in Dundee.
'Silicon Glen' brought many jobs in assembly, drawing more women into manufacturing, often in Scotland's New Towns. But few had sufficiently deep roots to withstand the powerful forces of globalisation.
Much of that work shifted to eastern Europe and Asia. Some firms moved on to higher value jobs, servicing the users of those computers from Scotland and developing new products, in alliances with Scottish universities.
In 1996, there were 343,000 Scots in manufacturing. But the most recent official figures indicate only 178,000. That's less than a quarter of the workforce of people making things only 60 years ago.
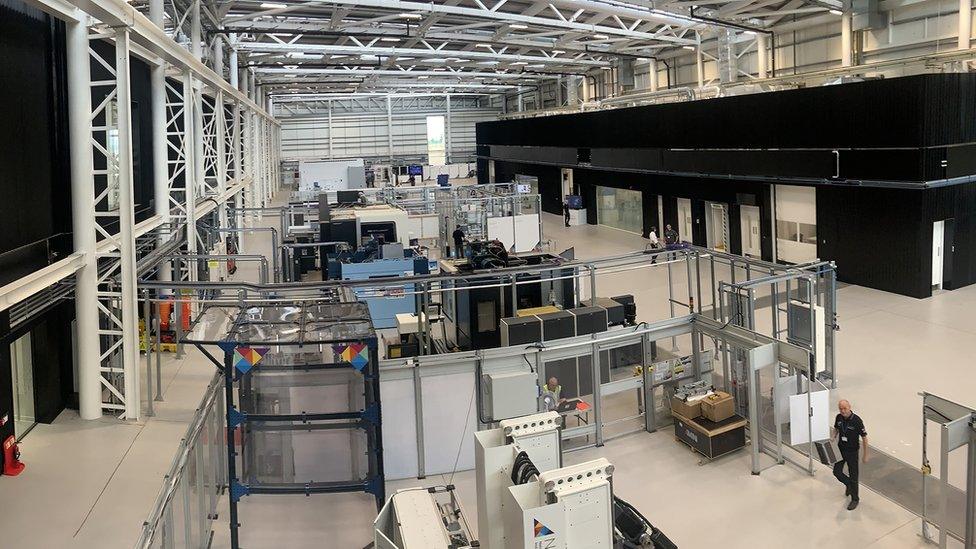
The centre is designed to be a an icon of Scottish hopes for a manufacturing revival
Those NMIS robots indicate one reason for the decline. Manufacturing involves ever greater depths of automation. People have been getting replaced by machines since the start of the first industrial revolution.
NMIS chief executive Chris Courtney is confident the current generation of robots won't reduce manufacturing employment but enhance it. There are more roles to be had in programming and working with robots, he argues.
And where skill shortages are a feature of the economy, automation offers an obvious answer.
While there has been a decline in job numbers, the share of manufacturing for the economy has fallen by similar levels. In common with many other developed countries, the service sector - finance to tourism to culture - has grown to become the overwhelming presence.
The most recent measure of gross value added, point to 59% of the private sector economy being in services. The primary sector (oil and gas extraction, as well as fishing and farming) accounts for 19%.
Construction is around 8% of private firm activity, by value added, and manufacturing is at 13% - an eighth of the private sector - or £13 billion.
Glasgow satellites
And what do Scots make now? A wide variety of products. Some might say it's too wide, and lacks specialisation.
Shipbuilding is an example of that. What Scotland has long done with ships is to make highly complex warships or bespoke designs.
The warship business depends on protection from foreign competition, and Ferguson shipyard in Port Glasgow can demonstrate what goes wrong with bespoke design.
Foreign competition is producing ferries or offshore energy jackets in large numbers on an assembly line.
To go back to the first industry, textiles, there are still specialist suppliers of high-end garments in cashmere, and calfskin for luxury airline seats, but that now accounts for only 2% of manufacturing output.
Far bigger is the drinks industry, mainly in whisky, but also other spirits and beer, accounting for nearly a fifth of what Scotland makes, measured by value.
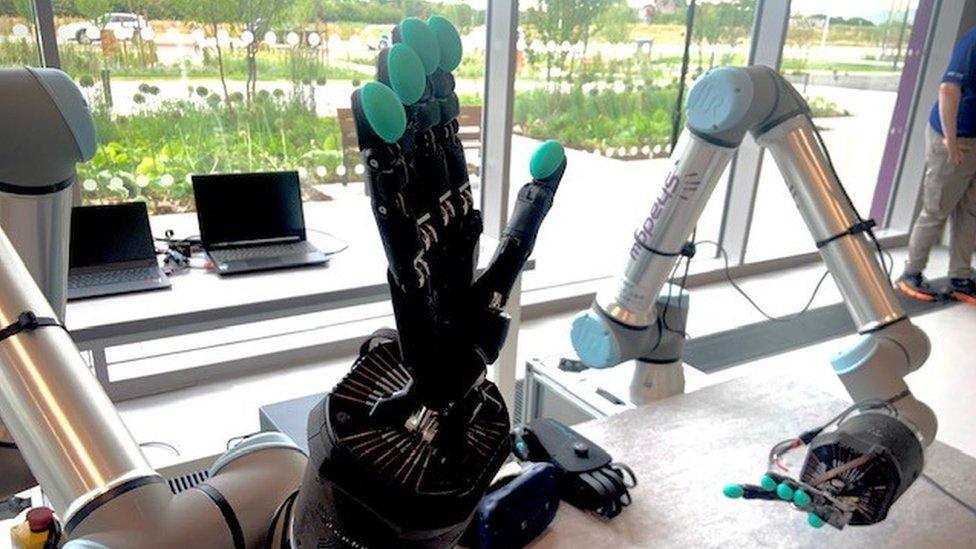
Robots and cobots demonstrate a variety of skills at the centre
Food is around a tenth, including baking and dairy for local consumption, also including processed fish and shortbread for export.
Chemicals, much of that sector in Grangemouth, are classified with pharmaceuticals, at which Scotland has some big plants, from Irvine to Montrose, and medical devices in Inverness. That's around a fifth of Scottish manufacturing.
As Chris Courtney points out, manufacturing does not focus on city centres the way it once did and the way services tend to do. It spreads economic benefit quite widely.
Metals, machinery and transport form a further fifth of output by value, much of that making equipment for offshore energy. In Prestwick, they make leading edges for the wings of Boeing and Airbus planes. In Falkirk, it's double-deck buses, for export to North America and the Pacific rim.
Electronics has fallen from a huge presence making hardware for the European market to only 8% of manufacturing. This is not just the residue of Silicon Glen from the end of last century, but new industries, notably including space. Glasgow has a world-leading cluster of activity making small satellites.
Friend-sharing
Where Jayne Nicoll has seen change in her short career at the NMIS, it has been towards use of lighter materials, often to meet the requirements of reduced carbon emissions. Companies want to find how to process with more efficient use of expensive energy, wasting less, recycling more and making new products for the renewable energy industry.
What Chris Courtney also sees are the lessons of the pandemic, and a growing nervousness about dependence on stretched global supply chains.
The move towards service economies, he says, has been checked by the evident need for resilience when pandemic struck and we needed protective clothing and vaccinations.
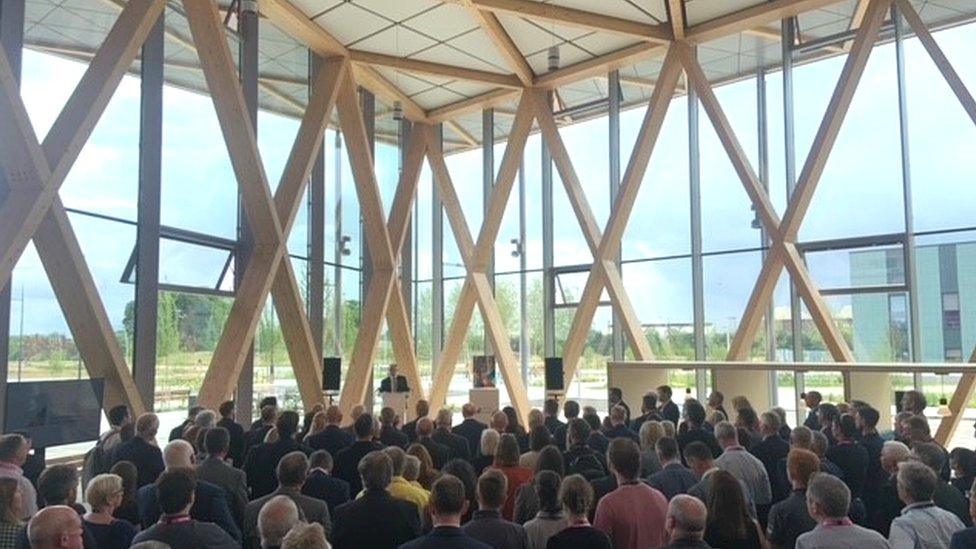
A 400-strong team is at the forefront of a programme to claw back Scotland's lost prowess in manufacturing
Geo-politics plays a compelling part too. The pandemic taught a valuable lesson in what happens when microchip production is disrupted. Car production and much else besides was hugely affected.
And with Taiwan a dominant producer of microchips, its vulnerability to China causes worry not only to military strategists but to economic ones too.
Offshoring of manufacturing is seeing a reversal in strategic industries towards re-shoring, near-shoring or 'friend-sharing' - shifting production from potential enemies to reliable allies.
The US drive to dominate green technologies, using subsidy and requirements for locally-manufactured content is a signal to others to follow, including the European Union.
The UK government is so far unsure how to respond, and industry warns that its hesitation could cost it dear in grabbing the big manufacturing projects to come, including batteries.
It means a new generation of manufacturing is being created, in which government intervention is to be expected if strategic industries are to thrive.
NMIS is one such strategic investment, with a £90m development cost including £20m of equipment, and most of that from government funds. It carries high hopes, that Scots can return to a future busier with making things.