Will 3D printing revolutionise manufacturing?
- Published
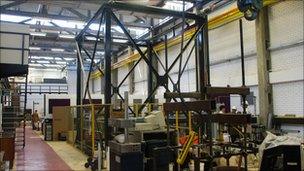
Loughborough University's machines can even print larger structures such as building materials
With the creation of many products - including building materials - now possible at the touch of a button, will 3D printing sound the death knell for mass production?
In a way there is nothing new about 3D printing.
For several decades it has been called "rapid prototyping": a quick way of making one-off items from fused plastic or metal powder, using expensive computer-controlled lasers that are at the heart of the "printers".
But now 3D printing is coming into its own, and is being taken seriously as a manufacturing process by very big corporations.
For 100 years, the manufacturing industry has been dominated by the idea of mass production.
That was devised by Henry Ford in Detroit in the early 1900s to tackle a severe shortage of skilled labour when he wanted to start making the revolutionary Model T automobiles.
Ford's factories melted iron ore, stamped out car bodies, used interchangeable parts to turn out millions of cars in, as the famous phrase has it, "any colour so long as it's black".
The moving production line came to be the emblem of the new manufacturing era, generating torrents of products and foods for a new mass market of consumers.
But now 3D printing is beginning to change the mass production model that so dominated the 20th century.
It is now called additive manufacturing, to distinguish it from old-fashioned subtractive manufacturing, that is the shaving away or moulding blocks of raw metal to make engineered components.
You might have laughed if 100 years ago In Business had come back from Detroit convinced that Ford had successfully combined the idea of interchangeable parts from the American small arms industry with the moving line from the slaughterhouses of Chicago meat packers to create a revolutionary system of mass production that would be adopted almost everywhere else in business.
But what Henry Ford started was no joke, and nor is 3D printing today.
You get some sense of the potential from the pioneers at Loughborough University.
'Cost effective'
Neil Hopkinson is senior lecturer in the Additive Manufacturing Research Group.
His lab is full of impressive 3D printing machines, decked out with samples of the work they are trying out.
Dream maker: New manufacturing techniques make product design an accessible reality
From demonstrating trial components, it does not take long before he is talking about the huge impact the process could have on the way businesses work.
"It could make off-shore manufacturing half way round the world far less cost effective than doing it at home, if users can get the part they need printed off just round the corner at a 3D print shop on the high street.
"Rather than stockpile spare parts and components in locations all over the world," he argues, "the designs could be costlessly stored in virtual computer warehouses waiting to be printed locally when required."
Just across the Loughborough campus at the Civil and Building Engineering Department is Neil's colleague Richard Buswell, who shows me an extraordinary three-storey rig designed to "print" buildings.
It squirts concrete out of a nozzle controlled by a computer, using the concrete just like a conventional printer would use ink, but in three dimensions, building up a structure layer by layer.
The construction industry is rather conservative; many building sites still look much as they did in Roman times.
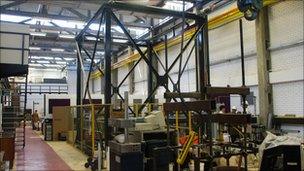
Loughborough University's machines can even print larger structures such as building materials
If Richard and his colleagues can prove it works at Loughborough - and convince potential users - additive manufacturing could change the industry.
One potentially big change, in construction as in other activities, is to place designers right at the centre of activity.
"Rapid manufacturing is all about putting the power of making things back in the hands of the architects," says Richard Buswell.
"Young architects currently training are the ones who will take the techniques through into mainstream architecture."
The EADS aircraft plant near Bristol is already exploiting this technology, and announced earlier this year that it had used additive layer manufacturing to produce a bike, external.
When I was there I saw machines turning out complex satellite parts which are lighter in weight and cheaper to make than conventionally-machined components.
'Disruptive' potential
"It's new materials, it's new design processes, it's a new way of looking at manufacturing," says Ian Risk, head of Innovation Works at EADS in the UK.
"We have had the processes of subtractive manufacturing built into our ways of working, the way we think about components from the outset. We could change things significantly, and save money."
But first entrenched companies will have to wake up to the potential of the process.
That may be an uncomfortable experience for most business people, trained and practiced in the mass production way of doing things.
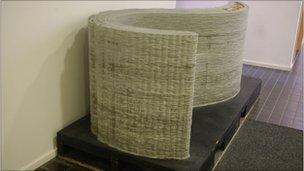
3D printing puts the designer at the centre of the process when creating items like this bench
Engineer Will Sillar is a partner at the Legerwood management consultancy which advises companies on 3D printing, something he believes has all sorts of disruptive potential:
"Up to 50 percent of the working capital of a business is currently tied up in stock and working capital," he says.
"Eliminate that, and the finance director is going to be the happiest man in the world."
But introducing disruptive change is not an easy thing to do, warns Stuart Jackson, UK manager of the German company EOS, a leading maker of 3D manufacturing machines.
"If you've spent years in your career to establish a manufacturing process, and then something comes along that could throw it out of the window, it's not necessarily attractive.
"It needs to be an open mind to actually take it on board."
3D printing may have reached that vital threshold. Now it needs companies and people who are open-minded enough to turn upside down the traditional ways of making things and, eventually, of running businesses.
In Business is on BBC Radio 4 on Thursday 28 July at 2030 BST and Sunday 31 July at 2130 BST. You can also listen via the BBC iPlayer or the podcast.
- Published5 July 2011
- Published25 November 2010
- Published6 December 2010
- Published30 April 2010